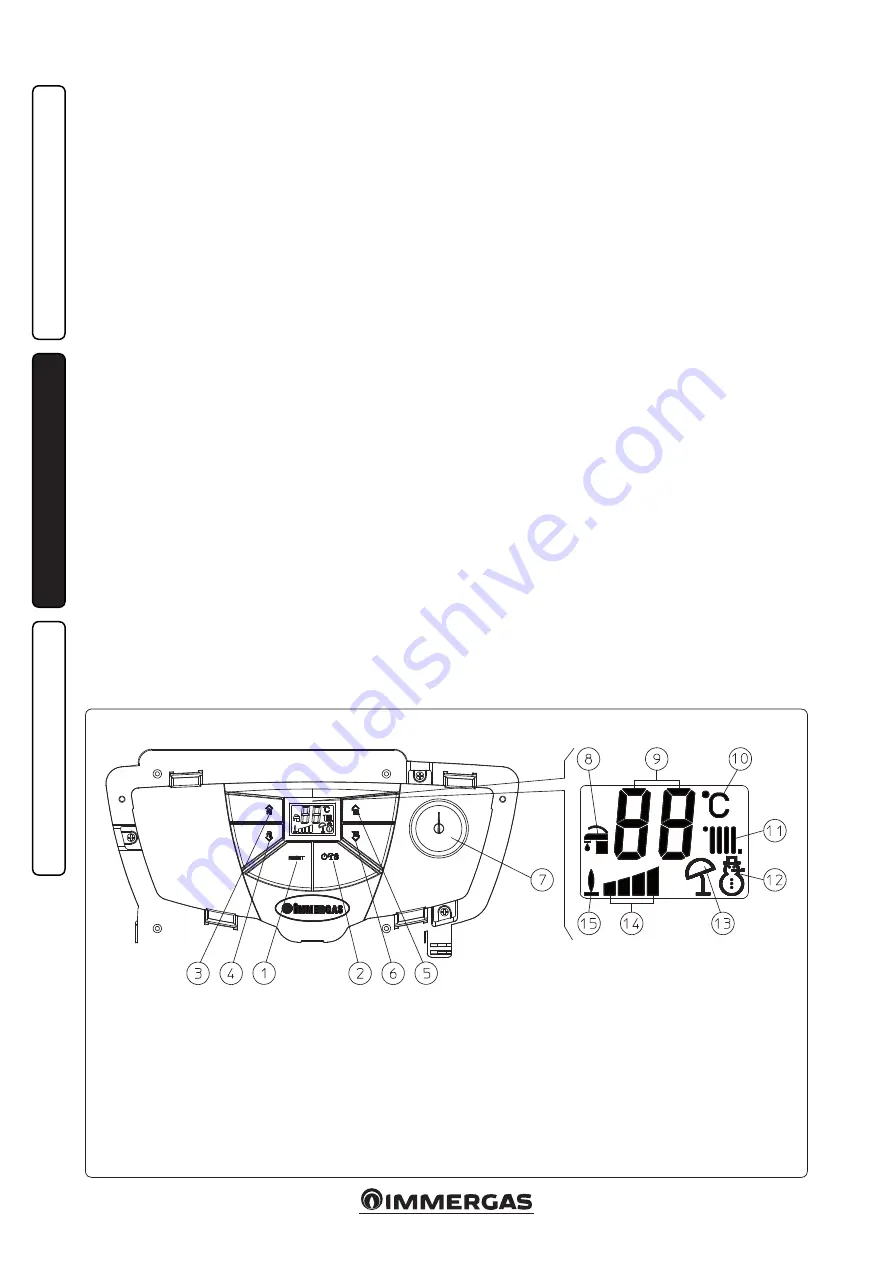
10
2-1
INS
TALLER
US
ER
MAINTEN
AN
CE TECHNI
CI
AN
2.4 CONTROL PANEL.
Key:
1 - Reset key
2 - Stand-by key/ summer / winter
3 - Key (+) to increase the domestic hot water
temperature
4 - Key (-) to reduce the domestic hot water
temperature
5 - Key (+) to increase the system water
temperature
6 - Key (-) to reduce the system water
temperature
7 - Boiler manometer
8 - Domestic hot water function
9 - Temperature and error code display
10 - Unit of measurement
11 - Heating mode
12 - Winter
13 - Summer
14 - Output efficiency
15 - Flame presence
2
INSTRUCTIONS FOR USE
AND MAINTENANCE.
2.1 CLEANING AND MAINTENANCE.
Attention:
to preserve the boiler’s integrity
and keep the safety features, performance and
reliability, which distinguish it, unchanged over
time, you must execute maintenance operations
on a yearly basis in compliance with what is
stated in the relative point at “annual check and
maintenance of the appliance”, in compliance
with national, regional, or local standards in
force.
2.2 VENTILATION OF THE ROOMS.
In the room in which the boiler is installed it
is necessary that at least as much air flows as
that requested for by normal combustion of the
gas and ventilation of the room. The provisions
relative to ventilation, the flue ducts and multiple
flues are stated in Par. 1.7 and 1.8. If in doubt re-
garding correct ventilation, refer to professional,
qualified staff.
2.3 GENERAL WARNINGS.
Never expose the suspended boiler to direct
vapours from a cooking surface.
Use of the boiler by unskilled persons or children
is strictly prohibited.
If temporary shutdown of the boiler is required,
proceed as follows:
a) drain the heating system if anti-freeze is not
used;
b) shut-off all electrical, water and gas supplies.
In the case of work or maintenance to structures
located in the vicinity of ducting or devices for
flue extraction and relative accessories, switch off
the appliance and on completion of operations
ensure that a qualified technician checks effi-
ciency of the ducting or other devices.
Never clean the appliance or connected parts
with easily flammable substances.
Never leave containers or flammable substances
in the same environment as the appliance.
It is prohibited and dangerous to obstruct the air
intake, even partially, for the ventilation of the
room in which the boiler is installed.
Due to the danger, functioning is also prohibited
in the same room as suction devices, chimneys
or similar at the same time as the boiler unless
there are additional openings dimensioned in a
way to satisfy the further necessity for air. For the
dimensioning of these additional openings, refer
to qualified technical staff. In particular, an open
fire must have its own air supply.
On the contrary, the boiler cannot be installed
in the same room.
•
Important:
the use of components involving
use of electrical power requires some funda-
mental rules to be observed:
- do not touch the appliance with wet or moist
parts of the body; do not touch when barefo-
ot;
- never pull electrical cables or leave the ap-
pliance exposed to atmospheric agents (rain,
sunlight, etc.);
- the appliance power cable must not be repla-
ced by the user;
- in the event of damage to the cable, switch
off the appliance and contact exclusively
qualified staff for replacement;
- if the appliance is not to be used for a certain
period, disconnect the main power switch.
N.B.: the temperatures indicated by the display
have a tolerance of +/- 3°C due to environmental
conditions that cannot be blamed on the boiler.
At the end of its service life, the appliance must
not be disposed of like normal household waste
nor abandoned in the environment, but must
be removed by a professionally authorised
company. Contact the manufacturer for disposal
instructions.
Summary of Contents for Nike Star 24 4 ErP
Page 18: ...18 3 4 3 2 2 4 1 INSTALLER USER MAINTENANCE TECHNICIAN ...
Page 27: ...27 ...