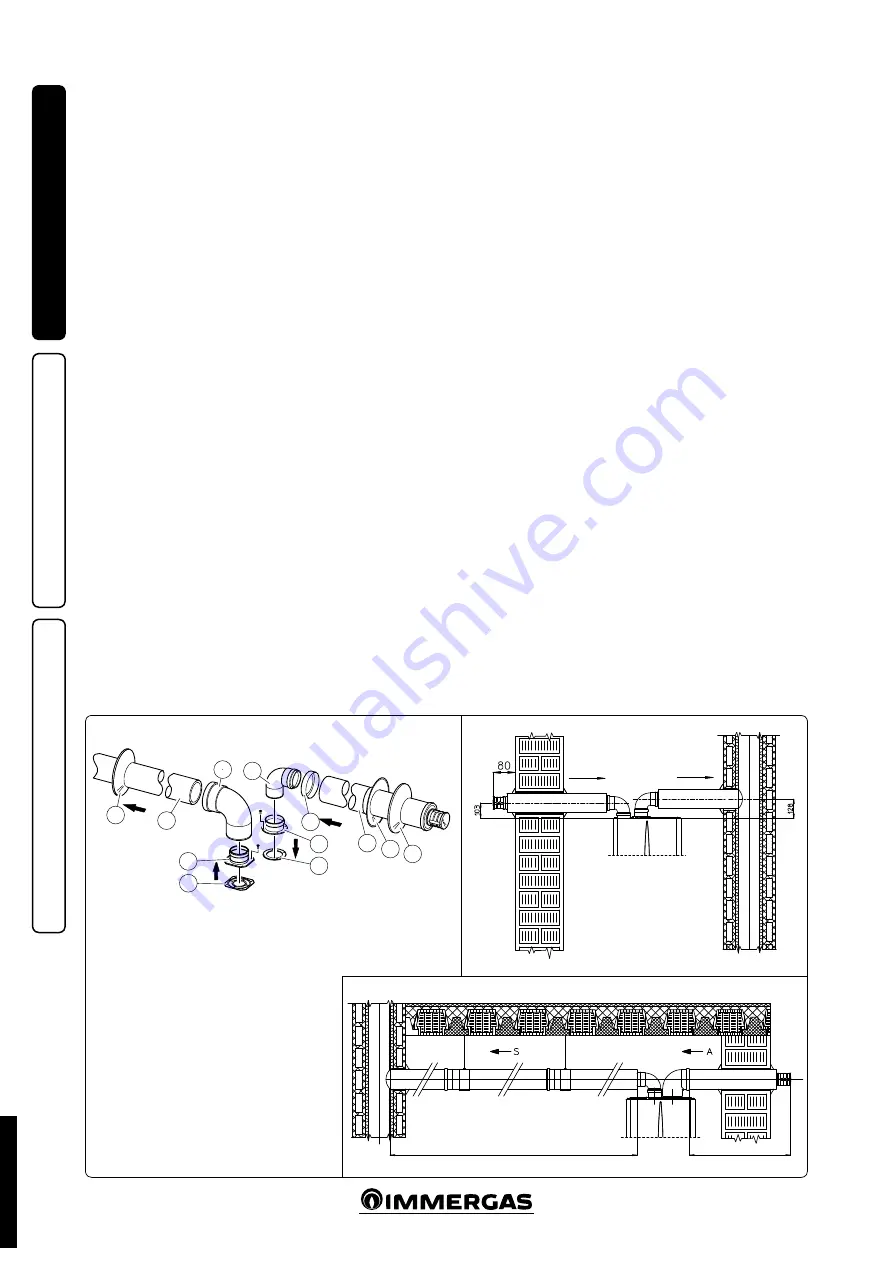
16
C
82
1-26
1-27
C
82
C
82
1-25
A
S
1
8
10
11
5
7
3
2
S
A
4
8
9
6
INS
TALLER
US
ER
MAINTEN
AN
CE TECHNI
CI
AN
• Temperature loss in flue ducts (Fig. 1-24). To
prevent problems of flue gas condensate in the
exhaust pipe Ø 80, due to fume cooling through
the wall,
the length of the exhaust pipe must be
limited to just 5 metres.
If longer distances must
be covered, use Ø 80 pipes with insulation (see
insulated separator kit Ø 80/80 chapter).
Insulated separator kit Ø 80/80.
Kit assembly
(Fig. 1-25): install the flange (4) on the central
hole of the boiler, interposing the gasket (1) and
tighten with the flat-tipped hex screws included
in the kit. Remove the flat flange present in the
lateral hole with respect to the central one (ac-
cording to needs) and replace it with the flange
(3), positioning the gasket (2) already present in
the boiler and tighten using the supplied self-
threading screws. Insert and slide cap (6) onto
bend (5) from the male side (smooth), and join
bends (5) with the male side (smooth) in the
female side of flange (3). Fit bend (11) with the
male side (smooth) into the female side of flange
(4). Fit the male end (smooth) of the intake ter-
minal (7) up to the stop on the female end of the
bend (5), making sure you have already inserted
the wall sealing plates (8 and 9) that ensure cor-
rect installation between pipe and wall, then fix
the closing cap (6) on the terminal (7). Join the
exhaust pipe (10) with the male side (smooth)
in the female side of the bend (11) to the end
stop, ensuring that the wall sealing plate (8) is
already inserted for correct installation between
the pipe and flue.
• Insulation of separator terminal kit. Whenever
there are flue gas condensate problems in the
exhaust pipes or on the external surface of the
intake pipes, on request Immergas supplies
insulated intake-exhaust pipes. Insulation
my be necessary on the exhaust pipe, due to
excessive loss of temperature of the flue gas on
their route. Insulation may be necessary on
the intake pipe as the air entering (if very cold)
may cause the outside of the pipe to fall below
the dew point of the environmental air. The
figures (Fig. 1-26 and 1-27) illustrate different
applications of insulated pipes.
Insulated pipes are formed of a Ø 80 internal
concentric pipe and a Ø 125 external pipe with
static air space. It is not technically possible to
start with both Ø 80 elbows insulated, as clear-
ances will not allow it. However starting with an
insulated elbow is possible by choosing either
the intake or exhaust pipe. When starting with
the insulated intake bend it must be engaged on
its flange until it is taken up to end stop on the
flue gas exhaust flange, a situation that takes the
two intake flue gas exhaust outlets to the same
height.
• Temperature loss in insulated flue ducting. To
prevent problems of flue gas condensate in the
insulated exhaust pipe Ø 80, due to flue gas
cooling through the wall,
the length of the pipe
must be limited to 12 metres.
The figure (Fig.
1-27) illustrates a typical insulation applica-
tion in which the intake pipe is short and the
exhaust pipe is very long (over 5 m). The entire
intake pipe is insulated to prevent moist air in
the place where the boiler is installed, in contact
with the pipe cooled by air entering from the
outside. The entire exhaust pipe, except the
elbow leaving the splitter is insulated to reduce
heat loss from the pipe, thus preventing the
formation of fume condensate.
N.B.:
when installing the insulated pipes, a
section clamp with gusset must be installed
every 2 metres.
MAX 12 m
The kit includes:
N°1 - Exhaust gasket (1)
N°1 - Flange gasket (2)
N°1 - Female intake flange (3)
N°1 - Female exhaust flange (4)
N°1 - Bend 90° Ø 80 (5)
N°1 - Pipe closure cap (6)
N°1 - Intake terminal Ø 80 insulated (7)
N°2 - Internal rings (8)
N°1 - External wall sealing plate (9)
N°1 - Discharge pipe Ø 80 insulated (10)
N°1 - Concentric bend 90° Ø 80/125 (11)
MAX 21 m
STD.002998/004
Summary of Contents for MAIOR EOLO 24
Page 1: ...MAIOR EOLO 24 28 32 Instruction and recommendation booklet 1 038763ENG STD 002998 004 ...
Page 2: ...STD 002998 004 ...
Page 31: ...31 3 5 6 6 7 8 8 f f e INSTALLER USER MAINTENANCE TECHNICIAN STD 002998 004 ...
Page 37: ...37 STD 002998 004 ...
Page 38: ...38 STD 002998 004 ...
Page 39: ...39 STD 002998 004 ...