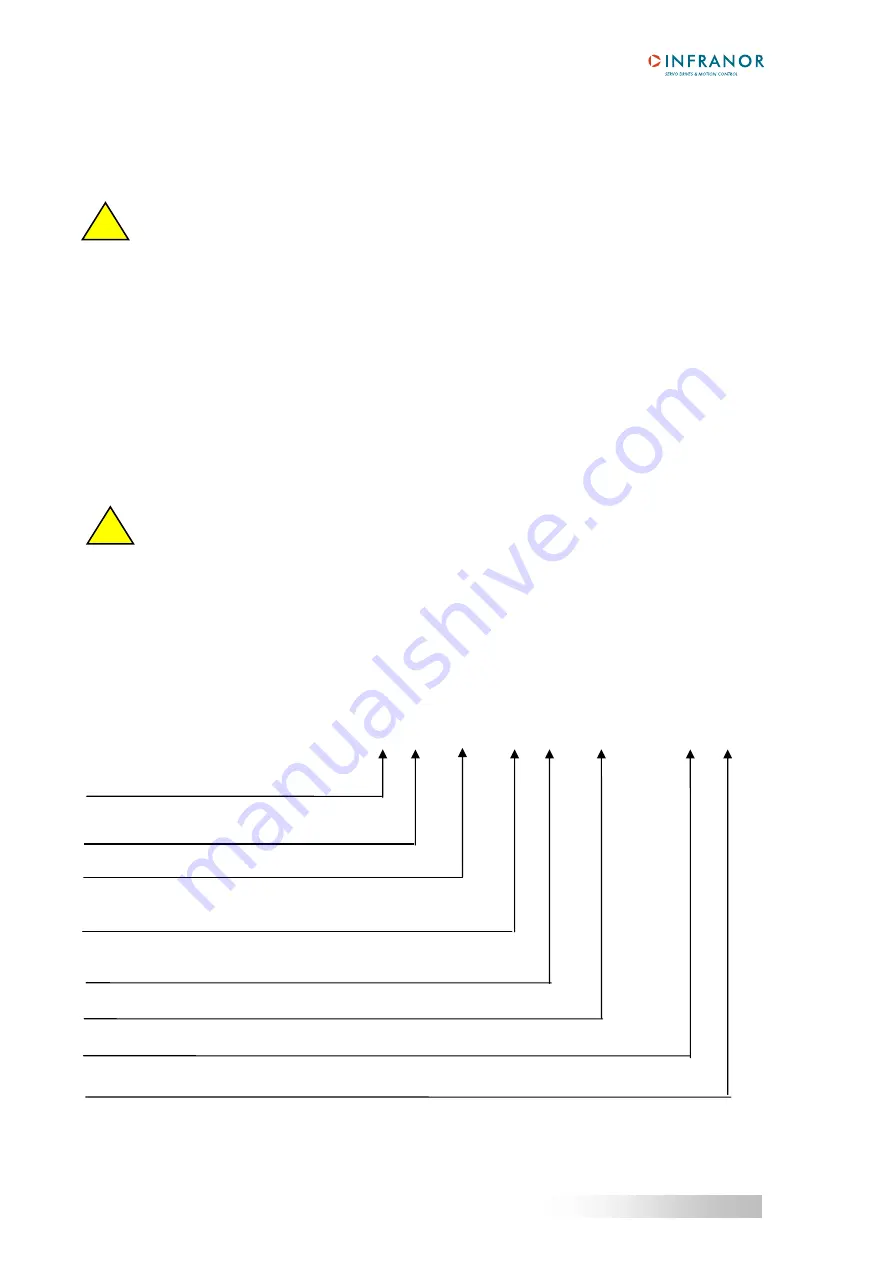
54
SMT-BD2
Chapter 8 – Appendix
Select the
PI
2
controller and the
High Bandwidth
, then execute the
Auto-tuning
procedure.
Execute the
Linear cogging acquisition
procedure. This procedure is taking a few minutes because the motor is
moving at low speed from one travel limit switch to the other in both directions. The acquired cogging force value
is automatically stored in the amplifier CT/BD2 memory during the procedure execution.
!
The motor must not be disturbed during the cogging force acquisition procedure.
For checking the cogging force compensation effects on the motor shaft, proceed as described below :
Switch the amplifier in force control mode by activating the CI input (X4 connector, pin 4) and short-circuit or open
the analog command input CV (X4 connector, pins 15, 16 and 17).
Execute the
Offset compensation
procedure.
Check manually for the reduction of the cogging force effects, by moving the motor when the
Cogging
compensation
command is activated and the amplifier enabled. If some resistant points do remain over one
complete motor travel, renew the acquisition procedure.
Switch off the amplifier. Then switch on the amplifier again, enable the
Cogging compensation
command and
execute the
Save parameters to EEPROM
procedure.
!
At the amplifier power up the cogging force compensation is only effective after the detection of the
encoder marker pulse.
When changing either the motor, the encoder or the amplifier, the cogging force acquisition
procedure must be renewed.
6 - AMPLIFIER TYPES
SMT-BD2 / _ _ - _ / _ _ / _ - T - _ _
Amplifier voltage rating: 220 VAC or 400 VAC
Serial link :
1 = RS 232 / 2 = RS 422
Analog input :
a = 12 bit / b = 16 bit
r = Additional heatsink for 220 VAC amplifiers
(total width = 18 TE)
w = Braking resistor for 220 VAC amplifiers (single-axis rack)
BS = Synchronous motor
Amplifier current rating:
4 A to 100 A (220 VAC) or 15 A to 60 A (400 VAC)
CT = Cogging torque compensation