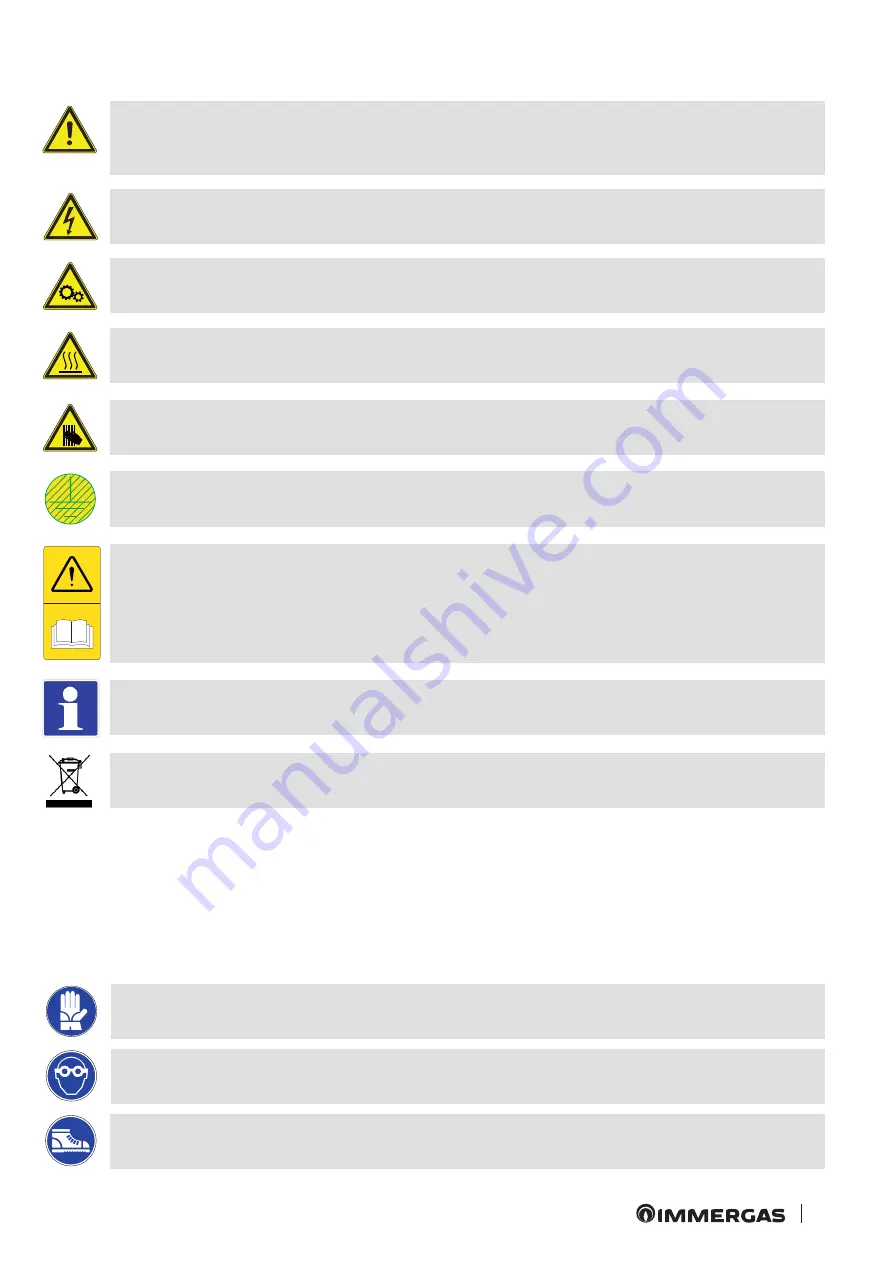
5
SAFETY SYMBOLS USED.
GENERIC HAZARD
Strictly follow all of the indications next to the pictogram. Failure to follow the indications can generate hazard situa-
tions resulting in possible harm to the health of the operator and user in general.
ELECTRICAL HAZARD
Strictly follow all of the indications next to the pictogram. The symbol indicates the appliance’s electrical components
or, in this manual, identifies actions that can cause an electrical hazard.
MOVING PARTS
The symbol indicates the appliance’s moving components that can cause hazards.
HOT SURFACES
The symbol indicates the appliance’s very hot components that can cause burns.
SHARP SURFACES
The symbol indicates the appliance’s components or parts that can cause cuts if touched.
EARTH TERMINAL CONNECTION
The symbol identifies the appliance’s earth terminal connection point.
READ AND UNDERSTAND THE INSTRUCTIONS
Read and understand the appliance’s instructions before performing any operation, carefully following the indications
provided.
INFORMATION
Indicates useful tips or additional information.
SAFETY GLOVES
PERSONAL PROTECTIVE EQUIPMENT.
SAFETY GOGGLES
SAFETY FOOTWEAR
The user must not dispose of the appliance at the end of its service life as municipal waste, but send it to appro-
priate collection centres.
Summary of Contents for NIKE ECO 24
Page 2: ...2 ...
Page 39: ...39 6 6 7 8 8 f f e 22 INSTALLER USER MAINTENANCE TECHNICIAN ...
Page 50: ...50 ...
Page 51: ...51 ...