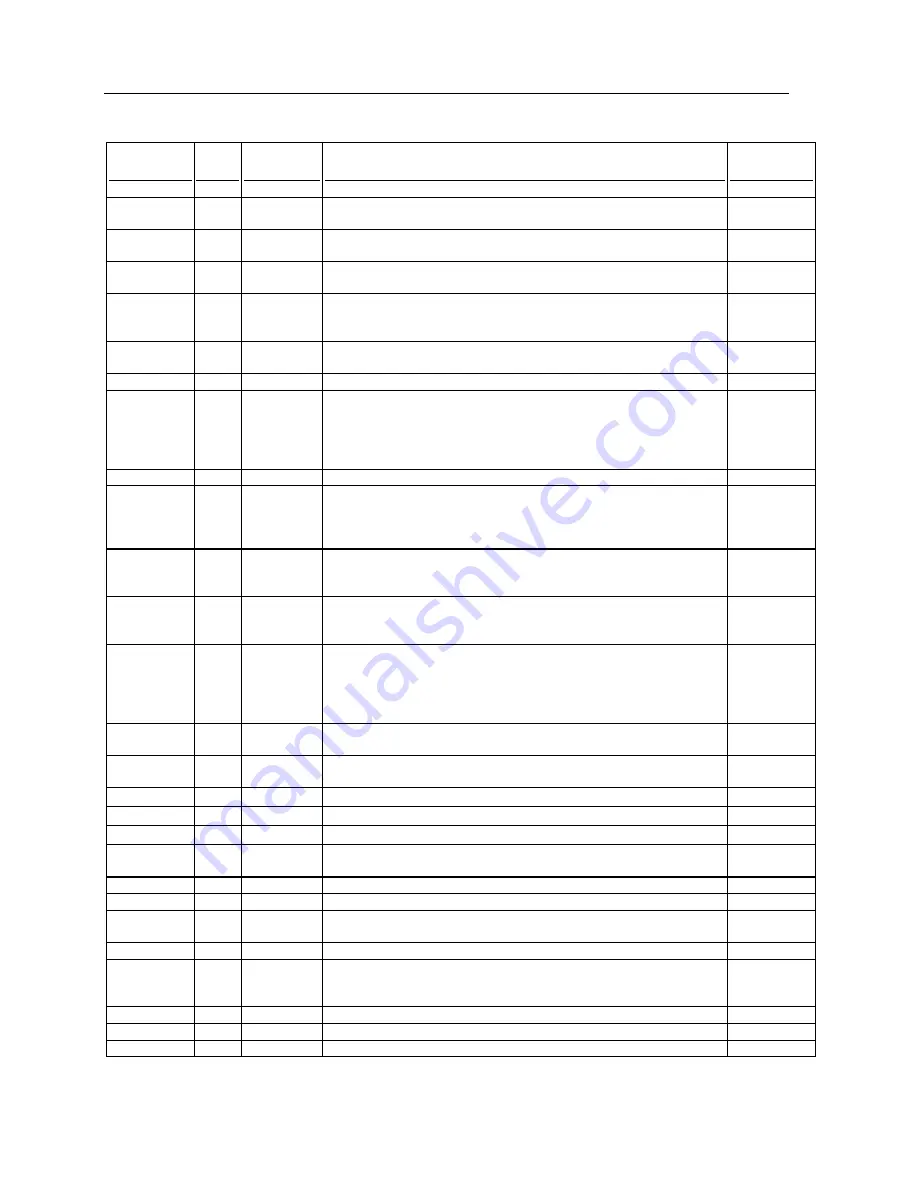
Chapter 8 General Reference
71
FREQUENCY ITEM KEY
INSPECTION DESCRIPTION
STATUS
(S,R,X,NA)
D
7
Wire Rope
Inspect for apparent deficiencies per applicable requirements and
manufacturer’s specifications.
D
8
Pins
Proper engagement of all connecting pins and pin retaining
devices.
D
9
General
Overall observation of crane for damaged or missing parts,
cracked welds, and presence of safety covers.
D
10
Operation
During operation, observe crane for abnormal performance,
unusual wear (loose pins, wire rope damage, etc.). If observed,
discontinue use and determine cause and severity of hazard.
D
11
Remote
Ctrl
Operate remote control devices to check for proper operation.
D
12
Electrical
Operate all lights, alarms, etc. to check for proper operation.
D
13
Anti Two-
Block or
Two-Block
Damage
Prevention
Operate anti two-block or two-block damage prevention device to
check for proper operation.
D
14
Tires
Check tires (when in use) for proper inflation and condition.
D
15
Ground
Conditions
Check ground conditions around the equipment for proper
support, watching for ground settling under and around stabilizers
and supporting foundations, ground water accumulation, or similar
conditions.
D
16
Level
Check the equipment for level position within the tolerances
specified by the equipment manufacturer’s recommendations,
both before each shift and after each move and setup.
D
17
Operator
cab
windows
Check windows for cracks, breaks, or other deficiencies which
would hamper the operator's view.
D
18
Rails, rail
stops, rail
clamps and
supporting
surfaces
Check rails, rail stops, rail clamps and supporting surfaces when
the equipment has rail traveling.
D
19
Safety
devices
Check safety devices and operational aids for proper operation.
D
20
Electrical
Check electrical apparatus for malfunctioning, signs of apparent
excessive deterioration, dirt or moisture accumulation.
D
21
Other
D
22
Other
M
23
Daily
All daily inspection items.
M
24
Cylinders
Visual inspection of cylinders for leakage at rod, fittings, and
welds. Damage to rod and case.
M
25
Valves
Holding valves for proper operation.
M
26
Valves
Control valves for leaks at fittings and between stations.
M
27
Valves
Control valve linkages for wear, smoothness of operation, and
tightness of fasteners. Relief valve for proper pressure settings.
M
28
General
Bent, broken, or significantly rusted/corroded parts.
M
29
Electrical
Electrical apparatus for malfunctioning, signs of apparent
excessive deterioration, dirt or moisture accumulation. Electrical
systems for presence of dirt, moisture, and frayed wires.
M
30
Structure
All structural members for damage.
M
31
Welds
All welds for breaks and cracks.
M
32
Pins
All pins for proper installation and condition.
Summary of Contents for 2003i
Page 2: ......
Page 6: ......
Page 38: ......
Page 77: ...Chapter 8 General Reference 75 X R CA ITEM EXPLANATION DATE CORRECTED ...