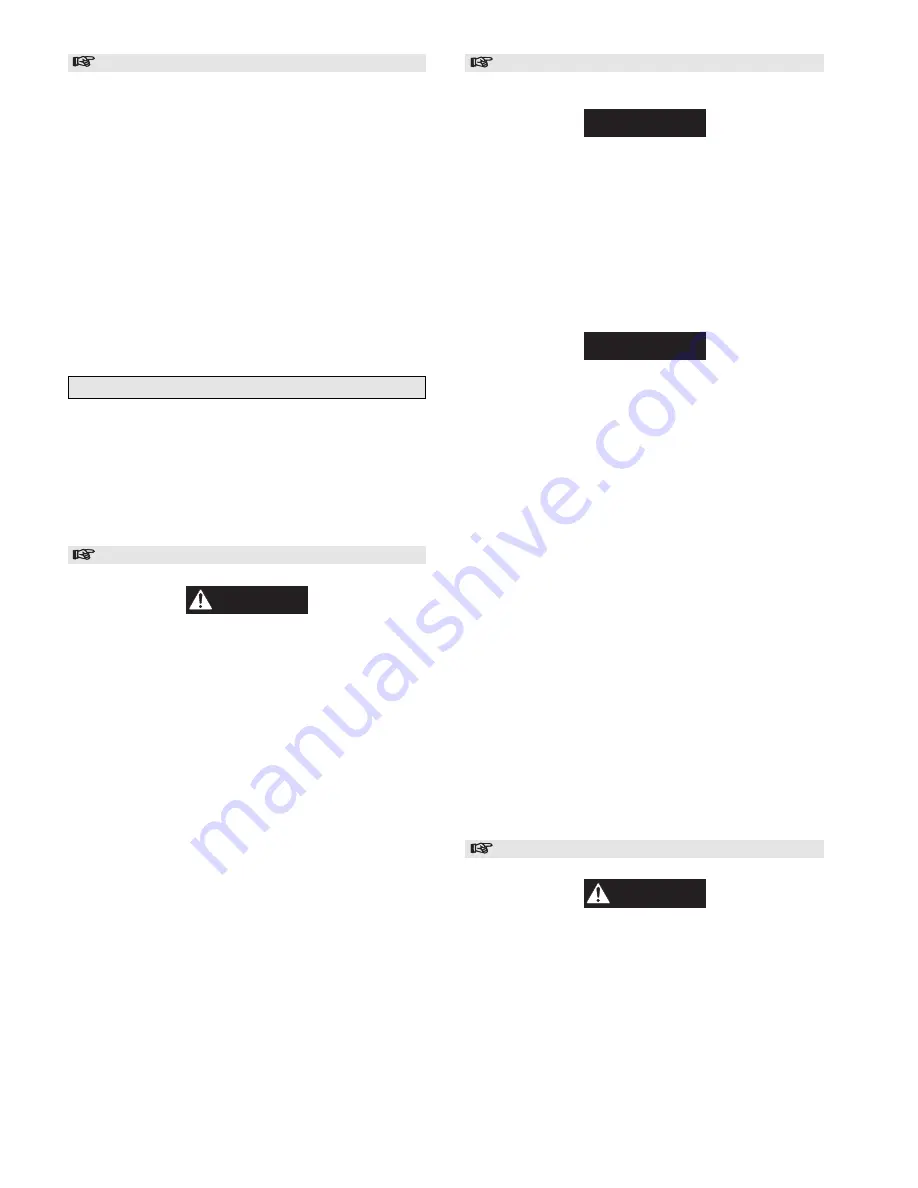
28
Repair
Actual repairs are limited to the removal of small burrs and other
minor surface imperfections from gears, shafts, housings and
machined surfaces. Use a fine stone or emery cloth for this
work.
1.
Worn or damaged parts must be replaced. Refer to the
applicable parts listing for specific replacement parts
information.
2.
Inspect all remaining parts for evidence of damage.
Replace or repair any part which is in questionable
condition. The cost of the part is often minor in comparison
with the cost of redoing the job.
3.
Smooth out all nicks, burrs, or galled spots on shafts,
bores, pins, or bushings.
4.
Examine all gear teeth carefully, and remove nicks or
burrs.
5.
Polish the edges of all shaft shoulders to remove small
nicks which may have been caused during handling.
6.
Remove all nicks and burrs caused by lockwashers.
Assembly
General instructions
•
use all new gaskets and seals.
•
replace worn parts.
•
assemble parts using match marks applied during
disassembly. Compare replacement parts with originals
to identify installation alignments.
•
lubricate all internal parts with rust and oxidation
inhibiting lubricant, ISO VG 100 (30W).
Thermoplastic Coated Parts Assembly
CAUTION
• During application of thermoplastic coating to assemblies
use a flame to localize the heat. Do not heat entire assembly.
Assemblies contain gaskets, ‘O’ rings and other components
that may be damaged by exposure to excessive heat.
1.
When assembling parts already coated, the mating areas can
be heated to soften the coating enough to flow together and
seal the parts.
2.
When installing a new component in an assembly, remove
coating from existing parts as necessary to ensure parts
mate correctly.
3.
Install fasteners and torque as required. Apply coating to
bare areas as described in ‘Thermoplastic Coating’
repairing surfaces instructions in the “MAINTENANCE”
section for areas larger than 1/16 inch (1.6 mm).
4.
Allow the repaired area to cool. Quenching with water is
acceptable. Rough spots, minor scorching and excess
coating deposits can be wet sanded to remove the
imperfections. To return the gloss finish, reheat the surface
carefully.
Motor Assembly
Refer to Dwg. MHP1310.
NOTICE
• When assembling the air motor keep the work area as clean
as possible. Dirt and contaminates are the biggest source of
component failure.
• Clean all components with a none residue solvent.
• Lubricate all ‘O’ rings with Dow Corning
®
111 Valve
Lubricant.
1.
Install ‘O’ rings (230) on spool (231) and lubricate.
2.
Press the spool (231) into the motor housing bore from the
motor adapter side until flush. Ensure ‘O’ rings are not
damaged during installation.
NOTICE
• If installing a new crankshaft assembly, new bearings (245)
are included. These are used because of the new mating
surface (pin (213)). See piston assembly for proper
installation procedures.
3.
Clean the center bore of the motor housing and lubricate.
4.
Take the locknut (202), tab washer (203), bearing (204) and
rotary valve seal assembly (208) off the back half of the
crankshaft assembly. Then insert the crankshaft assembly
through the main cavity.
5.
Lubricate the crankshaft and slide the rotary valve seal
assembly (208) (with the curved end facing the rotary valve
(208)) onto the shaft.
6.
Hold this crankshaft assembly and press the bearing and
retainer (204) in from the adapter side of the motor
housing.
7.
Place the tab washer (203) (curved surface up) onto the
crankshaft and then locknut (202). The flat side of locknut
(202) should be facing out and the curve of the locknut and
tab washer should match.
8.
Tighten locknut (202) to 60 in lb. (22 Nm). Use a wooden
(or fiberglass) tool handle to lock the crankshaft. Place it
through two of the cylinder ports in the motor housing and
let the crankshaft pin (213) come to rest on it. Loosen
locknut just enough to allow one of the locking tabs from
the tab washer (203) to be bent into one of the slots in the
locknut (202).
9.
Rotate crankshaft assembly, crankshaft should spin freely,
if not, correct problem before proceeding.
Piston Assembly
CAUTION
• Use a press and supports to avoid damaging the piston rod.
Press on the outer race of the bearings and support the piston
rod as close to the bearing as possible.
1.
Apply Loctite
®
609 to the bore of the piston rod (241) and
the outside of bearing (247).
2.
Press bearing (247) into piston rod (241) until bearing is
centered in piston rod.
3.
Press bearing (245) into large bore of link rod (244) until
centered in rod.
4.
Place link rod (244) over bearing (247) in piston rod.
5.
Insert washers (248) on both sides of bearing (247),
between link rod (244) and bearing (247).
Summary of Contents for FA2A
Page 8: ...7 ...
Page 38: ...37 WINCH CROSS SECTION DRAWING ...
Page 39: ...38 WINCH ASSEMBLY PARTS DRAWING ...
Page 41: ...40 MOTOR ASSEMBLY PARTS DRAWING ...
Page 47: ...46 CONTROL VALVE ASSEMBLY PARTS DRAWING ...
Page 49: ...48 REMOTE PENDANT AND CONTROL VALVE ASSEMBLY PARTS DRAWING ...
Page 53: ...52 EMERGENCY STOP AND OVERLOAD ASSEMBLY PARTS DRAWING ...
Page 55: ...54 REMOTE EMERGENCY STOP AND OVERLOAD ASSEMBLY PARTS DRAWING ...