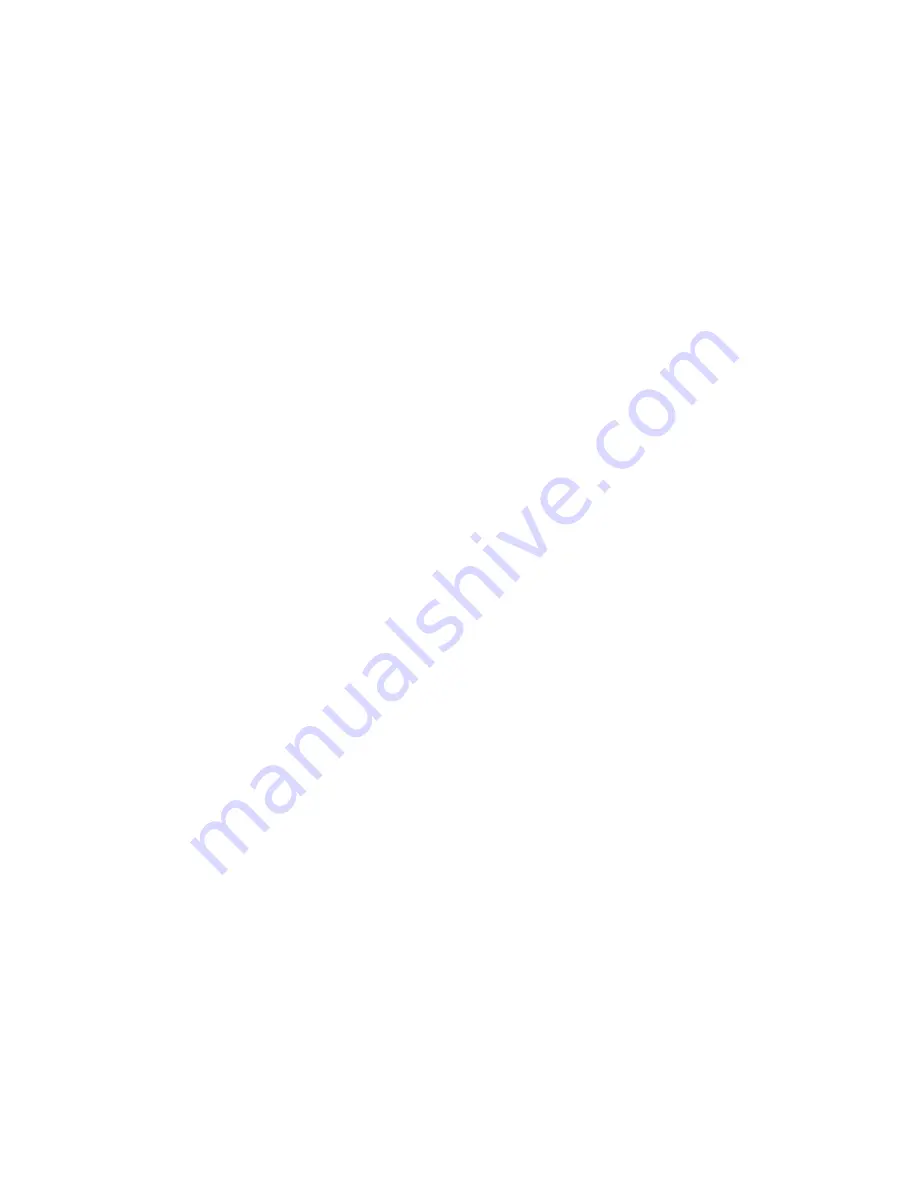
Book 43212455 (11/03)
15
SECTION 4 – SYSTEM DESCRIPTION
General
The CMH air compressors are semi-packaged, air cooled units designed for power take-off applications.
Each unit is designed to operate at ambient temperatures from - 10
°
F to 125
°
F (-23.3
°
C to 51.7
°
C). For
the actual delivery of each unit at its rated operating pressure, refer to the typical General Data Decal
supplied with each unit, and to the table in Section 5.
The unit includes an oil flooded, rotary, screw-type air compressor, a compressor inlet system, a capacity
control system, a compressor lubricating oil system, a compressor discharge system as well as basic
instrumentation. The compressor inlet system includes an air intake cleaner with a service indicator. The
capacity control system includes a pressure regulator linked to a compressor inlet unloader valve. The
compressor lubricating oil system includes an air-cooled type oil cooler, an oil filter, and oil control valve
and an oil separator tank and air receiver. The oil cooler is of the fin and tube-type construction that
requires forced draft cooling air. Basic instrumentation includes compressor discharge air pressure and
temperature gauges, and air cleaner restriction indicator.
The enclosure cabinet, in which most of the components are mounted, is of heavy gauge sheet steel and
is equipped with easy opening access panels for performing routine maintenance functions. Most routine
service can be performed without removing any panels.
Compression in the screw-type air compressor is created by the meshing of two sets of helical rotors
(male and female) on parallel shafts enclosed in a heavy-duty cast iron housing with air inlet and outlet
ports located at opposite ends. The male rotor has four lobes, 90 degrees apart and the female rotor has
six grooves 60 degrees apart. The grooves of the female rotor mesh with and are driven by the male
rotor. Thrust taper roller bearings at the rear of the air end prevent longitudinal movement of the rotors.
As rotation of the compressor occurs, the rotors unmesh and free air is drawn into the cavities or pockets
between the male rotor lobes and the grooves of the female rotor. The air is trapped in these pockets and
follows the direction of rotation of each rotor. As soon as the inlet port is closed, the compression cycle
begins and the trapped air is directed to the opposite or discharge side of the rotor housing. As the rotors
mesh, the normal free volume of air is decreased and the pressure increased until the closing pocket
reaches the discharge port. Cooled lubricating oil is admitted to the compressor by being injected, in
metered amounts, directly into the rotor housing so that it passes on with the air being compressed. This
removes the heat of compression to a large degree and results in a relatively low, final discharge air
temperature.
Since the CMH Series compressor is of the positive displacement type, an air flow control system must be
provided to regulate the volume of air passing through the compressor to match the amount of service air
required by the customer.
Constant speed control unloads the compressor at a predetermined pressure while the driving unit
continues to operate at full speed. This is accomplished by an air operated regulator closing off the intake
to the compressor in an infinitely variable or stepless manner through the inlet unloader valve.
The discharge air pressure can be controlled between 77 and 200 psig (531 to 1379 kPa) by simple
readjustment of the speed and pressure regulator adjusting screw.
Summary of Contents for HP600CMH
Page 8: ...Book 43212455 11 03 8 IMPORTANT SAFETY INSTRUCTIONS ...
Page 9: ...Book 43212455 11 03 9 ...
Page 10: ...Book 43212455 11 03 10 ...
Page 14: ...Book 43212455 11 03 14 fold ...
Page 37: ...Book 43212455 11 03 37 ...
Page 44: ......