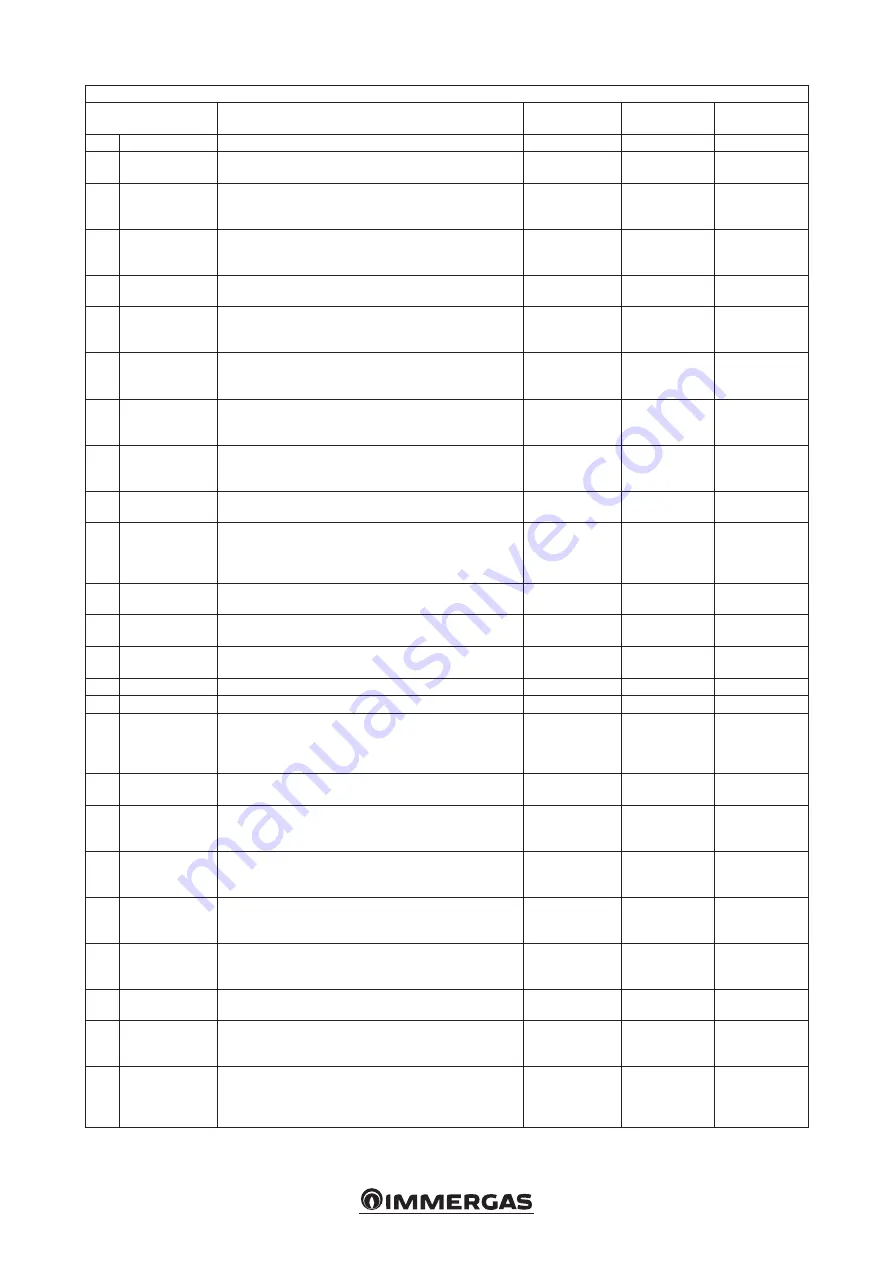
32
Programming menu
Menu item
Description
Adjustment range
Default value
Customised
Value
P01 Set Risc (CH Set)
This defines the boiler's flow temperature during heating
20 ÷ P02 °C
85
P02 Set risc Max (Max
CH Set)
This defines the maximum settable flow temperature during heating
20 ÷ 95 °C
85
P03
Isteresi
riscaldamento
(Heating Hysteresis)
This defines the power-off hysteresis during the heating phase
2 ÷ 10 °C
5
P04
Anti cicli
riscaldamento (Anti-
cycle CH)
This is used to set a waiting time to avoid the boiler from switching on
multiple times and frequently during CH mode
0 ÷ 15 minutes
3 minutes
P05 Tempo min risc (CH
min time)
This is the amount of time that the boiler needs to stabilise, when the burner
runs at minimum power for the set amount of time
3 ÷ 10 minutes
3 minutes
P06
Rampa
riscaldamento (CH
ramp)
The amount of time that the boiler takes to reach the required temperature,
number of degrees per minute (0 means no ramp)
0 ÷ 60 °C/minute
4 °C/minute
P07
Post circolazione
riscaldamento (CH
post-circulation)
The amount of CH post circulation once the CH phase is fnished
1 ÷ 30 minutes
3 minutes
P08
Pot risc max
disponibile (Available
max heat out)
This defines the maximum power percentage to be used during the set CH
phase
P09 ÷ 100%
100%
P09
Pot risc min
disponibile (Available
max heat out)
This defines the minimum power percentage to be used during the set CH
phase
0 ÷ P08%
0%
P10 Minimum system
flow rate
This defines the minimum system flow rate required to power-on the boiler
Attention:
do not change this parameter
5
÷
47 l/minutes
14 l/minutes
P11
Anti umidità elettrodi
(Electrodes anti-
humidity)
This defines fan speed and operating mode, to avoid humidity inside
the condensing module, which could otherwise cause the electrodes to
malfunction (0 = disabled function, recommended value = 40) (RPM speed is
calculated by multiplying the value displayed by 50)
P26
÷
120
0
P12 Boiler’s modulation
ratio
It defines the boiler’s modulation ratio
(Do not modify)
0
÷
100%
10%
P13 Boiler power
Used to calculate the boiler power in the event of simple cascade.
0
÷
255 kW
35 kW = 35
55 kW = 50
P14 External probe curve
This is used to select the external probe operating curve (optional) (0 =
disabled probe)
0
÷
10
0
P15 External probe offset
This defines the CH offset in relation to the selected external probe curve
20
÷
70 °C
30 °C
P16 Set San (DHW set)
This defines the DHW temperature
20 ÷ 65 °C
65 °C
P17 P17 External D.H.W /
3-waypump
- With single boiler and common flow probe, it lets you choose between an
external D.H.W pump and a 3-way one.
- With a simple cascade, it manages a D.H.W. pump (downstream an
hydraulic separator).
0 = 3 Ways
1 = D.H.W. pump
P18 Isteresi sanitario
(DHW hysteresis)
This defines the DHW power-on hysteresis during CH
2 ÷ 10 °C
5 °C
P19
Post circolazione
sanitario (DHW post-
circulation)
This is the post circulation time during DHW once DHW production is
finished
0
÷
180 seconds
60 seconds
P20
Pot san max
disponibile (Available
max DHW pow)
This defines the maximum power percentage to be used during the set DHW
phase
P21
÷
100 %
50 %
P21
Pot san min
disponibile (Available
max DHW pow)
This defines the minimum power percentage to be used during the set DHW
phase
0
÷
P20 %
0 %
P22
DHW flow
temperature with
thermostat
In combination with a storage tank and a separate thermostat, this defines the
flow temperature during DHW operation
35
÷
90 °C
80 °C
P23 Modulazione sanitario
(DHW modulation)
Summed with the “Set San” (P16) parameter, this defines the flow
temperature set that the boiler has to modulate the power on during DHW
5
÷
30 °C
15 °C
P24
Incremento off
sanitario (DHW off
increment)
This defines the time that the boiler allows the burner to switch off during
DHW, by an increment of 5 °C on top of the flow temperature
0
÷
255 seconds
60 seconds
P25
Velocità Max
ventilatore (Min fan
Speed)
This defines the max fan speed and therefore the maximum relative boiler
operating power (RPM speed is calculated by multiplying the value displayed
by 50)
P26
÷
255 RPM x 50
35 kW Met. 101
35 kW LPG 98
55 kW Met. 131
55 kW LPG 129
Summary of Contents for VICTRIX PRO 35 2ErP
Page 1: ...IE Instruction and warning book VICTRIX PRO 35 55 2 ErP 1 041662ENG...
Page 2: ......
Page 38: ...38 3 15 1 6 8 9 9 12 12 10 11 13 13 13 13 A A Rif A 7 7 Ref A...
Page 49: ...49...
Page 50: ...50...
Page 51: ...51...