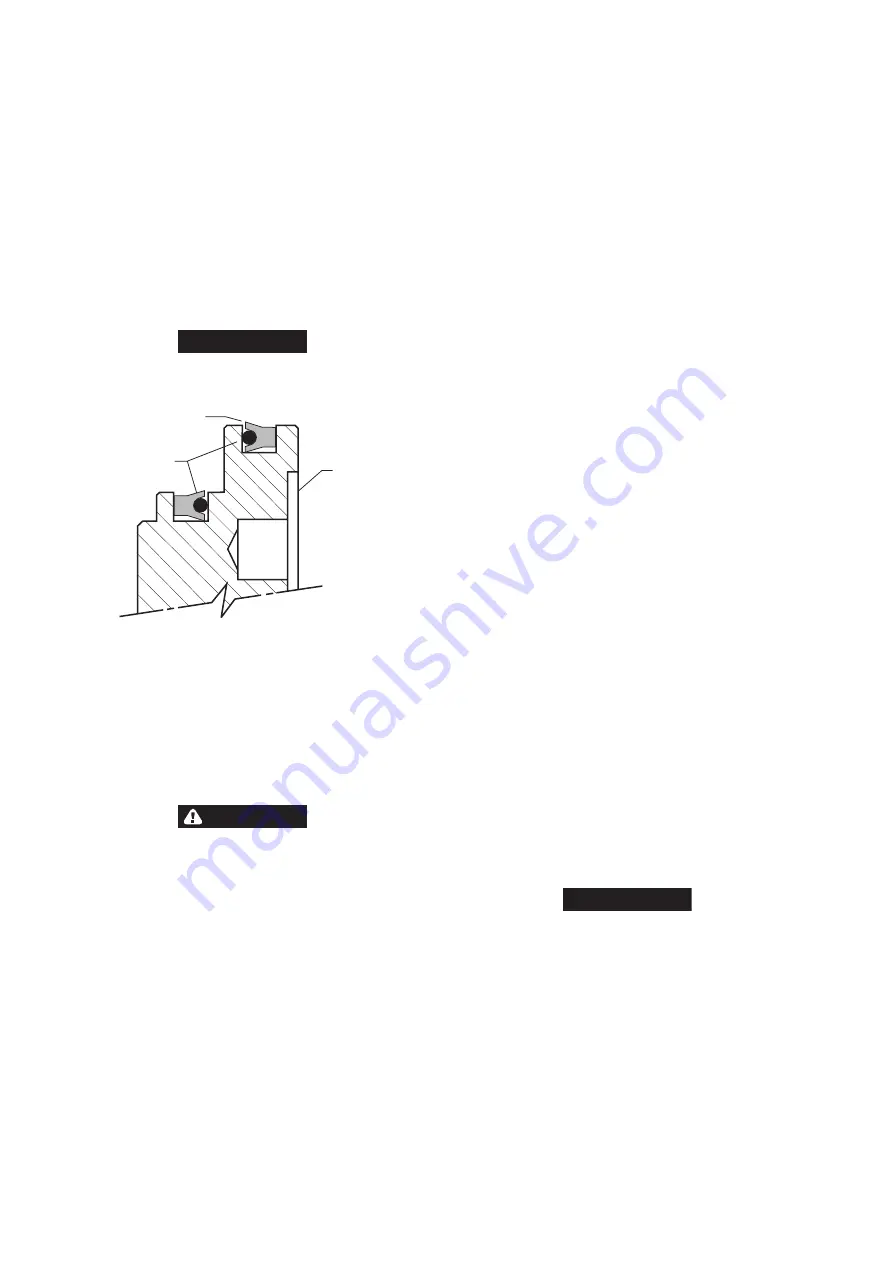
10
Form MHD56332 Edition 1
15. Install splined hub (21) so splined side on outside diameter goes on first. Install
capscrew in collar (13) and place on shaft (35). Maintain pressure on collar to
keep it against splined hub (21) and tighten capscrew in collar (13).
16. Lubricate and install ‘O’ ring (26) on drum shaft (41).
17. Install brake housing (17) on drum shaft (41).
18. Position brake housing so brake port is in the 2 o’clock position (as viewed from
the motor end). Install drain plug (25) in brake housing at the 6 o’clock
position.
19. Install reducer fitting (28) and breather (29) in the top of the brake housing
(17).
20. Lubricate friction plates (19) with a light motor oil (refer to ‘Recommended
Lubricants’ in Product Information Manual). Install friction plates (19) and drive
plates (18) in brake housing (17). Begin with a friction plate then alternate with
drive plates between friction plates. Ensure splined teeth mesh. Do not force
plates into place during installation.
21. Lubricate and install seals (11) and (12) in brake piston (10) grooves so seal lips
face each other. Do not overstretch seals during this procedure. Refer to
Dwg.MHP0139 on page 10.
22. Install brake piston assembly in brake housing so stepped side enters first.
Gently tap into position using a soft mallet until seated.
23. Install one brake spring (9) in each brake spring hole.
24. Lubricate and install ‘O’ ring (5) in groove on brake housing (17).
NOTICE
• ‘O’ ring, item (5) listed in step 24 refers to part number 51484 as shown on
disc brake Dwg. MHP2786. This part must be placed between brake housing(17)
and motor adapter (6).
(Dwg. MHP0139)
25. Install brake reaction plate (8) over springs (9).
26. Two threaded holes in motor adapter (6) are centered between mounting bolt
holes. Install motor adapter with these two holes as close as possible to the
6o’clock position.
27. Secure motor adapter (6) with five capscrews (4) using Loctite® 242. Torque
to35 ft lbs (47 Nm). On winches with a disc brake install capscrews (93) evenly
to compress brake springs. Do not allow mounting adapter to become cocked.
Evenly hand tighten all capscrews before applying final torque.
28. On disc brake equipped winches, install shaft (7) on end of drive shaft (35).
29. Lubricate and install ‘O’ ring (5) in groove on motor adapter (6).
30. Ensure oil seal (2) is installed in bore of motor assembly. Seal lip must face into
motor assembly.
31. Place gasket (470) on mounting flange (216) and align holes.
WARNING
• The air motor weighs approximately 117 lb. (53 kg). Adequately support air
motor while installing motor mounting capscrews.
32. Position winch in a horizontal position. Using suitable lifting equipment
carefully slide motor assembly onto the drive shaft (35). Position throttle
assembly at the top. Be careful not to damage oil seal (2).
33. Install the motor assembly to motor adapter (6) with capscrews (97) and
lockwashers (96). Lightly coat capscrew threads with Loctite® 242 and torque to
25 ft-lbs (34 Nm).
34. On winches with a disc brake install fitting (31) and dump valve (30) into brake
release port. Install vented fitting (27) in dump valve (26) between dump
valve(26) and hose assembly (44) or tubing assembly (64).
Manual and Automatic Band Brake
Refer to Dwg. MHP0209.
1. Install pivot bracket (122) on the end of arm (124) with pin (121), washer
(123)and cotter pin (102). Recessed side of the threaded hole must be toward
the band side.
2. Install connecting link (125) on the arm (124) and secure in position with
pin(121), washer (123) and cotter pin (121). Assemble connecting link (125) so
curved surface matches contour of the brake band.
3. Install halves of brake band (128) to the connecting link (125) and secure with
pins (101), (121) and cotter pins (102).
4. Lift the winch assembly, with a suitable hoist, approximately 6 inches (15 cm)
off the floor or work bench.
5. Position the brake band sub-assembly around the brake diameter on the
drum(80) so the arm (124) lays at the bottom. When positioned, lower the
winch.
6. Mount pivot bracket (122) on the inside surface of the siderail (130) and secure
in position with capscrews (116) and lockwashers (117).
7. Screw link stud into handle and install the handle (104) in the lug on the end of
the brake band (128). Lubricate the pivot points being careful not to get grease
on the brake band lining.
8. Pull the halves of the brake band together and install pin (101) through the lug
on band (128) and the adjusting screw (103) of the handle assembly.
9. Install stop plate (126) on the inside of the siderail (131) with capscrews
(119)and washers (117). Install adjusting screw (127) and locknut (120)
through the siderail (131) and stop plate (126) until it contacts the arm (124).
10. Adjust brake as described at the start of the “MAINTENANCE” section.
Automatic Band Brake Actuator
11. Install bracket (118) on siderail (139) with capscrews (116) and
lockwashers(117).
12. Screw nut (108) and clevis (107) onto cylinder rod.
13. Attach brake lever (105) to brake band (128).
14. Install cylinder (110) so it connects with bracket (118) and brake lever (105).
Use pins (106), washers (129) and cotter pins (102) to secure in position.
15. Install dump valve (112) fittings and hose (115) to the cylinder (110). Adjust
automatic brake as described at the start of the “MAINTENANCE” section. Install
pipe plug (98) in end cover (95).
Drum Guard
Refer to Dwg. MHP2676.
1. Secure frames (802) and (801) to uprights (42) and (84) with capscrews
(809)and washers (96). Secure lifting lugs (83) to uprights with capscrews (90)
and washers (91).
2. Install panels (805) and (807) one at a time, beginning with either the
upper(807) or lower (805) panel.
3. Install first crossbar (806) with nuts (804).
4. Attach panel to crossbar (806).
5. Hold second panel (805) in place and install second crossbar (806) by sliding
through [hooked] edges of the two panels.
6. Secure crossbar (806) with nuts (804).
7. Continue until all panels are in place.
8. Tighten all fasteners and check drum guard is secure. Ensure wire rope does not
interfere with drum guard during winch operation.
Limit Switch Assembly (optional feature)
Refer to Dwgs. MHP2670.
1. Secure limit switch assembly to upright (84) with capscrews (97) and washers
(96).
2. Install hose connections. Refer to label 71459929.
Press Roller
Refer to Dwg. MHP2695.
Two people are recommended when installing press roller assembly.
1. If shaft collars (404) have been removed, replace and install in uprights (42)
and(84), and in both ends of arm (407). Grease bushings (404) for ease of
installation.
2. Install rollers (402) on smaller ends of press roller arm (407) and secure with
capscrews (408) and washers (409). Apply a small amount of Loctite® 242 to
threads of capscrews.
3. Install springs (405) and (406) so that the shorter end of springs are towards the
inner portion of the arm (407) where the tabs are located.
4. One person positions press roller so the top of arm (407) is curved up towards
the under side of the drum (80), and holds press roller in place while the other
person completes installation.
5. Adjust both springs (405) and (406) so that the long end of springs are on the
inside of siderail (82).
NOTICE
• Do not engage shorter end of spring behind tabs of arm (407) until after
shaft (403) has been installed and secured, and press roller assembly adjusted
to center of drum.
6. Install shaft (403) through hole in leg of upright (42) only.
7. Install one collar (410) on end of shaft (403) between upright and press roller
assembly. Do not tighten collar (410) until steps 10 and 11 have been
completed.
8. Install shaft (403) through press roller assembly (400).
9. Install second collar (410) and slide shaft through hole in leg of upright
(84).Ensure that the long end springs (405) and (406) are still between the
siderail(82) and drum (80). Do not tighten collar (410) until steps 10 and 11
have been completed.
10. Secure shaft (403) to uprights using capscrews (408) and washers (409). Apply a
small amount of Loctite® 242 to threads of capscrews.
11. Adjust press roller assembly so that it is centered between the drum flanges, and
tighten collars (410).
Seal Lip
Seal
Brake
Piston