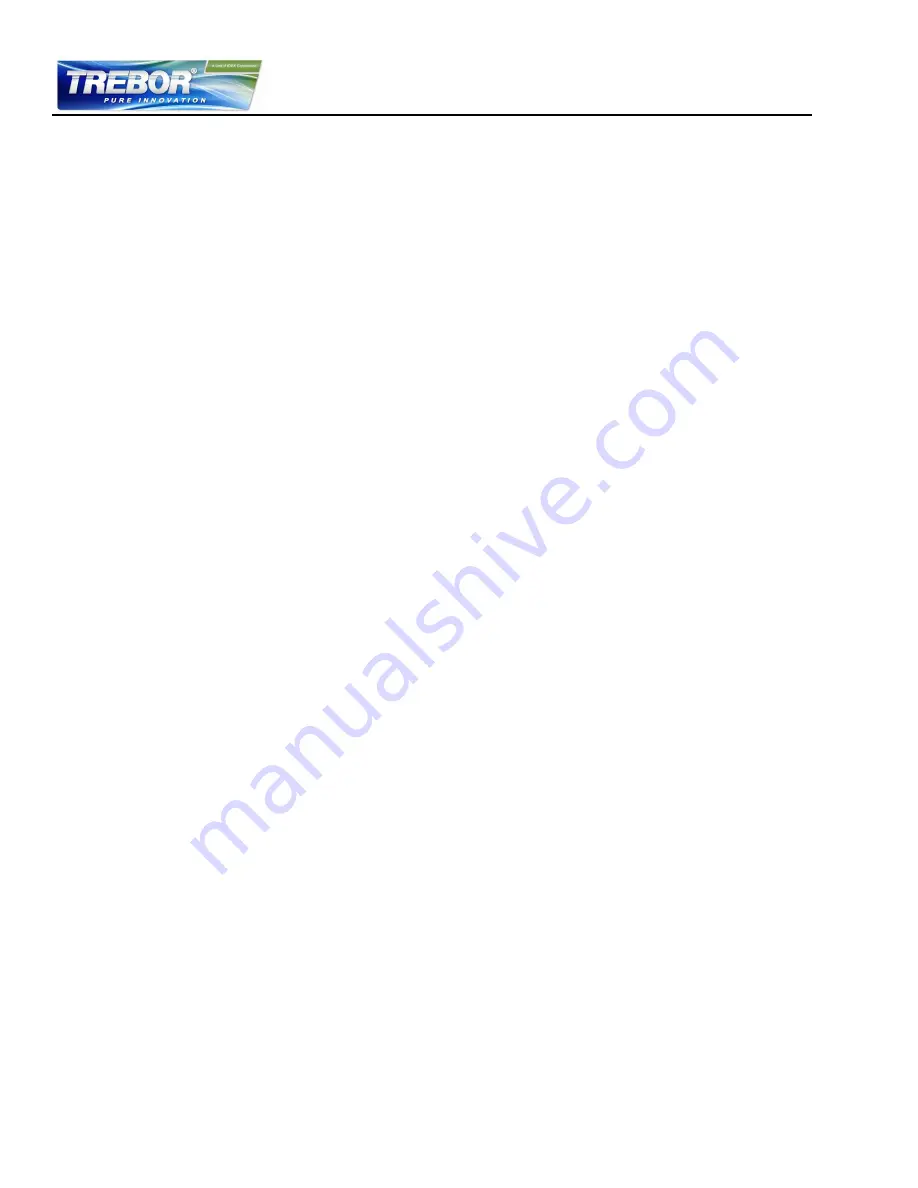
REV6 OPERATION / MAINTENANCE MANUAL
22
CONTENTS
3.5 Hydraulic Circuit Design
Follow these general design rules for the hydraulic circuit will yield more robust pump operation and
optimum priming:
1. The general rule for optimum priming behavior is to minimize the pressure drop in the inlet
circuit and avoid negative pressure at the inlet of the pump.
2. Minimize tubing length and maximize the tubing ID at the inlet of the pump. This reduces the
pressure drop and the tendency of cavitation.
3. Avoid any restrictions, valves, elbows, bended tubing and sharp edges at the inlet circuit of the
pump, which could potentially cause cavitation resulting in gas bubble collection in the pump
and potential priming loss.
4. Place the pump at the lowest point of the hydraulic circuit. Optimum is as much as possible
below a tank or reservoir. This optimizes priming behavior and removal of gas bubbles.
5. Keep the liquid level in the reservoir as high as possible, which increases the inlet pressure of
the pump and minimizes fluid heating.
6. In general, the pump system placement and circuit shall be designed such that gas bubbles can
leave the pump housing so the pump remains primed.
7. To minimize fluid heating, the overall pressure drop in the hydraulic circuit should be reduced as
much as possible.
8. Deadhead operation (pump operation when the discharge valve is closed) should be avoided. It
can cause heat-up of the liquid.
9. Optimization of the fluid circuit becomes more important as the fluid temperature increases due
to the higher cavitation tendency of the liquid.
Contact Trebor (see Section 8) for additional considerations and support on the hydraulic circuit design.