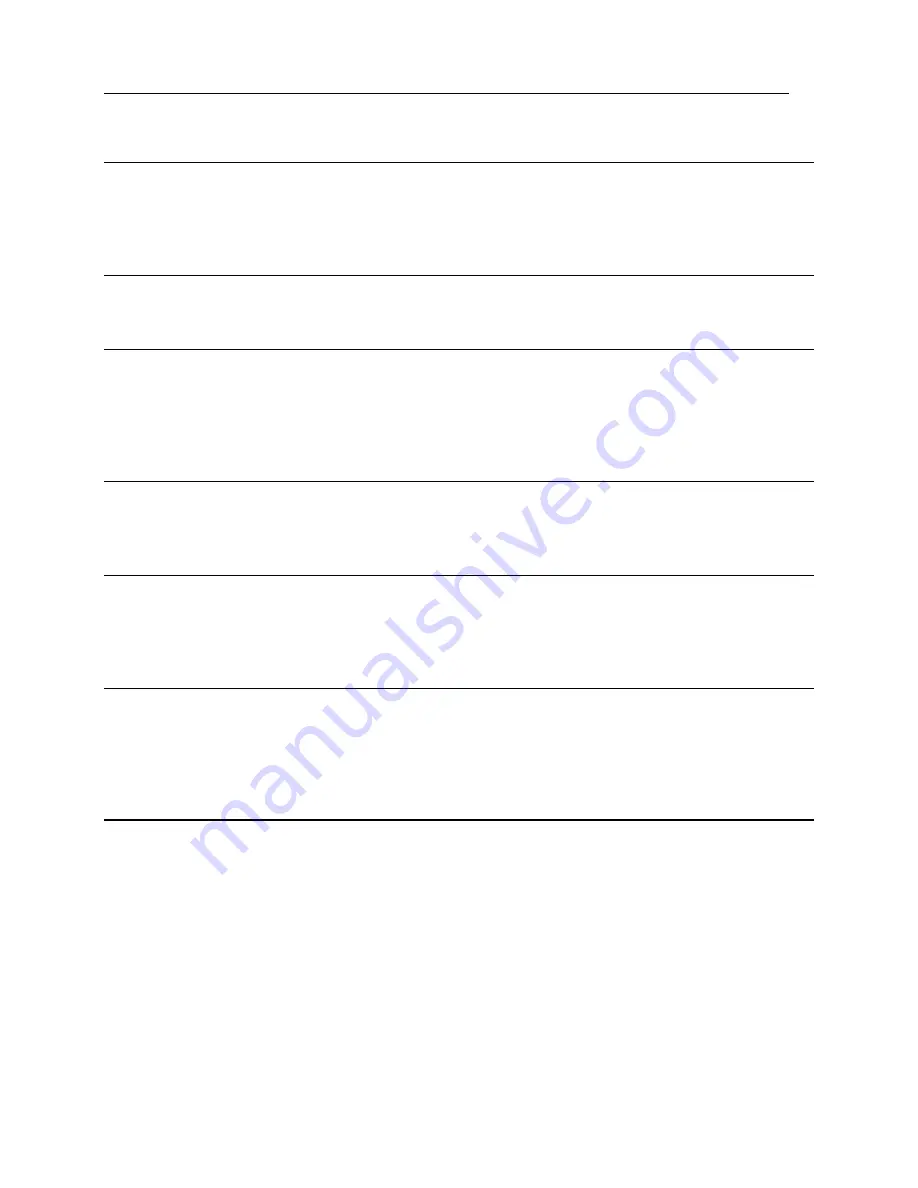
Operation 35
MINIMUM PRESSURE VALVE
The minimum pressure valve is located at the outlet of the coalescer head and serves to
maintain a minimum discharge pressure of 65 PSIG in operation, which is required to assure
adequate compressor lubrication pressure.
OIL FILTER
The compressor oil filter is the full-flow replaceable element type.
COMPRESSOR COOLING SYSTEM
The compressor cooling system consists of a remote mounted oil/air cooler with an electric fan.
The fan is activated through a temperature switch (180°) and latching relay, so it will not turn off
until the compressor is disengaged and the system pressure is fully relieved, or when the engine
is turned off. The thermal valve will divert oil to the oil cooler at 160°F.
ELECTRICAL AND SAFETY CIRCUIT SYSTEM
The unit is supplied with an hourmeter, wire harness and a high temperature shutdown switch.
Compressor shutdown occurs in the event of high compressor temperature (> 250°).
AUTOMATIC BLOW DOWN VALVE
There is one blow down valve in the compressor system. It is located inside the compressor.
The valve will automatically bleed the sump to atmospheric pressure when the compressor is
disengaged. The blow down time interval is typically less than 90 seconds.
CONTROL SYSTEM
The prime component of the compressor control system is the compressor inlet valve. The
control system is designed to match air supply to air demand and to prevent excessive
discharge pressure when compressor is at idle. Control of air delivery is accomplished by the
inlet valve regulation and modulation as directed by the discharge pressure regulator.
PRESSURE REGULATOR VALVE
This valve, located inside the compressor, is used to set the desired discharge pressure within
the operating pressure range. Turning the regulator screw clockwise increases the working
pressure; a counterclockwise movement of the screw reduces the working pressure. This
system has a maximum operating pressure of 150 psi.