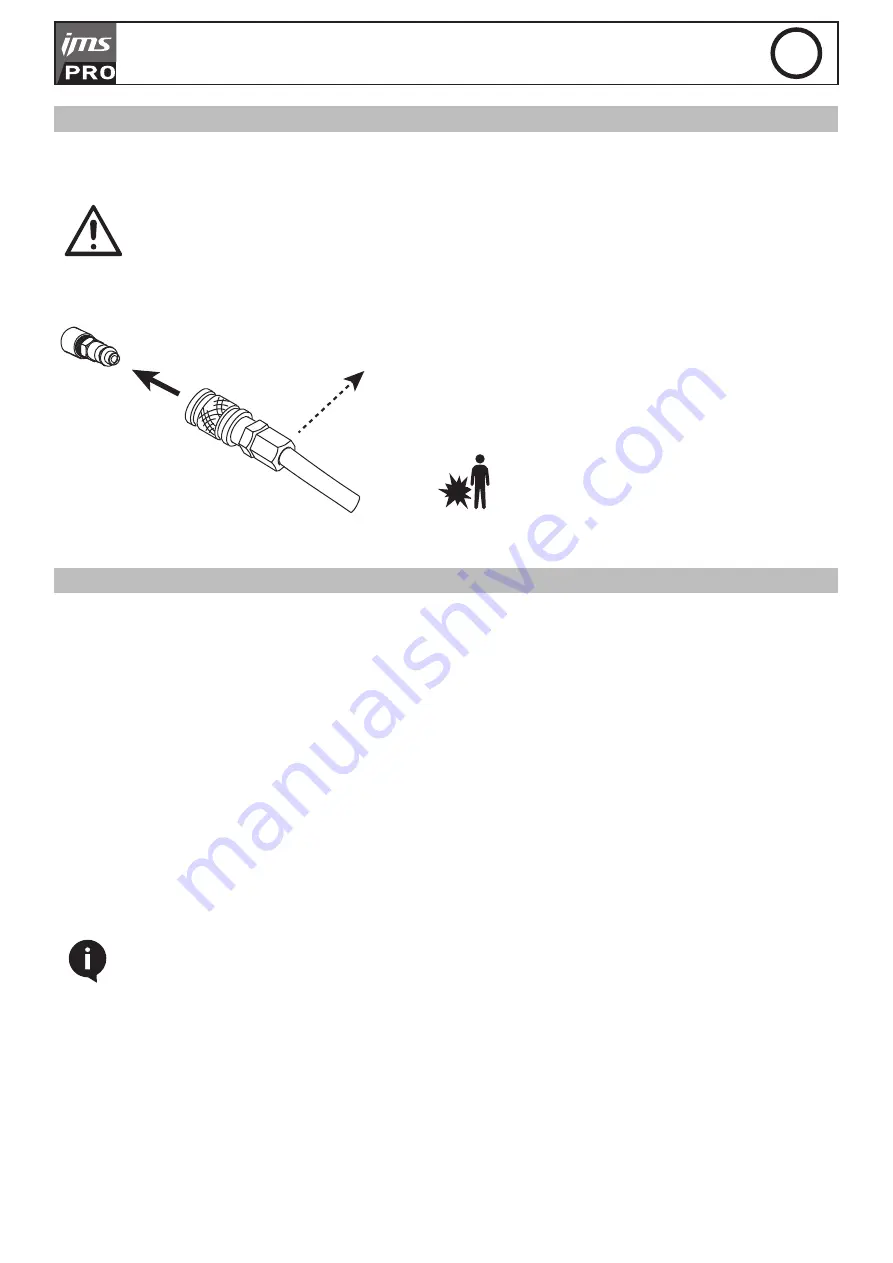
23
PLASMA CUTTER 85A / 125A
EN
AIR SUPPLY
The air supply can come from a compressor or high pressure bottles. A high pressure manometer must be used on any type of air supply and must be
able to transport the gas to the plasma cutter. These machines come with an integrated air filter (5μm), but an extra filtering system can be necessary
depending on the quality of the air supply (impurities filter in option, ref. 039728).
If the supplied air is of low quality, the cutting speed is reduced, the cutting quality deteriorates, the maximum cutting capacity
diminishes and the life cycle of the consumables is reduced.
For optimal performance, the compressed air must comply with the standard ISO8573-1, class 1.2.2. The maximum vapor pressure point must be - 40
°C. The maximum oil quantity (aerosol, liquid et vapor) must be 0.1 mg/m3.
Connecting the gas supply to the current source by means of an inert gas
pipe of an internal diameter of 9.5 mm and a quick connect coupler.
The pressure must not exceed 9 bars,
The filter’s cuve could explose.
The recommended entry pressure during air circulation is 5 to 9 bars with a minimum of 305 L/min.
MANUAL TORCH SETUP
The torches are cooled with ambient air and do not require any special cooling.
1 - CONSUMABLES LIFE CYCLE
The replacement frequency of the Plasma Cutter 85A TRI et 125A TRI’s consumables depends on several factors:
• The metal thickness.
• The average cutting time
• The cutting mode (manual or automatic).
• The air quality (presence of oil, humidity or other contaminants).
• The metal piercing or the cut from the edge.
• The adequate distance between the torch and the part when cutting or gouging.
• The adequate piercing height.
• The chain link cutting.
In normal conditions :
- During manual cutting, the electrode wears out first.
- During automatic cutting, the shroud wears out first.
2 - CHOICE OF CONSOMMABLES
The manual torch uses «protected» consumables. It is thus possible to drag the tip of the troch on the metal.
To maximise the cutting performance, it is important to use the correct consumables depending on the plasma cutter settings.
• A current that is too low leads to low cutting performance.
• A current that is too high for the tailpipe leads to early deterioration.