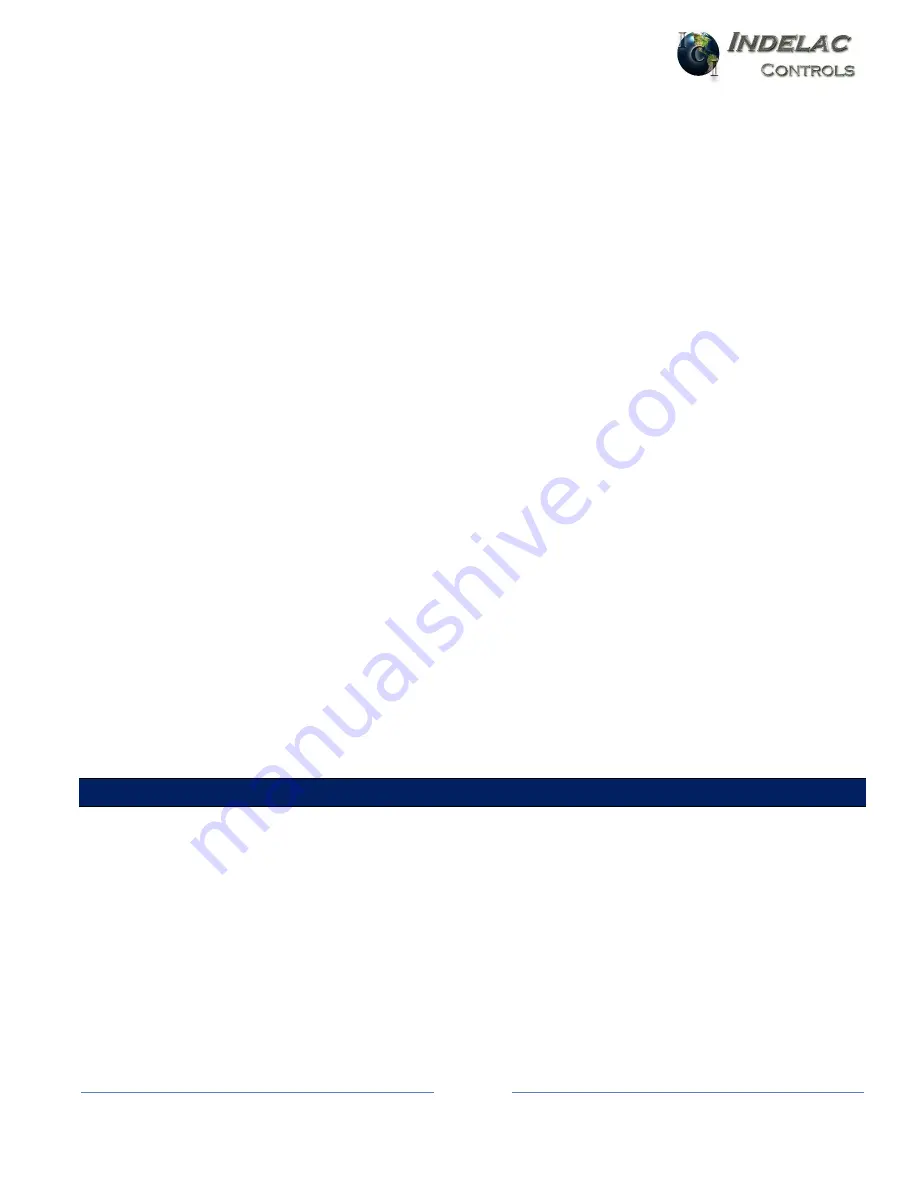
PART #22018-DH - High-Resolution Positioner
Page 13
30V or less. Note, earlier versions of the DHC-400 may not have this feature. Contact Indelac, Inc.
for more information.
WARNING! Exposing the DHC-400 to frequent or continuous voltages above 30V can damage the
unit. The user should take steps to suppress or eliminate possible supply voltage conditions above
30V.
Motor 1 No Motion
- A no motion fault is detected when no actuator motion is detected while the
Motor 1 output is turned on and drawing less than 0.5A of motor current. The fault can be cleared
in the same manner as previously described for a Motor 1 Stall. A stall usually indicates a heavy
mechanical load or stall, while a no motion fault usually indicates a broken motor wire or disengaged
feedback pot. Note that a stall cannot be detected in applications using very small motors (locked
rotor currents less than 0.5A); only a no motion fault can be detected.
Motor 2 No Motion
- A no motion fault is detected when no actuator motion is detected while the
Motor 2 output is turned on and drawing less than 0.5A of motor current. The fault can be cleared
in the same manner as previously described for a Motor 1 Stall. A no motion fault differs from a stall
as previously describe for a Motor 1 No Motion fault.
Double No Motion
- If the DHC-400 detects a no motion fault in both directions, both motor outputs
will be disabled. The fault can be cleared in the same manner as previously described for a Double
Stall.
Feedback Alarm
- A fault condition is detected whenever the feedback signal is out of range (that
is, less than 5% of the potentiometer value or more than 95% of the potentiometer value), or when
any of the potentiometer connections are broken. Normal operation resumes when the
potentiometer is reconnected or back in range.
Loss of Command
- If the command signal is disconnected, the fault indication will remain on until
the signal is reconnected. See LOSS OF COMMAND for details.
Command Out of Range
- If the command signal goes out of range, the fault indication will remain
on until the signal is back in range. See LOSS OF COMMAND for details.
LIMIT SWITCHES:
The actuator's limit switches should be connected to J1 as described in ACTUATOR (J1) - also see
OUTLINE and BLOCK DIAGRAM. The limit switches must be closed throughout the operating range
from closed to open. When Limit Switch 1 opens, Motor 1 operations are disabled. Likewise, when
Limit Switch 2 opens, Motor 2 operations are disabled.
Note that the actuator's limit switches should be set outside of the operating range set by the CLOSE
and OPEN functions. Limit switches exhibit wide variations, and the DHC-400 can position the
actuator more precisely at closed and open than the limit switches. A limit switch better serves as a
fail-safe device.
After setting the open and closed positions, the DHC-400 automatically determines which limit
switch is associated with open and closed. When a limit switch is reached, the appropriate indicator
Summary of Contents for 22018-DH
Page 1: ......
Page 3: ...PART 22018 DH High Resolution Positioner Page 3 BOARD OUTLINE...
Page 17: ...PART 22018 DH High Resolution Positioner Page 17 WIRING DIAGRAMS Output Configurations...
Page 18: ...PART 22018 DH High Resolution Positioner Page 18 WIRING DIAGRAMS Input Configurations...
Page 19: ...PART 22018 DH High Resolution Positioner Page 19 WIRING DIAGRAMS Special Applications...
Page 20: ...PART 22018 DH High Resolution Positioner Page 20 WIRING DIAGRAMS Special Applications...