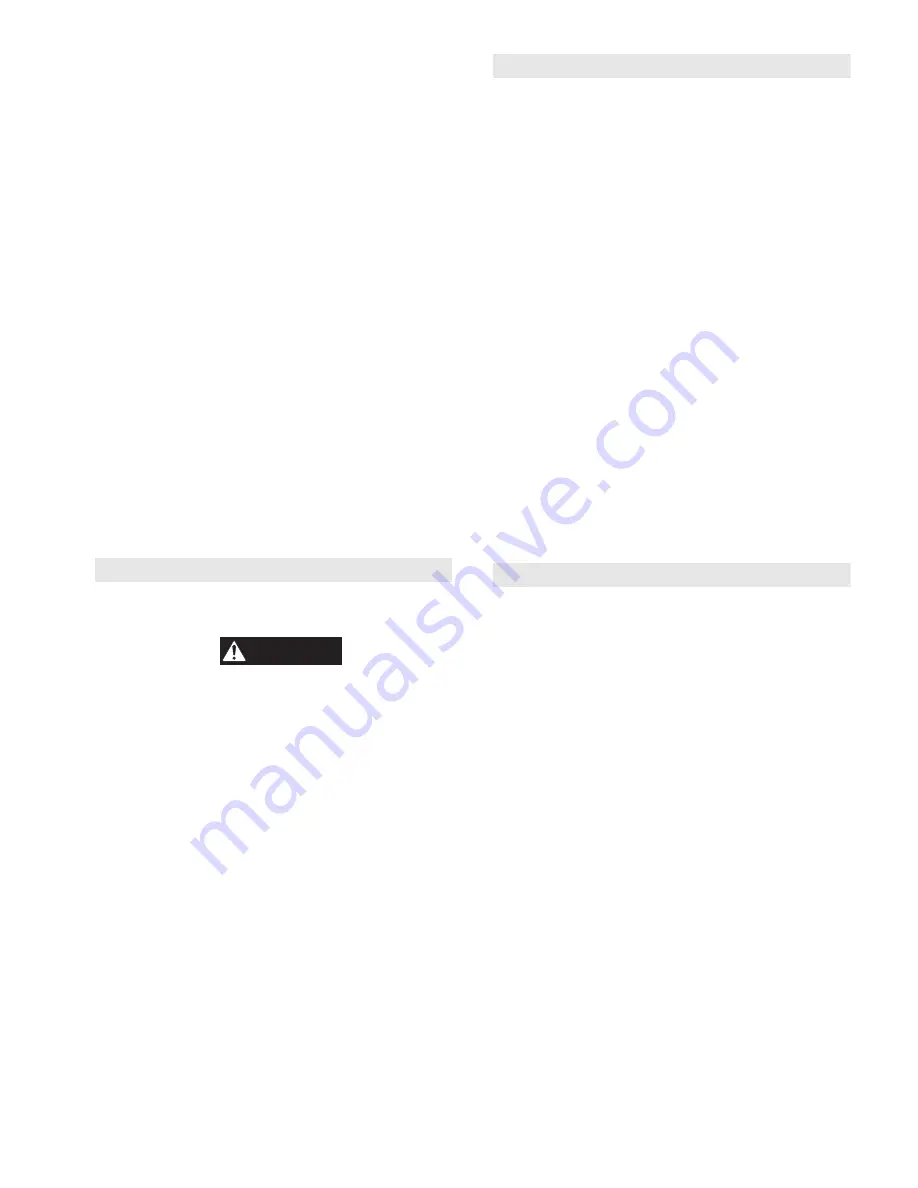
MHD56114 - Edition 4
35
3.
Assemble roller (116) in plunger (114) and secure using
dowel pin (115). Heavily coat the plunger assembly with
“LubriPlate” MO-LITH No. 2 or equivalent lubricant. Install
spring (113) and plunger assembly in brake bracket (106).
Align groove in plunger towards hole in motor end (68)
upright.
4.
Align cylinder rod roller surface to groove in plunger. Turn
cylinder (121) clockwise until snug. Adjust cylinder (121)
such that the air hose connection port is horizontal and
towards the motor.
Conduct the following when the winch is assembled, but prior
to mounting to the foundation. The motor end of the winch
should be raised enough to allow access to the brake
components located on the inside surface of the inboard
(motor end) upright (68).
5.
Place spacer (105) between upper brake band flange and
bracket. Attach band assembly (104) to bracket (106) using
three capscrews (101), spacers (102) and spacer tubes (103).
Torque capscrews to 55 ft lbs (75 Nm).
6.
Install pivot bar (119) and capscrew (120) through lower
flange of brake band assembly (104). At lowest point of
threads, place a bead of Loctite
®
680 and install jam nut
(117) fully. Jam nut threads must become coated with
sealant. Install second jam nut (117) to approximately the
middle of the thread length. Thread capscrew (120) into
bottom of plunger (114) a minimum of five thread lengths.
Lock in place, against plunger, using jam nut (117). Adjust
brake as described in the ‘Drum Band Brake Adjustment’
section.
Adjusting Automatic Drum Band Brake
Optional Feature. Refer to Dwg. MHP2508 on page 46.
CAUTION
• This adjustment is done after a rebuild. It is only a rough
adjustment intended to remove major slack prior to adjusting
with a load.
This procedure can be done at a work bench using a 50 psig (3.4
bar/340 kPa) air supply applied to the brake cylinder. After
completion of this procedure the brake must further be adjusted
using the recommended air supply and a test load.
1.
Insert a length of 3/8 inch NC threaded rod, fully into the
cylinder rod (108). With the brake band slack and no air
supplied to the brake, push the end of the threaded rod to
position the plunger all the way inside the brake bracket
(106). Place a nut on the threaded rod, and locate nut until it
is just touching the cover (125). Apply air to the brake. The
threaded rod should move out from the cylinder
approximately 1 inch (25 mm).
2.
Tighten capscrew (120) in plunger (114) to remove slack
from band brake. Release air pressure. The nut should move
closer to the end cover (125) and stop.
3.
Repeat step 1 until the nut stops at approximately 9/16 inch
(14 mm) from the cover (125).
4.
Refer to further adjusting in ‘Automatic Drum Brake
Adjustment’.
Freespool Assembly
Refer to Dwg. MHP2414 on page 63.
1.
Assemble shaft support (503) to output shaft (28) and secure
with socket capscrews (504). Torque capscrews to 18 ft lb
(25 Nm).
2.
Apply Loctite
®
609 to handle (512) and press into free spool
shifter (515).
3.
Apply Loctite
®
242 to threads of plunger (511) and screw
into detent plate (514).
4.
Place new ‘O’ ring (501) into groove in housing (502).
Lubricate with a mixture of half ISO VG 68 (SAE 20W)
lubricant and half molybdenum disulfide lubricant
compound.
5.
Lubricate free spool shifter assembly (507) with above
compound, place into housing (502).
6.
Slide shaft support (503) and output shaft (28) as an assembly
into housing (502) until groove in shaft support aligns with
pin (516) in free spool shifter assembly (507). Tap into place
with suitable soft headed hammer.
7.
Insert this assembly into winch drum (62), twisting slightly to
align gears and until housing (502) fits tightly against
outboard upright (26). Align marks made in ‘Disassembly’
step 2.
8.
Install capscrews (505) into housing (502) tighten and torque
to 18 ft lb (25 Nm).
9.
Apply light coat of EP grease to face of housing (502), place
gasket (18) on housing face and align bolt holes.
10. Using capscrews (1) and washers (902) install cover (2) onto
housing (502).
11. Operate free spool several times to ensure smooth operation.
Drum Guard Assembly (optional feature)
Refer to Dwg. MHP2512 on page 62.
Without Drum Brake, or with Automatic Drum Brake:
1.
Place drum guard (590) on rear side rail (64) with the longer
inside tab located under the side rail edge and the smaller
outside tabs located on top of the side rail edge.
2.
Place washers (593) on brackets (591). Install washers in
quantities required to remove any ‘play’ or gap between
drum guard and brackets.
3.
Align brackets (591) on mounting holes in uprights (26) and
(68). Secure in place with capscrews (592).
With Lever Operated Manual Drum Brake:
1.
Center drum guard (590) on rear side rail (64) with the longer
inside tab located under the side rail edge and the smaller
outside tabs located on top of the side rail edge.
2.
Place extension (596) into bracket (595) and secure with
capscrew (594).
3.
Place washers (593) on bracket (591) and extension (596).
Install washers in quantity required to remove any ‘play’ or
gap between drum guard and brackets.
4.
Align brackets (591) and (595) to mounting holes in uprights
(26) and (68). Secure using capscrews (592).