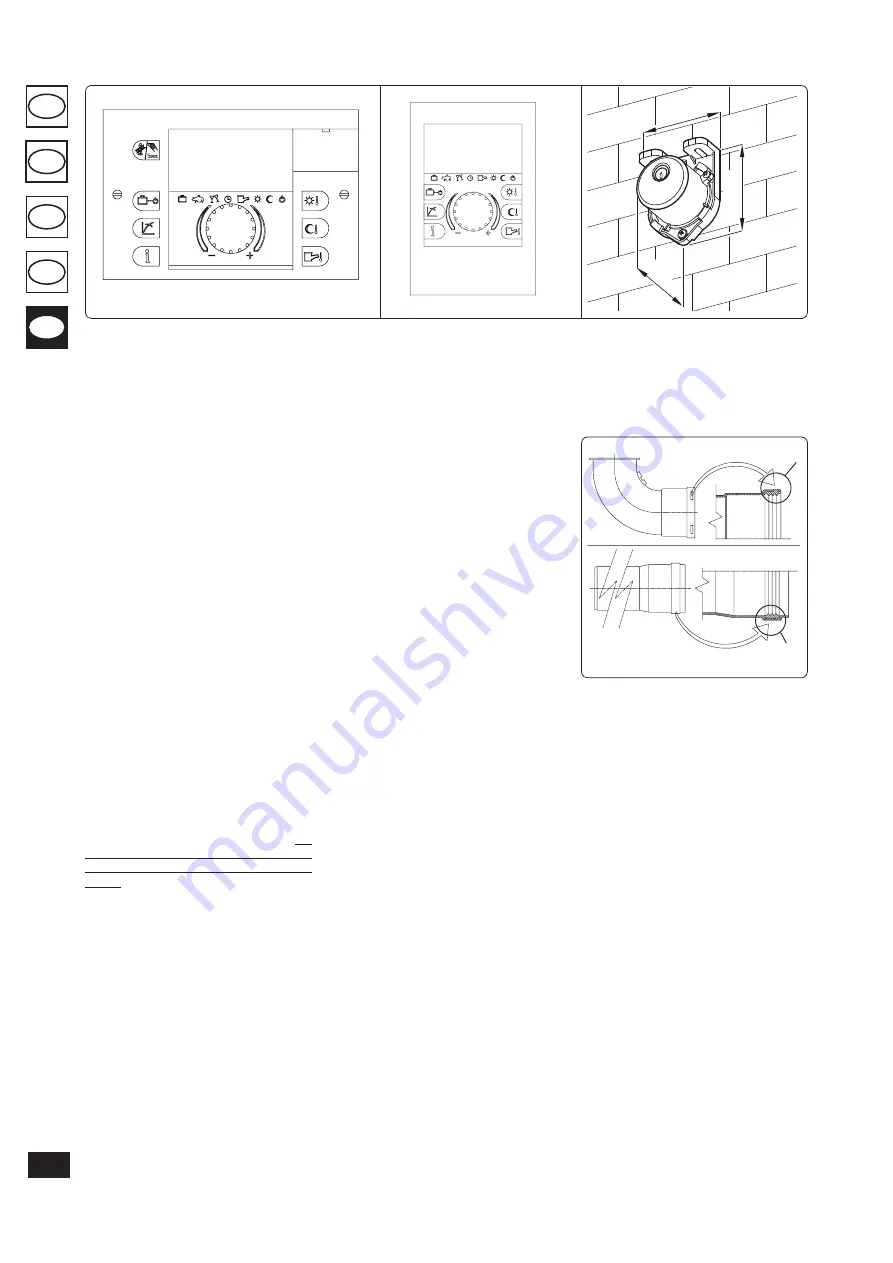
Fig. 1-6
Fig. 1-7
• Zone manager (Fig. 1-7). In addition to the
functions described in the previous point,
the zone manager allows to control all the
important information regarding operation
of the appliance and the heating system with
the opportunity of easily intervening on the
previously set parameters without having to
go to the place where the appliance is installed.
The climate chromothermostat incorporated
into the remote panel enables the system flow
temperature to be adjusted to the actual needs
of the room being heated, in order to obtain
the desired room temperature with extreme
precision and therefore with evident saving
in running costs. It also allows to display the
effective room temperature and the external
temperature (if external probe is present).
The zone manager is powered directly by the
cascade heat adjuster via 2 wires.
• External temperature probe (Fig. 1-8). The
probe can be connected directly to the boiler
electrical system and allows the max. system
flow temperature to be automatically decreased
when the external temperature increases, in
order to adjust the heat supplied to the system
according to the change in external tempera-
ture. The external probe always operates when
connected, regardless of the presence or type
of heat adjuster used and can work in combi-
nation with both heat adjusters. The electric
connection of the external probe must take
place on clamps G and J on the X86 connection
of the boiler. (Fig. 1-4).
Cascade and zone regulator electric connection
or On/off chronothermostat (Optional).
The
operations described below must be performed
after having removed the voltage from the ap-
pliance.
Any thermostat or On/Off environment
chronothermostat must be connected to clamps
“E” and “F” eliminating jumper X40 (Fig. 1-4).
Make sure that the On/Off thermostat contact
is of the “potential free” type, i.e. independent
of the mains supply, otherwise the electronic
adjustment card would be damaged. Any cascade
and zone regulator must be connected using
clamps 37 and 38 to clamps “M” and “O” on
the X86 connection terminal board (in boiler)
respecting the polarity eliminating jumper X40,
(Fig. 1-4)
the connection with incorrect polarity,
even if not damaging the heat adjuster, does not
allow its functioning.
Important:
If the Digital Remote Control is used,
arrange two separate lines in compliance with
current regulations regarding electrical systems.
No boiler pipes must ever be used to earth the
electric system or telephone lines. Ensure eli-
mination of this risk before making the boiler
electrical connections.
Installation with system operating at direct
low temperature.
The boiler can directly feed a
low temperature system, varying the maximum
flow temperature of the boiler and setting a value
between 20 e 85 °C. To vary the maximum flow
temperature of the boiler, modify the maximum
flow temperature of the boiler of parameter N° 4
according to the “parameters mode” procedure.
In this situation it is good practice to insert a
safety device in series with the power supply and
boiler. This device is made up from a thermostat
with a temperature limit of 55 °C. The thermostat
must be positioned on the system flow pipe at a
distance of over 2 metres from the boiler.
1.9 INSTALLATION OF THE AIR
INTAKE AND FLUE ExHAUST
TERMINALS.
Immergas supplies various solutions separately
from the boiler regarding the installation of air
intake terminals and flue extraction; fundamen-
tal for boiler operation.
Important: the boiler must be installed exclusi-
vely with an original Immergas “Green Range”
air intake and fume extraction system in pla-
stic, as envisioned by Standard in force. This
system can be identified by an identification
mark and special distinctive marking bearing
the note: “only for condensing boilers”.
• Resistance factors and equivalent lengths. Each
flue extraction system component is designed
with a Resistance Factor based on preliminary
tests and specified in the table below. The
resistance factor for individual components is
independent from the type of boiler on which
it is installed or the actual dimensions. It is,
however, conditioned by the temperature of the
fluids that pass through the pipe and therefore
varies according to applications for air intake
or flue exhaust. Each individual component has
a resistance corresponding to a certain length
in metres of pipe with the same diameter; the
so-called equivalent length. All of the boilers
have a maximum Resistance Factor, obtained
experimentally, equal to 100. The maximum
Resistance Factor allowed corresponds to the
resistance detected with the maximum allowed
pipe length for each type of Terminal Kit. This
information enables calculations to be made
in order to verify the possibility of various
configurations of flue extraction systems.
Gasket for
“green series” flue extraction ele-
ments. In the case of component lubrication
(already carried out by the manufacturer) is not
sufficient, remove the residual lubricant using a
dry cloth, then to ease fitting spread the elements
with common or industrial talc.
(A)
(B)
Fig. 1-9
45
31
58
Fig. 1-8
118
TR
SI
RU
IE
CZ