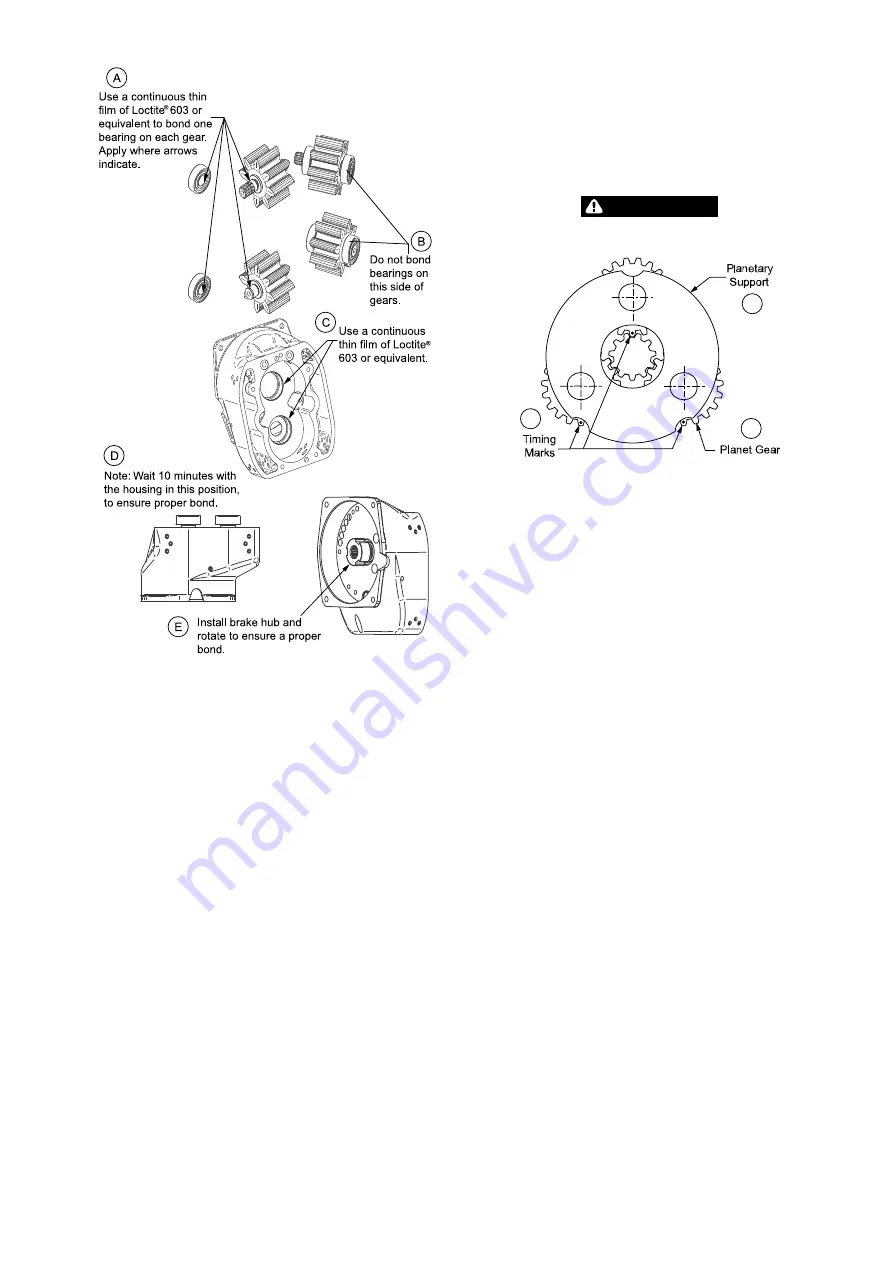
(Dwg. MHP2644)
Motor Emergency Stop End Cover:
Refer to Dwg. MHP2812.
1. Lubricate and install ‘O’ ring (201) and seal (189) on base plate (199).
2. Lubricate and install ‘O’ ring (197) to plunger (198).
3. Install diaphragm (196) and washer (195) with stop nut (194) on plunger (198)
and insert into base plate (199). Ensure plunger assembly moves freely in bore
of base plate.
4. Insert base plate (199) with plunger into motor cover (97).
5. Lubricate and install ‘O’ rings (204) on valve seat (205).
6. Place washer (206), diaphragm (212), cap (211), seal (203), sleeve (209) and
washers (206) and (208) onto capscrew (214) and insert into valve seat (205).
Apply a thin film of Loctite® 243 or equivalent to capscrew threads. Do not over
tighten capscrew.
7. Place seal (210) and cap (202) on capscrew (62). Place spring (213) on cap (202).
8. Install valve seat assembly into emergency stop end cover (185).
9. Lubricate and install ‘O’ ring (191) on regulating screw (192); insert into
emergency stop end cover (185) avoiding damage to the ‘O’ ring. Secure with
screw (102). Install screw (102) with Loctite® 243 or equivalent.
10. Lubricate and install spring (193).
11. Install ‘O’ rings (187) to valve seat (186).
12. Insert axle (188) into valve seat (186) then install seals (189) on each end of axle
(188).
13. Insert valve seat (186) into emergency stop end cover (185).
14. Insert ball (84) into emergency stop end cover (185).
15. Install gasket (101) on motor cover (97).
16. Install emergency stop end cover (185) on motor cover (97) and secure with
capscrews (103).
17. Insert plug (182) if removed during disassembly.
18. Install setscrew (180) in emergency stop end cover (185).
19. Install ‘O’ rings (90) on emergency stop end cover (185).
20. Install control valve assembly.
21. If pendant adapter plate (605) or (613) was removed from motor cover (83), refer
to pendant assemblies for installation.
n
Reduction Gear Assembly
Refer to Dwg. MHP2807.
1. Install oil seal (17) in the bore of the reduction gear end cover (15) so seal lip is
toward the planet assembly side.
2. Lubricate and install ‘O’ ring (16) on outside diameter of reduction gear end cover
(15). Install plug (14).
3. Press bearings (13) and (39) into the reduction gear end cover (15). Install retainer
ring (12) on the gear shaft (20).
4. Press gear shaft (20) into reduction gear end cover (15).
5. Install ring gear (19) and bearing (21) on gear shaft (20) and secure in position
with retainer ring (94). Install assembly in reducer housing (27).
6. Press bearing (35) onto the sun gear (34) and locate with retainer ring (36). Install
sun gear (34) with bearing (35) in the planet gear support (32) and secure with
retainer ring (49).
7. Install two bearings (28) with a spacer (30) between in the bore of each planetary
gear (31).
8. Install bearing rings (29) in each bearing (28).
9. Position each assembled planetary gear in the planet gear support (32) with the
timing mark as shown on drawing Dwg. MHP1406 on page 11, A. Planet Gear
Support; B. Timing Marks; C. Planet Gear. Carefully install gear shafts (33)
CAUTION
•
For assembly of planet gears, each planet gear must be positioned with the
timing mark as shown on Dwg. MHP1406.
B
A
C
(Dwg. MHP1406)
10. Install planetary gear assembly in the reducer housing (27).
11. Install ball bearing (38) on the planet gear support (32). Check planet gears, sun
gear and ring gear teeth mesh smoothly.
12. Place the reduction gear assembly in a vertical position with the planetary gear
end up.
13. Fill the gear assembly to within 1 in. (25 mm) of the top with clean oil. Refer to
“LUBRICATION” section in Product Information Manual.
14. Install new gasket (20) on reducer housing (27).
15. Apply Loctite® 243 to capscrews. Refer to “TORQUE CHART” on page 13.
n
Disc Brake Assembly
Refer to Dwg. MHP2807.
1. Lubricate and install ‘O’ rings (16) and (52) on piston (51).
2. Install new gasket (26) on reducer housing (27) if not done during reduction gear
assembly.
3. Assemble brake housing (41) to reducer assembly and secure with capscrew (24).
4. Ensure plug (14) is removed, then press piston assembly into brake housing (41).
Puller screw holes must face out.
5. Install spacer (54) and splined hub (53). Start with friction plate (55) followed by
drive plate (56), friction plate with springs (58), drive plate (56), friction plate (55),
drive plate (56) and finishing with friction plate with springs (58).
6. Install plug (14).
n
Winch Base and Drum Assembly
Refer to Dwgs. MHP2728, MHP2807 and MHP2812.
1. Install oil seal (77) and rear bearing (76) on drum end cover (78). Oil seal lip must
be toward the bearing.
2. Install drum end cover assembly on upright (62) and secure with capscrews (50)
and lockwashers (73).
3. Position the upright on several block of wood with the rear bearing (76) up.
4. Check that plate (72) is securely installed in the drum with countersunk screws
(71).
5. Lubricate the outside diameter of oil seal (77) and install drum assembly on rear
bearing.
6. Install oil seal (77) and front bearing (76) on drum end cover (78). Oil seal lip must
be toward the bearing.
7. Install drum end cover assembly on front upright (62) and secure with capscrews
(50) and lockwashers (73).
8. Lubricate the outside diameter of oil seal (77) and install front upright assembly
on drum (60).
9. Rotate uprights so they are aligned and install spacers (66) and siderails (68) with
capscrews (65) and (67), nuts (63) and washers (64). Longer capscrews (65) are
required to attach lifting lugs (69). Mount lifting lugs diagonally opposite.
10. Check pin (79) is installed in drum end cover (78).
11. Install motor reducer assembly. Ensure gear shaft (20) meshes with splined bore
in drum and secure with capscrews (86) and lockwashers (125).
12. Return winch to a horizontal position.
13. Install remaining external assemblies.
n
Automatic Band Drum Brake Assembly
Refer to Dwg. MHP2811. It is recommended that any brake cylinder service work be
conducted by an Ingersoll Rand trained technician.
1. Install ‘O’ ring (145) on the piston (146).
2. Install oil seal (114), ring (143) and ‘O’ ring (145) in the cover (117).
3. Install piston (146) and spring (144) in the housing (147).
Form MHD56305 Edition 4
11