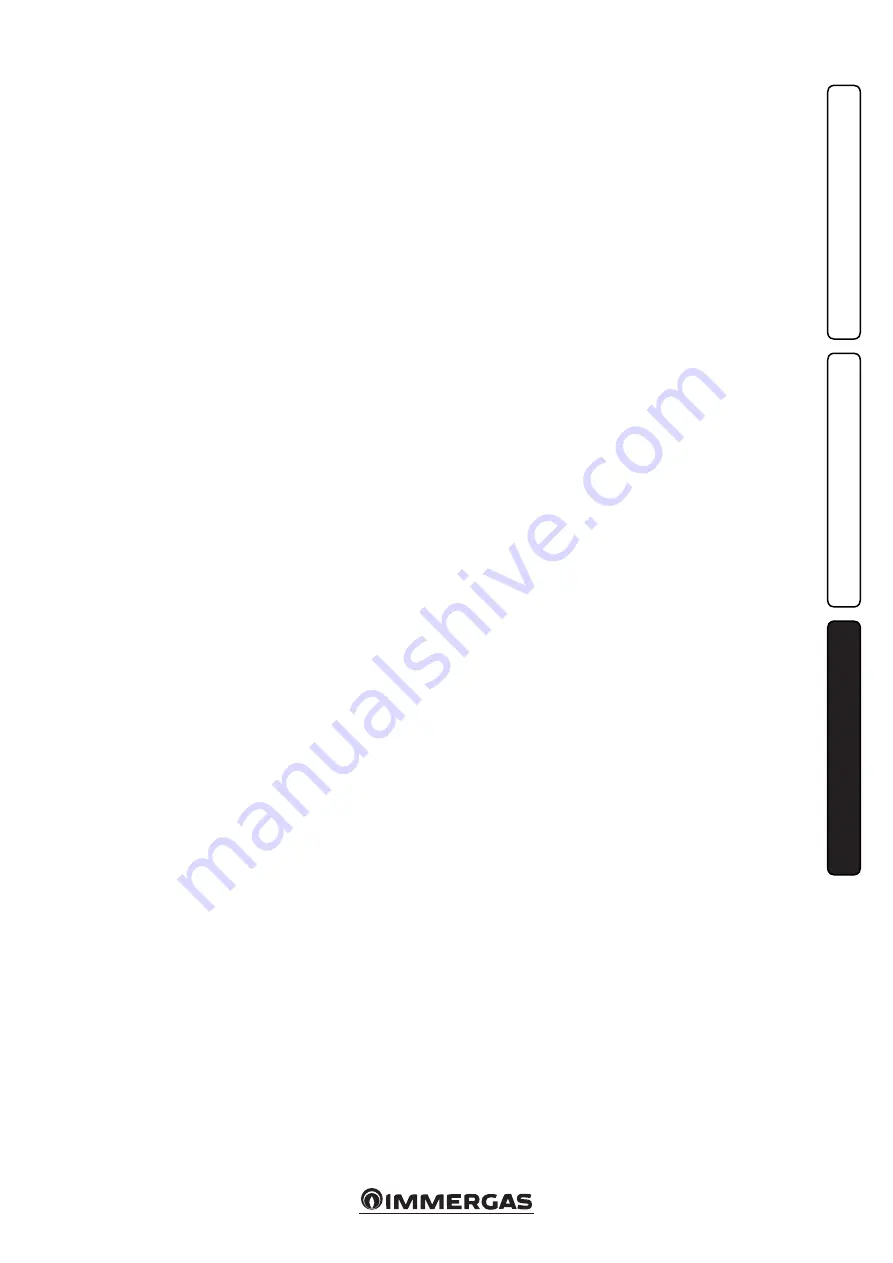
37
INS
TALLER
US
ER
MAINTEN
AN
CE TECHNI
CI
AN
3.16 SOLAR PANELS COUPLING
FUNCTION.
Attention: to install the kit (solar panels) cor-
rectly, you must move the DHW probe (26 Fig.
1-28), in the upper seat of the storage tank.
The boiler is set-up to receive pre-heated water
from a solar panels system up to a maximum
temperature of 65 °C. In any case, it is always
necessary to install a mixing valve on the hydrau-
lic circuit upstream of the boiler. Set the “P71”
function on “P71.1” (Par. 3.8).
When the boiler inlet water temperature is equal
to or greater than that set by the domestic hot
water selector switch “SET”, the boiler does not
switch on.
3.17 YEARLY APPLIANCE CHECK AND
MAINTENANCE.
The following checks and maintenance should
be performed at least once a year.
- Clean the flue side of the heat exchanger.
- Clean the main burner.
- If deposits are detected in the combustion
chamber they must be removed and the heat
exchanger coils must be cleaned using nylon
or broomcorn brushes; it is forbidden to use
brushes made of metal or other materials that
may damage the combustion chamber.
- Check the integrity of the insulating panels
inside the combustion chamber and if damaged
replace them.
- Visually check for water leaks or oxidation
from/on fittings and traces of condensate
residues inside the sealed chamber.
- Check contents of the condensate drain trap.
- Via the condensate drain cap check that there
are no residues of material that clog condensate
passage; also check that the entire condensate
drain circuit is clear and efficient.
In the event of obstructions (dirt, sediment,
etc.) with consequent leakage of condensate
in the combustion chamber, one must replace
the insulating panels.
- Check that the burner seal gaskets and the lid
are intact and perfectly efficient, otherwise
replace them. In any case the gaskets must be
replaced at least every two years, regardless of
their state of wear.
- Check that the burner is intact, that it has no
deformations or cuts and that it is properly
fixed to the combustion chamber lid; otherwise
it must be replaced.
- Visually check that the water safety valves drain
is not blocked.
- Check, after discharging the system pressure
and bringing it to zero (read on boiler pressure
gauge), that the expansion vessel charge is at 1.0
bar.
- Check that the domestic hot water expansion
vessel charge is at a pressure between 3 and 3.5
bar.
- Check that the system static pressure (with
system cold and after refilling the system by
means of the filling cock) is between 1 and 1.2
bar.
- Visually check that the safety and control
devices have not been tampered with and/or
shorted, in particular:
- temperature safety thermostat;
- system pressure switch.
- Check integrity of the boiler Magnesium anode.
- Check the condition and integrity of the electri-
cal system and in particular:
- supply voltage cables must be inside the
fairleads;
- there must be no traces of blackening or
burning.
- Check ignition and operation.
- Check correct calibration of the burner in
domestic hot water and central heating phases.
- Check the operation of the appliance control
and adjustment devices and in particular:
- intervention of the main electrical switch on
the boiler;
- system control thermostat intervention;
- domestic hot water control thermostat inter-
vention.
- Check sealing efficiency of the gas circuit and
the internal system.
- Check the intervention of the device against
no gas ionisation flame control. The relative
intervention time must be less than 10 seconds.
N.B.:
in addition to yearly maintenance, one
must also check the thermal system, with fre-
quency and procedures that comply with the
indications of the technical regulations in force.