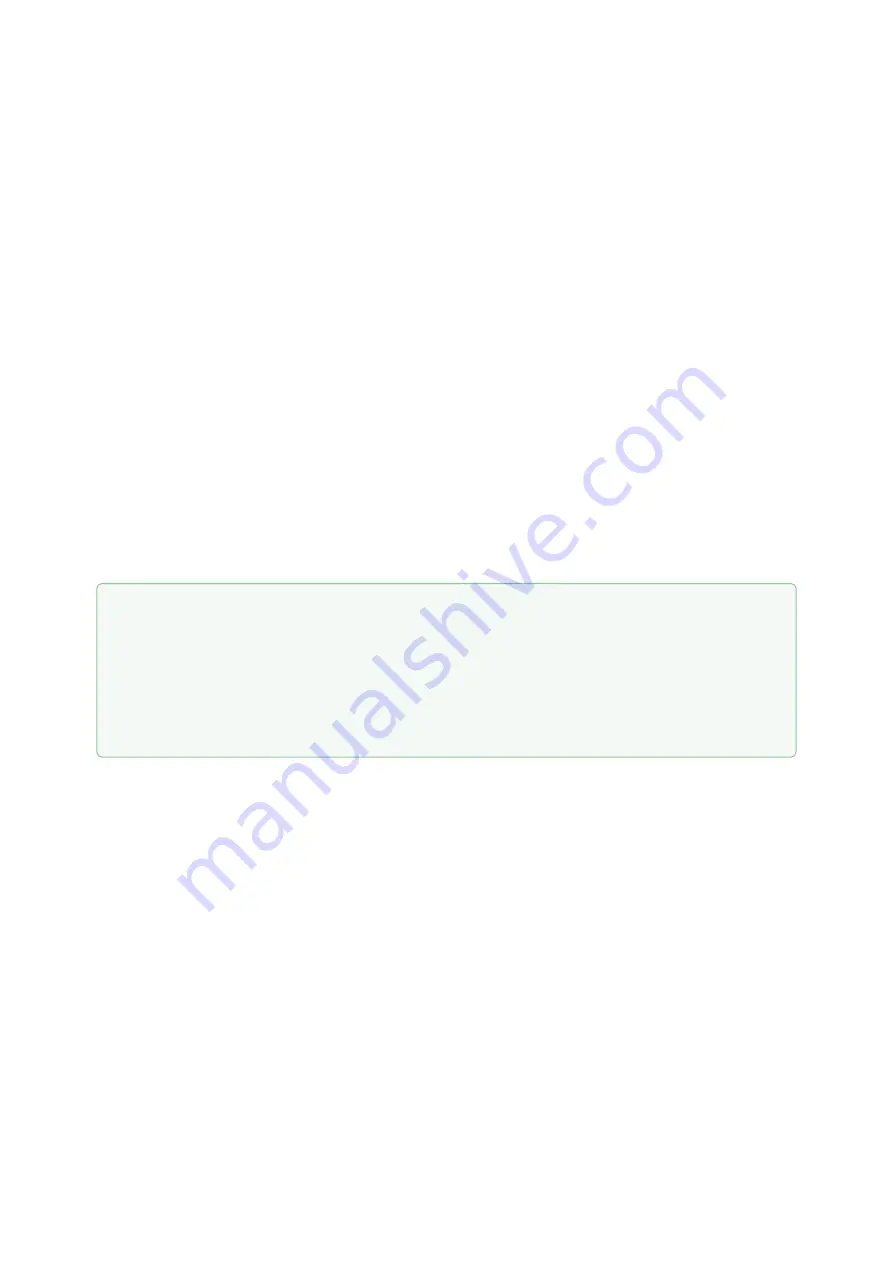
Triton Go Product Manual |
Wiring and Connections
INGENIA | 05/29/2017
52
7 Wiring and Connections
Proper wiring, and
especially grounding and shielding
, are essential for ensuring safe, immune and optimal
servo performance of Triton Go Servo Drive. Next pages show detailed connection recommendation as well as
technical details of each interface.
•
•
•
Motor and shunt braking resistor
•
•
•
•
•
7.1 Protective earth
Connection of Triton Go Servo Drive and motor housing to Protective Earth (PE)
is required for
safety
reasons.
Electrical faults can electrically charge the housing of the motor or cabinet, increasing the risk of
electrical shocks. A proper connection to PE derives the charge to Earth, activating the installation safety
systems (differential protections) and protecting the users.
Moreover, a proper connection to PE prevents many of the noise problems that occur operating a servo drive.
Triton Go Servo Drive provides the following earth/ground connection points, which are internally connected
and decoupled to power ground and power supply:
•
PE terminal in the Supply, shunt and motor connector.
•
PE terminal in the Halls, motor temperature and analog feedback connector.
•
PE terminal in the Absolute encoder connector.
•
PE terminal in the Incremental and Sin-Cos encoder connector.
•
PE terminal in the I/O and LEDs connector.
•
PE terminal in the RS485 connector.
•
Cold plate is connected to PE.
A diagram of the recommended Earth wiring is shown below.
Reducing EMI susceptibility
Connecting the drive PE terminals
and cold plate screws
to your system Earth and to the motor
housing solves many noise and EMI problems.
The PE drive terminals are decoupled to power
ground through a safety capacitor. This provides a low impedance
preferential path for coupled
common mode noises that otherwise would be coupled to sensitive electronics like the
encoders. A good
grounding of the drive to the earth of the power supply
is also essential for a EMI
reduction.