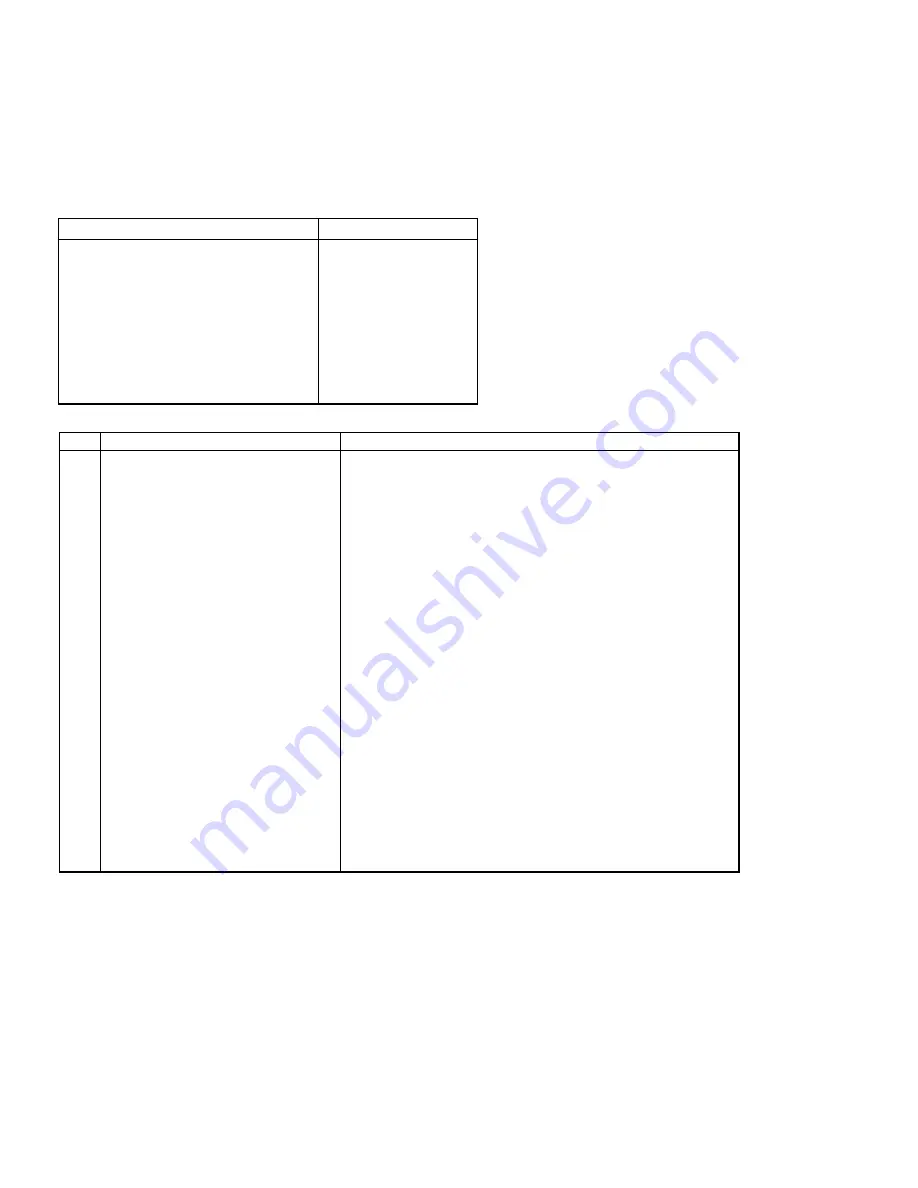
36 FD151 Gas Compressor
In most cases problems with your Corken Gas Compressor can
be solved quite simply. This chart lists some of the more
frequent problems that occur with reciprocating compressors
along with a list of possible causes. If you are having a problem
which is not listed or if you cannot find the source of problem,
consult the Factory.
PROBLEM
POSSIBLE CAUSES
Low Capacity
1, 2, 3, 4, 17
Overheating
1, 2, 3, 5, 6, 11, 16
Knocks, Rattles and Noise
1, 7, 9, 10, 11, 15
Oil in Cylinder
8, 12, 15
Abnormal Piston Ring Wear
1, 3, 5, 6, 11, 15, 16
Product Leaking Through Crankcase Breather
8, 15
Product Leakage
4, 8, 15, 17
Oil Leakage Around Compressor Base
18, 19
No Oil Pressure
20, 21
Excessive Vibration
1, 7, 9, 10, 11, 13, 14, 29
Motor Overheating or Starter Tripping Out
22, 23, 24, 25, 26, 27, 28, 29
Two-Stage Compressors can have problems that never occur
with single-stage machines. Interstage pressure is an important
indicator of the condition of a
two-stage Compressor.
Interstage pressure is too high:
1. Second stage valves may be broken or leaking.
2. Second stage piston rings may be worn.
Interstage pressure is too low:
1. First stage valves may be broken or leaking.
2. First stage piston rings may be worn.
Another cause for high interstage pressure is a low compression
ratio. Two-Stage machines should not be used in applications
where the compression ratio is below 5. To use Two-Stage
Compressor in this kind of situation results in rapid ring wear,
machine imbalance and excessive horsepower. If you think you
have a problem in this area, consult Factory.
TWO-STAGE COMPRESSOR TROUBLESHOOTING
GENERAL
REF.
POSSIBLE CAUSES
SOLUTIONS
1.
Valves broken, stuck or leaking
Inspect and clean or repair
2.
Piston ring worn
Inspect and replace as necessary
3.
Inlet strainer clogged
Clean or replace screen as necessary
4.
Leaks in piping
Inspect and repair
5.
Inlet or ambient temperature too high
Consult Factory
6.
Compression ratio too high
Check Application and consult Factory
7.
Loose flywheel or belt
Tighten
8.
Worn piston rod packing
Replace
9.
Worn wrist pin or wrist pin bushing
Replace
10.
Worn connecting rod bearing
Replace
11.
Unbalanced load
Inspect valve or consult Factor
12.
Oil in distance piece
Tighten packing nut - drain weekly
13.
Inadequate compressor base
Strengthen, replace or grout
14.
Improper foundation or mounting
Tighten mounting or rebuild foundation
15.
Loose valve, piston or packing
Tighten or replace as necessary
16.
Dirty cooling fins
Clean weekly
17.
Leaking gas blowing oil from crankcase
Tighten packing
18.
Bad oil seal
Replace
19.
No oil in crankcase
Add oil
20.
Oil pump malfunction
See oil pressure adjustment
21.
Low voltage
Check line voltage with motor nameplate. Consult Power Company
22.
Motor wired wrong
Check wiring diagram
23.
Wire size too small for length of run
Replace with correct size
24.
Wrong power characteristics
Voltage, phase and frequency must coincide with motor nameplate. Consult with
Power Company.
25.
Wrong size of heaters in starter
Check and replace according to manufacturer’s instructions
26.
Compressor Overloading
Reduce speed
27.
Motor shorted out
See driver installation
28.
Bad motor bearing
Lubricate according to manufacturer’s instructions
GENERAL COMPRESSOR TROUBLESHOOTING
APPENDIX J