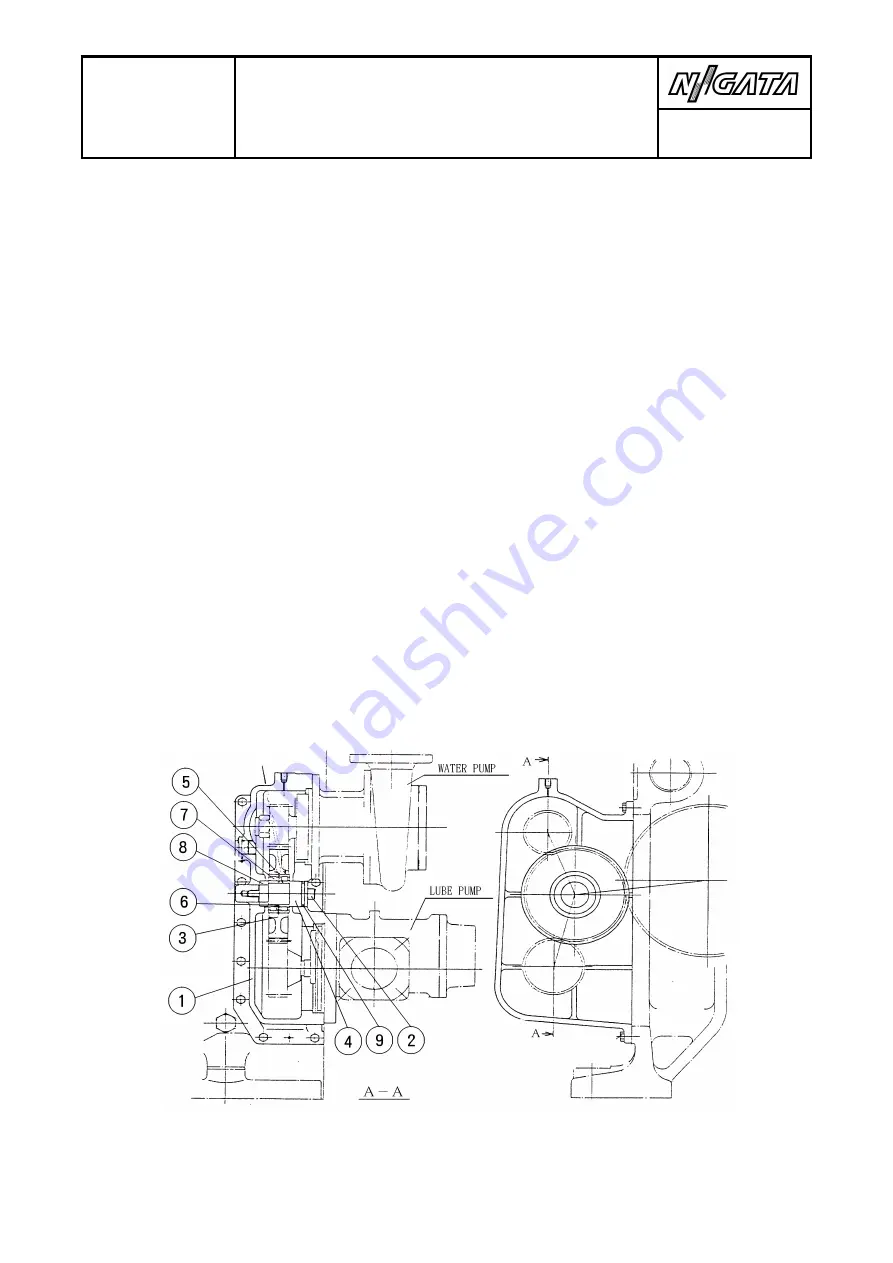
This document is property of NIIGATA POWER SYSTEMS CO., LTD. It must be neither reproduced nor communicated nor published without permission.
SECTION
4
- DISASSEMBLY AND REASSEMBLY
4.8 CAMSHAFT AND TIMING GEAR TRAIN
4-8-05
Reassembly
- Before installing the roller bearings back onto the shaft, coat the bearing
outer diameter and the inner diameter of the gear bore with Locktite 601 or
equivalent. Make certain that the Locktite does not enter the bearing cage.
- Complete the reassembly in the reverse order of disassembly.
Lube Oil Pump Idler Gear Bearings
The lube oil pump idler gear can be removed as follows:
- Remove the housing
①
, bolt
②
, then support the gear by hand while
removing the shaft
④
.
- Place the gear assembly on a workbench and remove the bearings with the same
procedure as described for the main idler gears above.
- Reinstallation of the bearings is the same as outlined above for the main
idler gears. Install a new o-ring seal
⑨
on the shaft.
- After the bearings have been reinstalled in the gear, hold the gear in the
housing and insert the shaft. Tighten the retaining bolt
②
to the settled
torque.
Summary of Contents for NIIGATA MG(L)26HLX
Page 2: ......
Page 34: ......
Page 38: ......
Page 40: ......
Page 60: ......
Page 66: ......
Page 68: ......
Page 80: ......
Page 82: ......
Page 86: ......
Page 88: ......
Page 94: ......
Page 107: ......
Page 108: ......
Page 110: ......
Page 130: ......
Page 132: ......
Page 170: ......
Page 174: ......
Page 186: ......
Page 188: ......
Page 192: ......