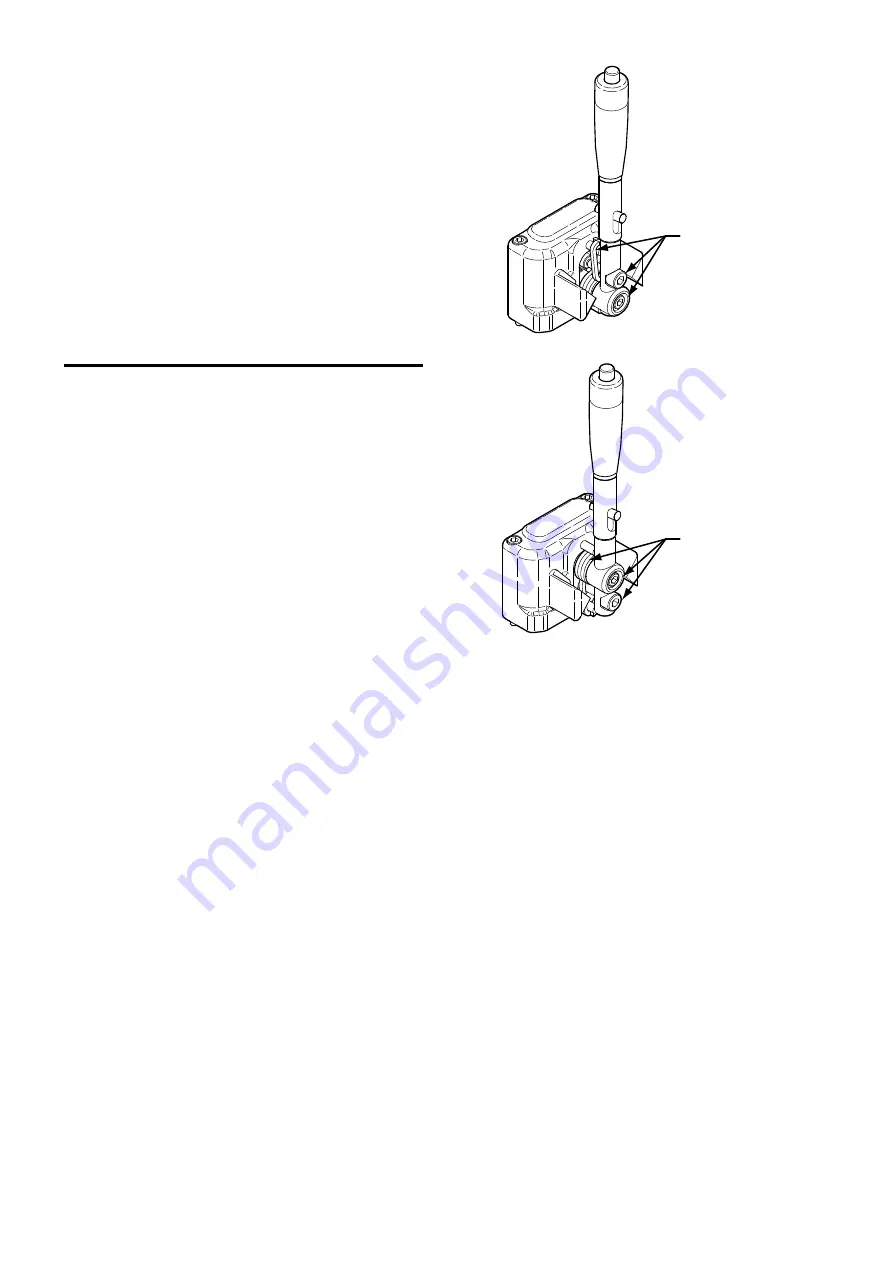
Inspect bearings for
•
-
loss of grease and evidence of grit, dirt or other contaminants. All motor
bearings are factory lubricated and sealed. If dry or contaminated, replace
the bearing.
•
-
damage. Inspect roller bearings (needle). At any indication of damage or
contamination, replace bearings.
Inspect disc brake for
•
-
wear. Replace brake discs if grooving pattern is no longer visible or if discs
are cracked or chipped.
-
thickness of disc. If less than 0.047 in (1.2 mm), replace.
n
Repair
Actual repairs are limited to the removal of small burrs and other minor surface
imperfections from gears, shafts, housings and machined surfaces. Use a fine stone
or emery cloth for this work.
1. Worn or damaged parts must be replaced. Refer to applicable parts listing for
specific replacement parts information.
2. Inspect all remaining parts for evidence of damage. Replace or repair any part
which is in questionable condition. The cost of the part is often minor in
comparison with the cost of redoing the job.
3. Smooth out all nicks, burrs or galled spots on shafts, bores, pins or bushings.
4. Examine all gear teeth carefully and remove nicks or burrs.
5. Polish edges of all shaft shoulders to remove small nicks which may have been
caused during handling.
6. Remove all nicks and burrs caused by lockwashers.
n
Assembly
Refer to the Product Parts Information Manual for drawings unless specified
elsewhere.
General instructions:
•
-
use new gaskets and seals.
•
-
replace worn parts.
•
-
assemble parts using match marks applied during disassembly. Compare
replacement parts with originals to identify installation alignments.
n
Control Valve Assembly
Refer to Dwg. MHP2729.
1. Install bushings (133) and (141) in valve housing (135).
2. Install pins (132) in spindle shafts (115), so they extend an equal amount on both
sides.
3. Install retainer (140), spindle shaft (115), key (136) and gear cam (139) in valve
housing.
4. Install retainer (140), spindle shaft (131), key (136) and gear (138) in valve
housing. Ensure keys are vertically aligned and gear teeth are meshed.
5. If handle was disassembled, install spring (130) and handle spool (123) in lever
shaft (128). Align hole in handle spool (123) with slot in lever shaft (128) and
install pin (120) so it extends an equal amount on both sides. Install ʽOʽ ring
(122) on cap (121) and screw cap (121) into lever shaft (128).
6.
Vertical Wire Rope Take-off Angle:
a. Install pin (134) in the top pin hole in valve housing (134).
b. Install lever assembly in coupling (124). Install spring (116) and coupling/
handle assembly on lower spindle shaft (115). Align notch in coupling with
pin in spindle shaft. Spring (116) ends will point up. Refer to Dwg. MHP2998
c. Install capscrew (126) and lockwasher (125) through coupling (124) and
lower hole in lever shaft (128).
or
7.
Horizontal Wire Rope Take-off Angle:
a. Install pin (134) in the lower pin hole in valve housing (134).
b. Install lever assembly in coupling (124). Install spring (116) and coupling/
handle assembly on top spindle shaft (115). Align notch in coupling with pin
in spindle shaft. Spring (116) ends will point down. Refer to Dwg. MHP2998
c. Install capscrew (126) and lockwasher (125) through coupling (124) and top
hole in lever shaft (128).
8. Install spools (142) in valve housing (135).
9. Install emergency stop housing assembly to valve housing (135). Install shoulder
screw (127). Tighten capscrews (126) and (127) to secure emergency stop
housing.
10. Install capscrews (118), lockwashers (2) and stop plate (119) on valve housing
(135).
11. Check operation of control valve to ensure smooth movement and ability to
spring return and lock in neutral.
Vertical
(Standard)
Note:
position
of coupling,
shoulder screw
and spring.
Horizontal
Note:
position
of coupling,
shoulder screw
and spring.
(Dwg. MHP2998)
n
Motor Assembly
Refer to Dwg. MHP2812.
1. Clean the grease from bearings (91).
2. Clean interior and exterior diameter of bearings with Loctite® 7063 or equivalent.
3. Put a continuous thin film of Loctite® 603 or equivalent on interior diameter of
bearing (91). Refer to Dwg. MHP2644 on page 11, A. Use a continuous thin
film of Loctite® 603 or equivalent to bond one bearing on each gear. Apply where
arrows indicate; B. Do not bond bearings on this side of gears; C. Use of
continuous thin film Loctite® 603 or equivalent; D. Note: Wait 10 minutes with
the housing in this position, to ensure proper bond; E. Install splined hub (75)
and rotate to ensure a proper bond.
4. Apply a continuous thin film of Loctite® 603 or equivalent on bearing diameter
on drive gear (92) and install bearing (91).
5. Install a second bearing (91), not bonded, on drive gear (92).
6. Apply a continuous thin film of Loctite® 603 or equivalent on interior diameter
of bearing (91).
7. Apply a continuous thin film of Loctite® 603 or equivalent on bearing diameter
on idle gear (104) and install bearing (91).
8. Install a second bearing (91), not bonded, on idle gear (104).
9. Apply a continuous thin film of Loctite® 603 or equivalent on bore for bearings
in the motor housing (87).
10. Install drive gear (92) and idle gear (104) into motor housing, ensure the drive
gear and idle gear are completely inside motor housing and leave the motor
housing in a position as shown in Dwg. MHP2644 on page 11, for 10 minutes.
11. Turn the gears with coupling and a tool. Check bearings do not rotate on bonded
diameters and gears rotate freely.
12. Install pins (88) in motor cover (97).
13. Install exhaust washer (99) with a drop of Loctite® 601 or equivalent on motor
cover.
14. Install ‘O’ rings (90) on motor cover (97).
15. Install motor cover (97) on motor housing and secure with capscrews (107).
16. Lubricate ‘O’ rings (85) on valves (94) and (105). One ‘O’ ring is mounted in a
special groove. Ensure a good assembly.
17. Install springs (96) and valve assemblies (94) and (104) in motor cover (97).
18. Lubricate and install ‘O’ rings (166) on check valve (83). Install ball (84) and check
valve assembly in motor housing (87).
19. Check to ensure motor gears turn smoothly in both directions.
10
Form MHD56305 Edition 4