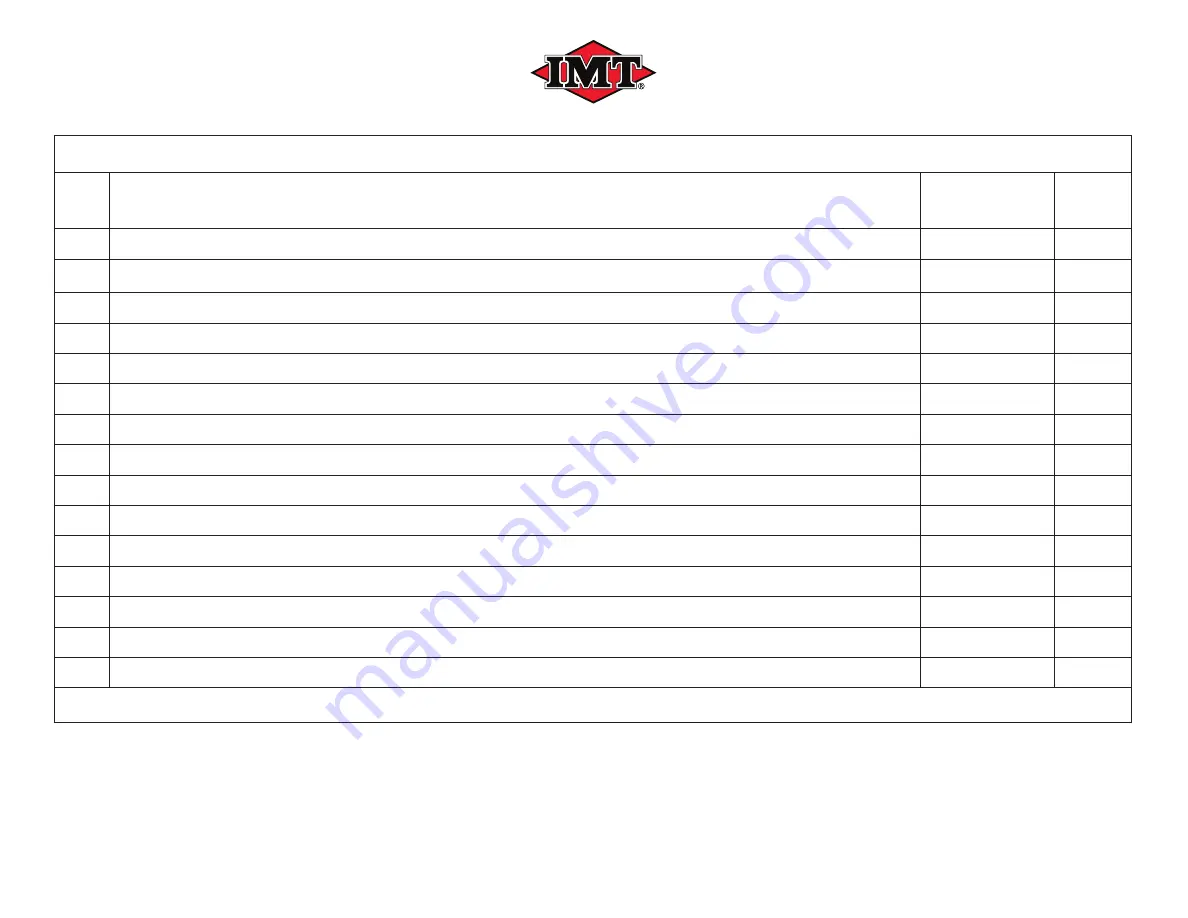
SECTION 7: ILLUSTRATED PARTS LIST
99906549 rev 00 (JANUARY-2020)
7 - 5
CAS40PL, CAS40PL-CW, CAS40PLE, CAS40PLE-CW
IOWA MOLD TOOLING CO., INC.
(641) 923-3711
7.2 COMPRESSOR AND PARTS
ITEM
DESCRIPTION
PART
NUMBER
QTY
1
PLUG, MALE 37 JIC 08
1
2
ORIFICE, .63 HEX x 1/8F x 1/4M x 0.031
1
3
TEE, 1/4” NPT MALE BRANCH
1
4
ORIFICE, FILTER .032 DIA., 1/4 FPT X 1/4 MPT
1
5
WASHER, LOCK 1/2 GRADE 8
4
6
VALVE, CHECK MANIFOLD 60CFM 450F
1
7
COMPRESSOR, PARTS DD AL
1
8
EYE, LIFTING COMPRESSOR
1
9
HOSE, COMPRESSOR OIL DRAIN DD
1
10
BUSHING, RED STEEL 1 1/4 x 1
1
11
PLUG, PIPE 1/4
1
12
CAPSCREW, HEX 10mm 1.5 x 30
1
13
CAPSCREW, HEX GR5 1/2-13 x 1.75
4
14
CONNECTOR, 37FL/MPT #04 x 1/8
1
15
CONNECTOR, 37FL/MPT #08 x 3/8
1
PLEASE NOTE: WHEN ORDERING PARTS, INDICATE MACHINE SERIAL NUMBER.
Summary of Contents for CAS40PL
Page 2: ...BLANK PAGE...
Page 81: ...BLANK PAGE...