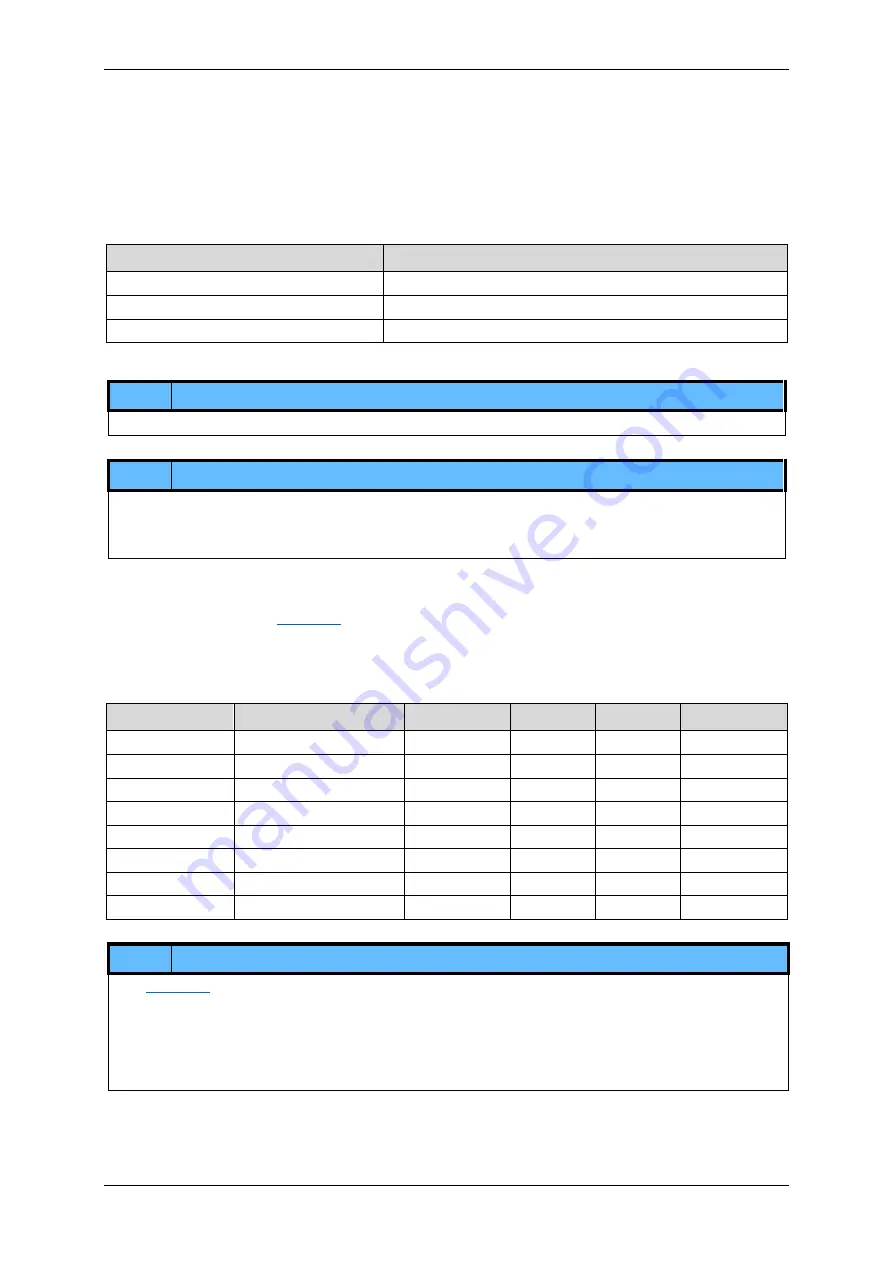
Initial Operation
D8-3_EN
– V1.0
11/14
4.1.2
Standstill Current and Autotuning
If the enable signal is set but no motion command is present, the motor current set via switches SW1 to SW3 is reduced to 50%
(SW7 ON) or 90% (SW7 OFF) at standstill.
The auto-tuning function allows the motor controller to be optimally adapted to the connected motor. If this is performed, the
internal control parameters are tuned to ensure a high torque output even at high rpm, as well as generally quiet and low-
vibration operation.
If autotuning is started, the green status LED switches off for the duration of the parameter determination. Autotuning has been
successfully performed when the green status LED lights up again. This process takes approx. 3 seconds.
Standstill Current
SW7
50 % of preselected Motor Current-
ON
90 % of preselected Motor Current-
OFF
Start Autotuning
OFF
– ON – OFF within 1 second
NOTE
Autotuning can only be started if switch SW7 has been set to OFF for at least 1 second.
NOTE
Autotuning should always be performed when:
-
The motor control unit is used for the first time.
-
The motor controller's supply voltage changes
-
A different motor is connected to the motor controller
4.1.3
Micro-Stepping
If the motor controller is used in
(p.13), the desired micro step mode must be preselected by the combination of
switch SW4 to SW6 and SW 8.
By preselecting the micro steps per motor revolution, the precision, the resulting vibrations, and the noise of the motor can be
directly influenced.
The higher the micro steps, the better the precision and at the same time vibrations and noise are reduced to a minimum.
Micro Step
Step mode
SW4
SW5
SW6
SW8
200
1/1 Full Step
ON
ON
ON
ON
400
1/2 Step
OFF
ON
ON
ON
800
1/4 Step
ON
OFF
ON
ON
1600
1/8 Step
OFF
OFF
ON
ON
3200
1/16 Step
ON
ON
OFF
ON
6400
1/32 Step
OFF
ON
OFF
ON
12800
1/64 Step
ON
OFF
OFF
ON
25600
1/128 Step
OFF
OFF
OFF
ON
Note
(p.13) is used, the selection of the executed micro steps per motor revolution in the master controller and
in the motor controller must be the identical.
If, for example, 200 micro steps per motor revolution are set in the motor controller, but 400 micro steps per motor revolution
are set in the master controller, and the master controller issues the movement command for one motor revolution, the motor
will execute 2 revolutions.
The reason for this is that instead of the 200 pulses expected by the motor controller for one motor revolution, 400 pulses
were now emitted by the master controller and these were converted into 2 motor revolutions.