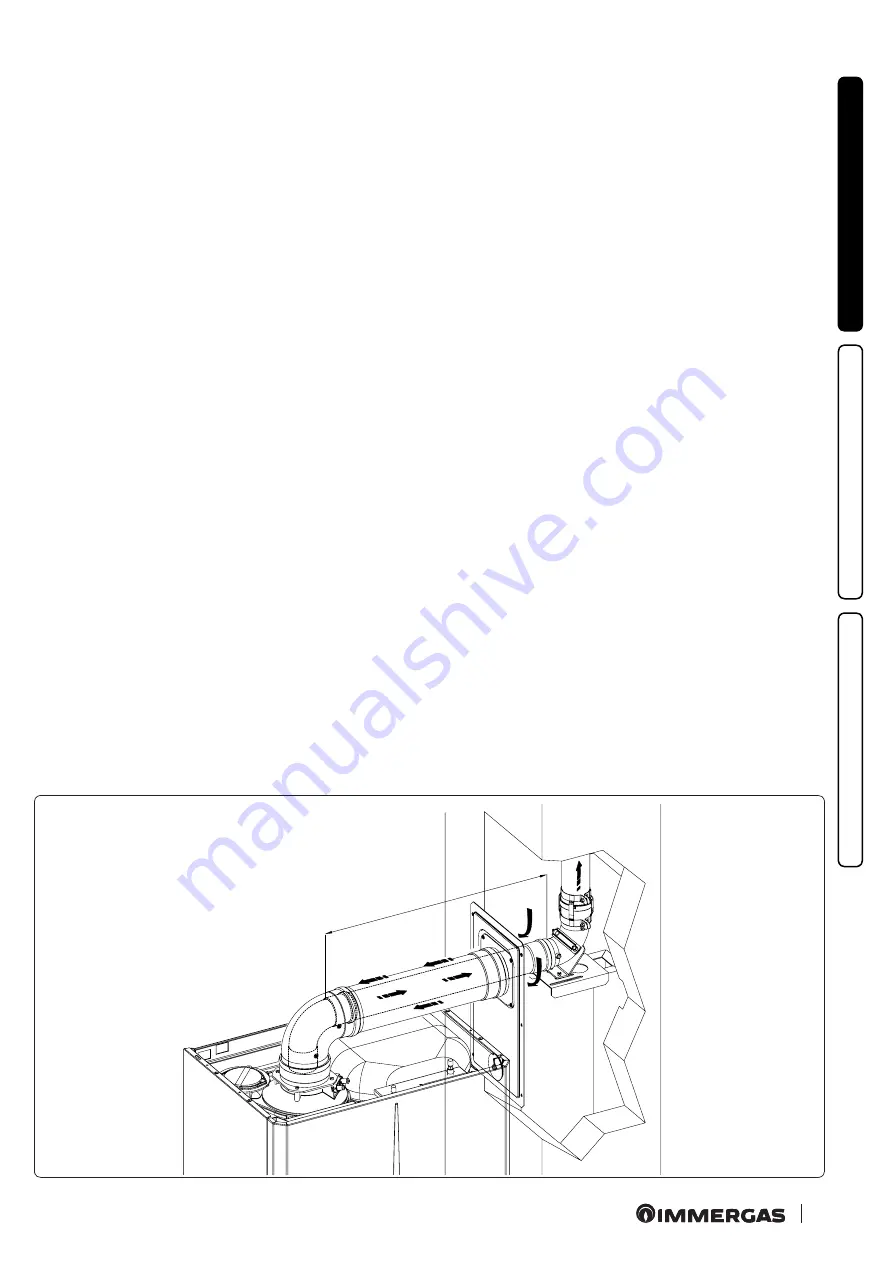
25
C
93
27
X
25
INS
TALLER
US
ER
MAINTEN
AN
CE TECHNI
CI
AN
Technical data.
-
Th
e dimensions of the shafts must ensure a minimum gap be-
tween the outer wall of the smoke duct and the inner wall of the
shaft: 30 mm for circular section shafts and 20 mm in the event
of a square section shaft (Fig. 24).
- Maximum 2 changes of direction are allowed on the vertical
section of the
fl
ue system with a maximum clearance angle of
30° with respect to the vertical.
-
Th
e maximum vertical extension using a
Ø
60 ducting system is
13 m, the maximum extension includes 1 bend
Ø
60/10 at 90°,
1 m of horizontal pipe 60/100, 1 90° ducted bend
Ø
60 and the
roof terminal for ducting.
To determine the C
93
fl
ue system in configurations other than
that described (Fig. 26) one must consider that 1 metre of ducted
pipe according to the indications described has a resistance factor
equal to 4.9.
-
Th
e maximum vertical extension using a
Ø
80 ducting system
is 28 m, the maximum extension includes 1 adapter 60/100 to
80/125, 1 87° bend
Ø
80/125, 1 m of horizontal pipe 80/125, 1
90° ducted bend
Ø
80 and the roof terminal for ducting.
To determine the C
93
fl
ue system in configurations other than
that described (Fig. 26) one must consider the following head
losses:
- 1 m of concentric pipe
Ø
80/125
=
1 m of ducted pipe;
- 1 87° bend
=
1.4 m of ducted pipe;
Consequently one must subtract the equivalent length of the
part added to the 28 m available.