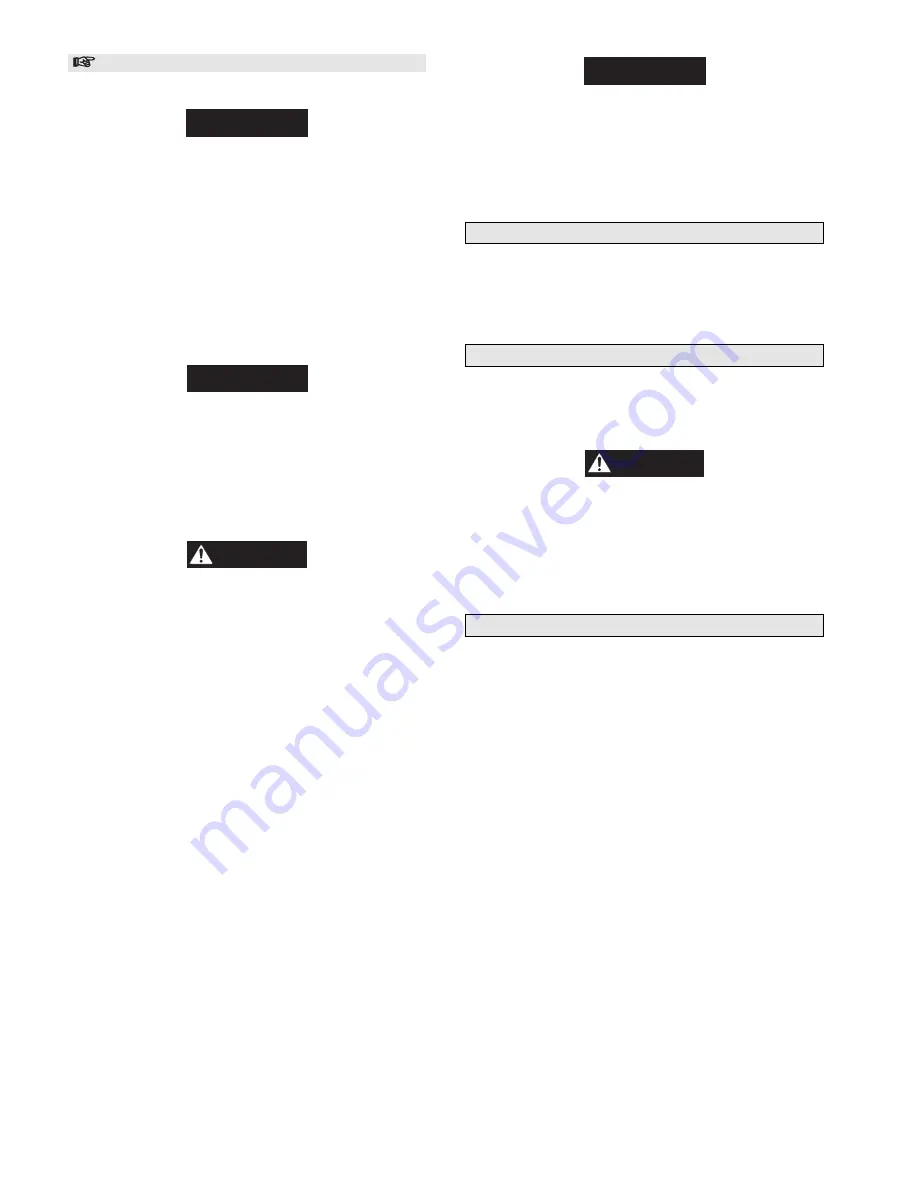
20
Reduction Gear and Disc Brake Fill/Drain Procedures
Refer to Dwg. MHP0501.
NOTICE
• There are only 2 plugged holes, located 90º apart, on
reduction gear cover (33). To fill or drain reduction gear oil,
the winch drum must be rotated to align the plugs for either
the fill or drain operation.
To Fill:
1.
Rotate the winch drum to align the reduction gear plugs to
the fill position. Fill plug position is at top center.
2.
Remove the fill and drain plugs located on the reduction
gear cover (33).
3.
Winch with disc brake: do not remove the level plug
located on the reduction gear cover. Instead, remove the
level plug located on the disc brake housing.
NOTICE
• Depending on ambient temperature it may take several
minutes for oil to flow from the disc brake level plug hole.
Wait 10 minutes after oil starts to flow from level plug hole
before re-installing plug fittings.
4.
Fill slowly until oil flows from the disc brake level plug
hole.
5.
Re-install the plugs.
CAUTION
• Do not over fill. Excess oil will reduce operating efficiency
and increase oil temperature.
• The use of unsuitable oil may result in excessive
temperature rise, loss of efficiency and possible damage to
the gears. Use only high quality rust and oxidation inhibiting
lubricant.
To Drain:
1.
Rotate the winch drum to align the reduction gear plugs to
the drain position. Drain plug is located at bottom center.
2.
Remove the reduction gear drain plug and install long pipe
nipple threaded at one end to 3/8-18 NPT. Remove drain
vent plug. Remove the disc brake drain plug.
NOTICE
• Always drain oil into a suitable container and inspect
drained oil for evidence of damage, metal shavings, dirt,
water, etc. Dispose of oil in an environmentally safe manner.
3.
Collect the drained oil and dispose of properly. If replacing
oil, refer to ‘To Fill’ instructions. Re-install the reduction
gear and disc brake plugs.
Motor Assembly
Lubrication for the motor is provided by the air line lubricator.
An air line lubricator must be installed in the air supply line as
close as possible to the motor inlet, but no more than 10 feet (3
metres) away. The lubricator must provide a minimum of 3
drops per minute of ISO VG 32 (10W) oil.
Wire Rope
Follow the wire rope manufacturer's instructions. At a minimum,
observe the following guidelines.
1.
Clean with a brush or steam to remove dirt, rock dust or
other foreign material on the surface of the wire rope.
CAUTION
• Do not use an acid-based solvent. Only use cleaning fluids
specified by the wire rope manufacturer.
2.
Apply a wire rope lubricant, Ingersoll-Rand LUBRI-
LINK-GREEN or ISO VG 100 (30W) lubricant.
3.
Brush, drip or spray lubricant weekly, or more frequently,
depending on severity of service.
Seals and Bearings
If winch is disassembled, clean all parts thoroughly and coat
bearings and seals with clean grease. Refer to the
'Recommended Lubricants' section. Use sufficient grease to
provide a good protective coat.
Summary of Contents for FA2A
Page 8: ...7 ...
Page 38: ...37 WINCH CROSS SECTION DRAWING ...
Page 39: ...38 WINCH ASSEMBLY PARTS DRAWING ...
Page 41: ...40 MOTOR ASSEMBLY PARTS DRAWING ...
Page 47: ...46 CONTROL VALVE ASSEMBLY PARTS DRAWING ...
Page 49: ...48 REMOTE PENDANT AND CONTROL VALVE ASSEMBLY PARTS DRAWING ...
Page 53: ...52 EMERGENCY STOP AND OVERLOAD ASSEMBLY PARTS DRAWING ...
Page 55: ...54 REMOTE EMERGENCY STOP AND OVERLOAD ASSEMBLY PARTS DRAWING ...