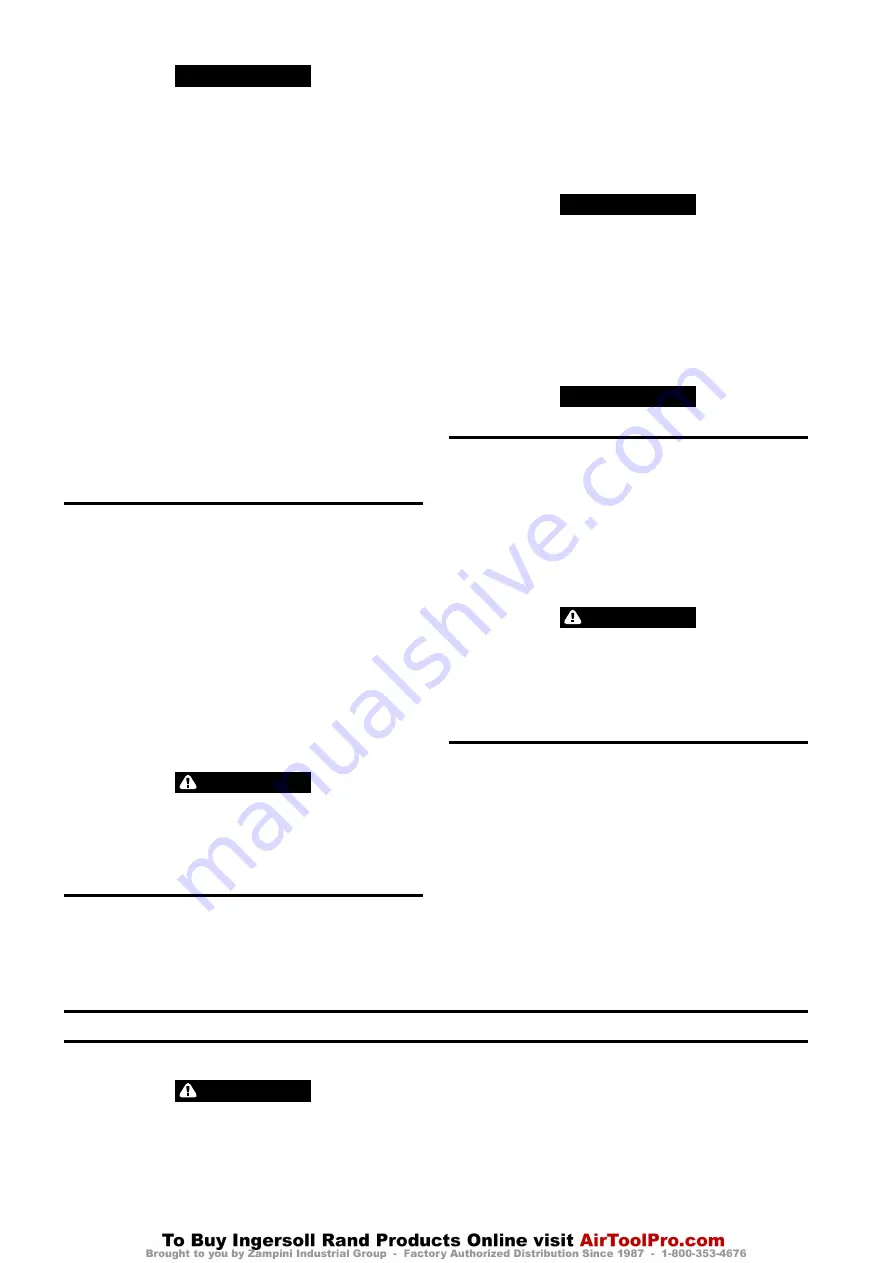
NOTICE
•
If winch overload occurs, overload device, if equipped, also stops winch. To
operate winch after an overload, reduce load and reset overload.
Emergency Stop Reset:
1. Rotate red stop button, in (counterclockwise) direction until red stop button
‘pops’ up.
2. Winch is ready to resume operation.
Pendant Control:
Refer to “Emergency Stop” section and Dwg. MHP1892 on page 13, A. Pendant
Handle; B. “Emergency Stop” Button; C. “ON” Button; D. Winch Control Levers.
n
Overload System (CE Models only)
The winch utilizes a direct acting load limiter to limit the maximum line pull to 160%
of the rated line pull. The limiter is a pressure regulator that limits the supply air to
a pressure that will not allow the winch to pull beyond 160% of the rated line pull.
Checking Overload Valve Setting:
Proper test and adjustment of overload should only be performed by an
Ingersoll Rand trained technician. The winch shall not be able to lift a load greater
than 160% of the rated utility load. If this is possible, adjustment is required.
1. Attach load line to a load that is calibrated to maximum rated load for winch.
2. Move control lever to haul-in position. If winch does not lift load, adjust the
adjustment screw. Refer to ‘Overload Valve Adjustment’ in the Product
Maintenance Information Manual.
Setting the Overload:
Attach load line to a load that is calibrated to 160% of winch rated capacity. Shift
control lever to haul-in position.
1. If overload valve activates, reset overload valve. Winch is ready for normal
operation.
2. If winch lifts higher than 160% of rated load, lower load. Turn jam nut
(counterclockwise) in 1/4 turn increments until overload valve activates when
control lever is shifted to haul-in position. After each 1/4 turn, retest winch.
n
Tensioning System (optional feature)
Refer to Dwg. MHP1865 on page 12, A. Pressure Gauge; B. Regulator; C. Auxiliary
Valve (shown in Normal Position); D. Control Valve.
With auxiliary valve in the NORMAL position, winch provides normal operation.
Placing valve selector in TENSIONING position allows winch to automatically operate
to haul-in slack wire rope to maintain tension.
Auxiliary valve provides preset air pressure to air motor and disc brake. This allows
brake to be released and winch to overhaul during TENSIONING operations. In this
position, winch will maintain constant tension on wire rope.
Auxiliary valve is pre-set at zero from the factory. Specific adjustments must be made
in the field. Adjustments can be modified at any time to accommodate the load
conditions. Refer to ‘Regulator Adjustment’ in the Product Maintenance Information
Manual.
n
Tensioning System (operation)
1. Place auxiliary valve in NORMAL position.
2. Operate winch normally to position end of load line.
3. Connect load line to load.
WARNING
•
Ensure slack load line is taken up by operating winch control valve with
selector in NORMAL position. If selector lever is placed in TENSION position
the winch will immediately attempt to establish line tension causing line
to ‘snap’ resulting in injury or damage to property.
4. Operate winch normally to remove slack from load line.
5. Actuate valve to TENSION position to set winch to automatically haul-in load line
and maintain line tension.
n
Winch Brakes
n
Manual Drum Band Brake
The manual drum band brake may be applied by pushing down on handle and
released by pulling up. If handle is pushed down fully, it should lock in that position
and prevent drum rotation, until released by operator. The brake must be kept
properly adjusted to hold required load.
n
Automatic Drum Band Brake
The automatic drum band brake is a spring applied, air released brake which utilizes
an air actuated, spring loaded cylinder, that automatically disengages brake when
motor is operated. Air pressure in cylinder overcomes spring pressure to release
brake. When control valve is placed in neutral position, air in cylinder is vented and
spring automatically engages brake to prevent drum rotation.
The cylinder clevis must be kept properly adjusted to hold required load. Refer to
‘Adjustments’ in “MAINTENANCE” section in Product Maintenance Information
Manual for instructions.
NOTICE
•
Extended exposure to corrosive atmospheres can cause the band brake
lining to adhere to the drum. It is recommended when winch is not in
operation and in a no load condition that the band brake be left in a released
position.
n
Automatic Disc Brake
The automatic disc brake is a spring applied, air released brake. Using an air actuated,
spring loaded piston, the brake automatically disengages when motor is operated
and engages when throttle is returned to neutral position.
Air pressure ported through brake housing overcomes spring pressure and moves
piston which releases brake. When control valve is placed in neutral position, air is
vented, spring pressure overcomes air pressure and spring pressure moves piston,
engages brake and prevents drum rotation.
NOTICE
•
A minimum of 40 psig is required to release the brake.
n
Drum Locking Pin (optional feature)
Refer to Dwg. MHP2772 on page 13, A. Drum Lock Assembly; B. Engaged; C.
Disengaged.
The drum locking pin assembly is mounted on the outboard upright, opposite
motor. Handle movement must be parallel to the winch base. It should be engaged
if a load is left suspended. The word ‘TOP’ is stamped into the handle for correct
orientation and must be visible from above.
To engage Drum Locking Pin:
When facing the handle, pull handle away from the outboard upright and pivot it
to the left. Handle pivot capscrew will be in closest position to drum flange. Operate
winch very slowly until locking pin engages one of the drum flange holes.
WARNING
•
Ensure that all braking mechanisms are engaged and all personnel are clear
of winch load and rigging before disengaging locking pin.
•
Extremely difficult locking pin release is an indication that load is held by
locking pin and braking mechanisms are not functioning properly. Do not
release locking pin until load control is established.
To disengage Drum Locking Pin:
When facing the handle, pull handle away from the outboard upright and pivot it
to the right. Handle pivot capscrew will be in furthest position from drum flange.
n
Limit Switches
Limit switches are standard on -CE winches.
Pre-set limit switch settings prevent winch wire rope payout and haul-in by stopping
air flow to the winch motor when a set point has been reached. It is the owner’s and
operator’s responsibility to adjust winch operating limits prior to using the winch.
To adjust the limit switch set points, refer to ‘Limit Switches’ on page 6.
INSPECTION
Inspection information is based in part on American Society of Mechanical Engineers
Safety Codes (ASME B30.7).
WARNING
•
All new or repaired equipment should be inspected and tested by
Ingersoll Rand trained Service Technicians to ensure safe operation at
rated specifications before placing equipment in service.
•
Never use a winch that inspection indicates is damaged.
Frequent and periodic inspections should be performed on equipment in regular
service. Frequent inspections are visual examinations performed by operators or
Ingersoll Rand trained Inspectors and include observations made during routine
equipment operation. Periodic inspections are thorough inspections conducted by
Ingersoll Rand trained Service Technicians. ASME B30.7 states inspection intervals
depend upon the nature of the critical components of the equipment and the
severity of usage. Refer to “Inspection Classifications” chart and “Maintenance
Intervals” chart in Product Maintenance Information Manual for recommended
maintenance intervals.
8
Form MHD56434 Edition 6