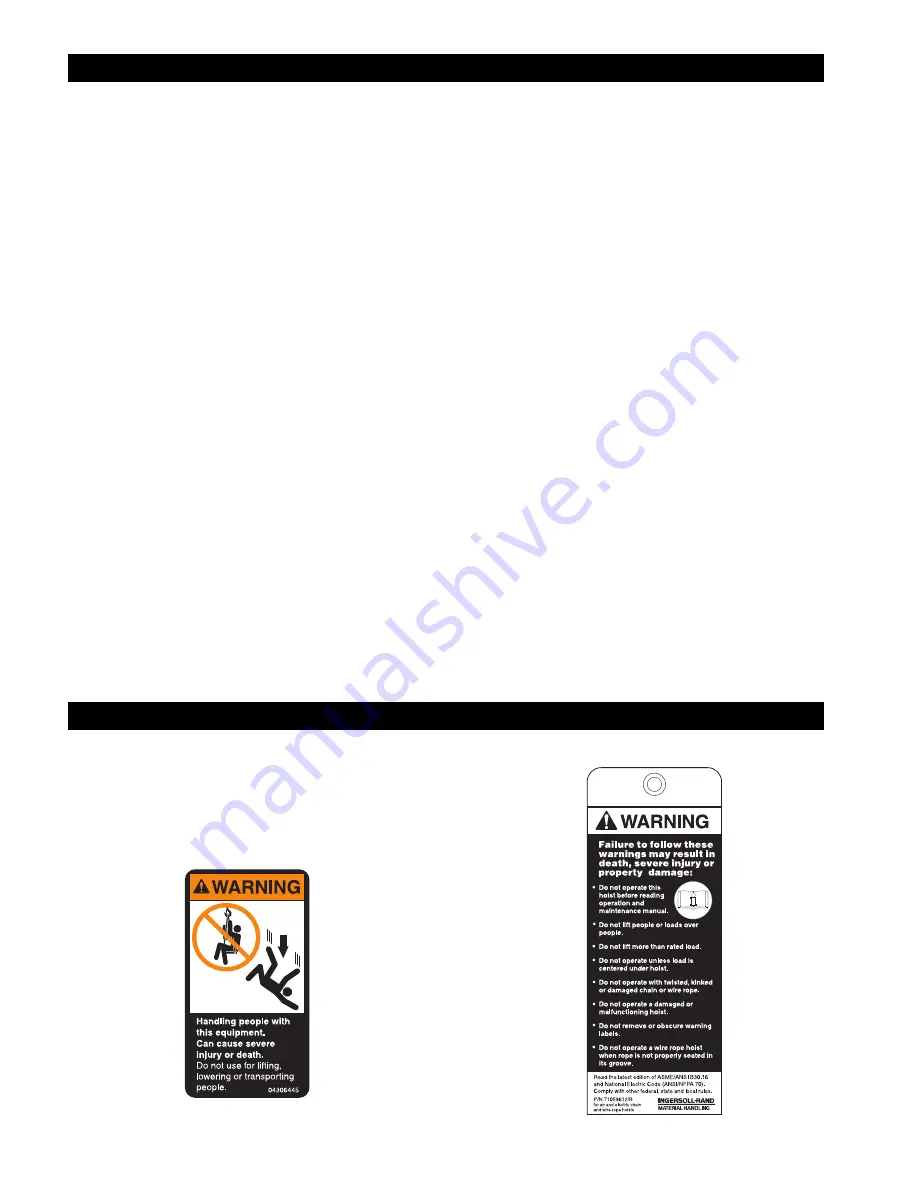
4
SAFE OPERATING INSTRUCTIONS
WARNING TAG AND LABEL
Each hoist is supplied from the factory with the warning tag and
label shown. If the tag or label is not attached to your unit, order
a new tag or label and install it. Refer to the Parts List for the
part number. Read and obey all warnings and other safety
information attached to this hoist. Tag and label are shown
smaller than actual size.
The following warnings and operating instructions have been
adapted in part from American National (Safety) Standard
ASME B30.16 and are intended to avoid unsafe operating
practices which might lead to injury or property damage.
Ingersoll-Rand recognizes that most companies who use hoists
have a safety program in force at their facility. In the event that
some conflict exists between a rule set forth in this publication
and a similar rule already set by an individual company, the
more stringent of the two should take precedence.
Safe Operating Instructions are provided to make an operator
aware of dangerous practices to avoid and are not necessarily
limited to the following list. Refer to specific sections in the
manual for additional safety information.
1.
Only allow personnel trained in safety and operation of this
product to operate and maintain the hoist.
2.
Only operate a hoist if you are physically fit to do so.
3.
When a “DO NOT OPERATE” sign is placed on the hoist,
or controls, do not operate the hoist until the sign has been
removed by designated personnel.
4.
Before each shift, check the hoist for wear and damage.
Never use a hoist that inspection indicates is worn or
damaged.
5.
Never lift a load greater than the rated capacity of the hoist.
Refer to “SPECIFICATIONS” section.
6.
Keep hands, clothing, etc., clear of moving parts.
7.
Never place your hand in the throat area of a hook.
8.
Always rig loads properly and carefully.
9.
Never use the load chain as a sling.
10. Be certain the load is properly seated in the saddle of the
hook. Do not tipload the hook as this leads to spreading and
eventual failure of the hook.
11. Do not “side pull” or “yard”.
12. Make sure everyone is clear of the load path and there are
no objects in the way of the load. Do not lift a load over
people.
13. Never use the hoist for lifting or lowering people, and
never allow anyone to stand on a suspended load.
14. Ease the slack out of the chain when starting a lift. Do not
jerk the load.
15. Do not swing a suspended load.
16. Never suspend a load for an extended period of time.
17. Never leave a suspended load unattended.
18. Pay attention to the load at all times when operating the
hoist.
19. After use, properly secure hoist and all loads.
20. The operator must maintain an unobstructed view of the
load at all times.
20. Never operate a hoist with twisted, kinked or damaged
chain.
21. After use, or when in a non-operational mode, the chain
hoist should be secured against unauthorized and
unwarranted use.
22. Do not do anything you believe may be unsafe.
23. Never splice a hoist chain by inserting a bolt between links
or by any other means.
24. Do not force a chain or hook into place by hammering. Do
not insert the point of the hook into a chain link.
25. Do not expose the sling chain to freezing temperatures, and
do not apply sudden loads to a cold chain.
26. Follow the lubrication instructions.
27. Do not attempt to repair load chains or hooks. Replace
them when they become worn or damaged.
28. Periodically inspect the hoist thoroughly and replace worn
or damaged parts.
29. Shut off air supply before performing maintenance on the
hoist.
30. Do not use the load chain as a ground (earth) for welding.
Do not attach a welding electrode to a hoist or chain.
Part Number:
04306445
Part Number:
71059612
Summary of Contents for LCA015
Page 26: ...25 SERVICE NOTES ...
Page 27: ...26 SERVICE NOTES ...
Page 31: ...30 LCA030S AND LCA060D HOIST ASSEMBLY PARTS DRAWING 3 and 6 ton Hoist Capacities Dwg MHP1464 ...
Page 33: ...32 LCA060S AND LCA120D HOIST ASSEMBLY PARTS DRAWING 6 and 12 ton Hoist Capacities Dwg MHP1465 ...
Page 50: ...49 SERVICE NOTES ...