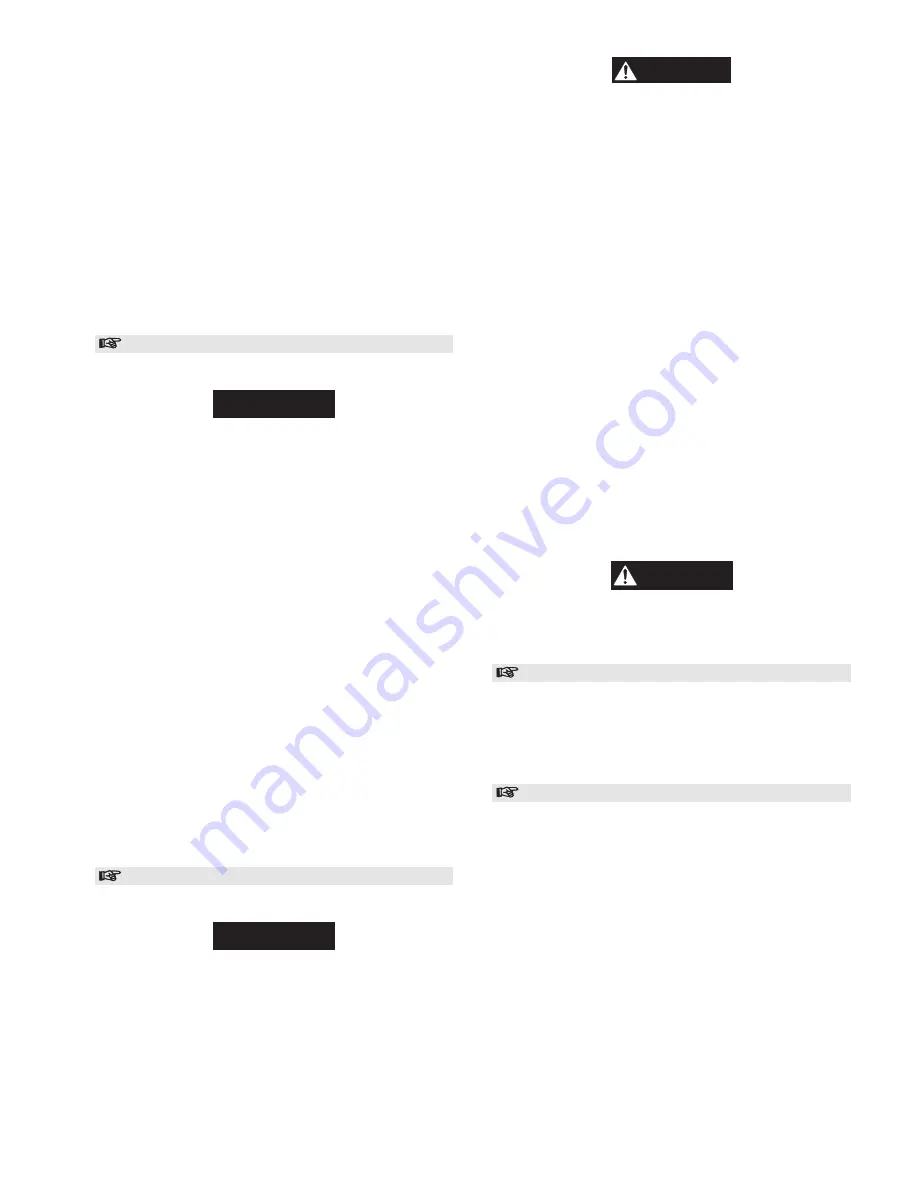
25
5.
Note hose route and fitting orientation for reassembly, then
disconnect fittings (513) from emergency stop valve (541).
6.
Remove capscrews (542). Remove emergency stop valve as
an assembly and store in a clean location until reassembly.
7.
Remove capscrews (538) and bracket (539) from shut off
valve (522).
8.
Note hose route and fitting orientation for reassembly, then
disconnect fittings (513), (519) and (622) from shuttle
valve (517).
9.
Separate shuttle valve (517) from shut off valve (522) at
elbow (537) by rotating shuttle valve counterclockwise.
Remove elbow (537).
10. Note fitting orientation for reassembly, then disconnect
fittings (513) and (622) from Delta ‘P’ valve (533).
Remove fittings (514), (515) and (519).
11. Separate bracket (529) by removing capscrews (531).
Remove bracket (527) by removing capscrews (528).
Remote Emergency Stop Disassembly
Optional feature. Refer to Dwg. MHP1323.
NOTICE
• During disassembly, take care to keep the work area free
from dirt and contamination. It is recommended that parts
be moved to a clean, suitable work area.
1.
Disconnect main air supply line at the winch.
2.
Disconnect disc brake air line from connector fitting (621)
located on valve assembly (355).
3.
Disconnect pendant hoses from valve assembly.
4.
Remove capscrews (608) and lift valve (355) and cover
(607) assembly.
5.
Remove capscrews (615) and separate cover (607) from
valve assembly (355).
6.
Remove capscrews (614) and lift manifold (606) from
motor housing (220).
7.
Remove gasket (611).
8.
Note orientation of muffler to shut off valve for reference
during assembly. Remove muffler (525), nipple (524) and
elbow (523) from shut off valve (522).
9.
Note fitting orientation for reassembly, then disconnect
hoses and fittings from shut off valve (522), shuttle valve
(517) and Delta ‘P’ valve (533).
10. Separate shuttle valve (517) from shut off valve (522) at
elbow (537) by rotating shuttle valve counterclockwise
(left, circular direction). Remove elbow (537).
11. Separate shut off valve (522) at nipple fitting (578) by
rotating shut off valve counterclockwise (left, circular
direction). Remove fitting (535).
Motor Disassembly
Refer to Dwg. MHP1310.
NOTICE
• Internal components of the motor are machined to very
close tolerances. Ensure that work area and parts are kept
very clean to prevent damage or contamination to
components.
1.
Disconnect air line to winch.
2.
Remove muffler (234) as an assembly.
WARNING
• The air motor weighs approximately 100 lbs. (45.3 kg).
Adequately support the air motor before removing the motor
mounting capscrews.
3.
Use a nylon sling and suitable hoist to support the motor
assembly.
4.
Remove capscrews (221) and pull motor straight away from
motor adapter (71).
5.
Place motor on a suitable clean bench with air inlet facing
up.
6.
Refer to ‘Control Valve Disassembly’ for manifold
removal.
7.
Remove capscrews (224) and pull exhaust manifold (233)
off of motor housing.
8.
Tip motor onto the open end. Remove capscrews (224) and
separate cover (223) from motor housing (220).
9.
Remove setscrew (218) and loosen capscrew (216) and
locknut (217). Pull counterweight (214) off of crankshaft
pin (213).
10. Remove capscrews (229) from cover assemblies (226) and
(227) and remove cylinder assemblies.
11. Rotate crankshaft slowly until the flat portion of the piston
assembly (240) can be lifted into the square portion of the
cylinder port in the motor housing. Lift the piston assembly
off the crankshaft pin (213) and slide back out through the
motor housing.
12. Repeat this operation for the other piston assembly.
13. Push spool (231) out of motor housing (220). Remove and
discard ‘O’ rings (230).
CAUTION
• Use a press to remove the following components. DO NOT
use a hammer to remove parts as this can cause damage to
the link rod and piston rod.
Piston Disassembly
1.
Remove piston sleeve (243) and ‘O’ ring (242) from the
piston and discard.
2.
Press out pin (246) and remove washers (248).
3.
Pull link rod (244) apart from piston rod (241).
4.
Press out bearings (245) and (247).
Crankshaft Disassembly
1.
Bend the locking tab on tab washer (203) out of the slot in
locknut (202).
2.
Use a wooden (or fiberglass) tool handle to lock the
crankshaft. Place it through two of the cylinder ports in the
motor housing and let the crankshaft pin come to rest on it.
3.
Remove locknut (202) and tab washer (203).
4.
Press the crankshaft assembly (only, NOT bearing (204))
out through the main cavity of the motor housing.
5.
Pull bearing (204) and attached retainer ring back out,
towards adapter side of motor housing.
Summary of Contents for FA2A
Page 8: ...7 ...
Page 38: ...37 WINCH CROSS SECTION DRAWING ...
Page 39: ...38 WINCH ASSEMBLY PARTS DRAWING ...
Page 41: ...40 MOTOR ASSEMBLY PARTS DRAWING ...
Page 47: ...46 CONTROL VALVE ASSEMBLY PARTS DRAWING ...
Page 49: ...48 REMOTE PENDANT AND CONTROL VALVE ASSEMBLY PARTS DRAWING ...
Page 53: ...52 EMERGENCY STOP AND OVERLOAD ASSEMBLY PARTS DRAWING ...
Page 55: ...54 REMOTE EMERGENCY STOP AND OVERLOAD ASSEMBLY PARTS DRAWING ...