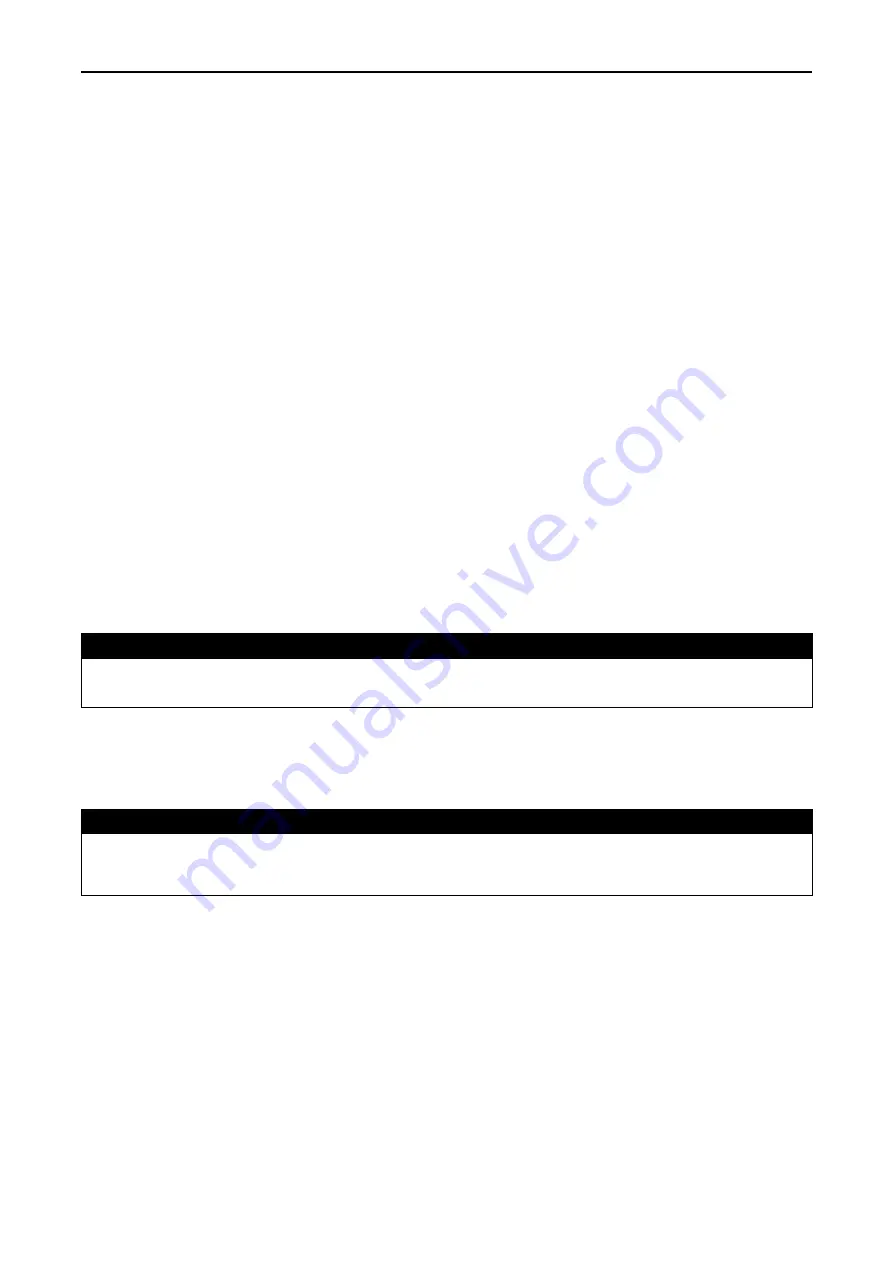
20
MHD56490
Daily Inspection
Complete inspections prior to start of daily tasks. Conduct visual inspections during regular operation for
indications of damage or evidence of malfunction (such as abnormal noises).
1.
Lubricator:
Adjust air line lubricator drops 2 to 3 per minute of ISO VG 32 (SAE 10W) oil during winch operation.
2.
Surrounding Area:
Visually check for winch oil leaks. Do not operate winch if leaking oil is found. Make sure the
surrounding area has no slippery surfaces and is obstruction free.
3.
Hoses and Fittings:
Visually inspect for damage, air leaks, and loose connections. Repair all leaks or damage
and tighten loose connections prior to starting daily tasks.
4.
Wire Rope Anchor:
Verify wire rope anchor is securely installed.
5.
Guards:
Verify wire rope does not contact drum guard during winch operation and that guards are secure and
undamaged.
6.
Winch:
Visually inspect winch housings, control(s), external brake, siderails, uprights and drum for damage.
Check that all external bolts are in place and secure. Report damage to supervisor and request additional
inspection by an
Ingersoll Rand
trained Service Technician.
7.
Mounting:
Visually inspect winch mounting bolts. Check bolts are tight, undamaged and free of corrosion.
8.
Winch Operation:
Power winch in both directions. Winch must operate smoothly without sticking, binding or
abnormal noises and have minimal vibration.
9.
Control Valve or Pendent:
Check operation is smooth and winch is responsive to control device movement.
Check control returns to neutral when released. If winch responds slowly or control sticks. Winch is to operate
without hesitation in both the payout and haul-in directions.
10.
Motor:
During operation check motor housing for excess heat build up. Housing should not be hot to touch.
Listen for grinding or knocking noises. If excess heat or noises are noted, do not operate until inspected by an
Ingersoll Rand
trained Technician.
11.
Wire Rope Spooling:
Visually check reeving and make sure the wire rope feeds on and off the drum smoothly.
Verify spooling direction is correct for winch and application.
12.
Brakes:
Lift and lower the load a short distance to test brakes. Brakes must hold load without slipping.
Automatic brake must release when winch control throttle is operated. If brakes do not hold load or do not
release properly, they must be adjusted or repaired.
W
WA
AR
RN
NIIN
NG
G
Brakes!
Worn or improperly functioning brakes may cause excessive heat buildup and sparks.
13.
Wire Rope:
Visually inspect all wire rope expected to be in use during the day’s operations. Inspect for wear and
damage indicated by distortion of wire rope such as kinking, “birdcaging”, core protrusion, main strand
displacement, corrosion, broken or cut strands. If damage is evident, do not operate winch until the
discrepancies have been reviewed and inspected further by personnel knowledgeable on wire rope safety and
maintenance procedures.
N
NO
OT
TIIC
CE
E
Periodic Inspection!
The full extent of wire rope wear cannot be determined by visual inspection. At any indication of
wear inspect wire rope in accordance with instructions in “Periodic Inspection”.
14.
Limit Switches:
Make sure the limit switches engage and prevent operation at the required set point and with
drum rotating in the correct direction. Make sure the limit switch properly resets.
15.
Emergency Stop and Reset Valve:
Activate emergency stop in payout and haul-in directions to ensure proper
operation. Valve must stop winch operation and brakes must set quickly. Reset valve after test.
16.
Slack Line Detection:
Operate winch in payout direction until slack line valve actuates. Ensure winch stops
operating in lowering direction, but can still lift load, after emergency stop reset.
17.
Emergency Lowering Device:
Check the pressure gauge located on the emergency lowering enclosure to ensure
tank has the proper psi supply of air. Do not operate the winch if there is no air supply in the tank.
18.
Press Roller:
Make sure the wire rope is positioned between press roller and drum barrel and springs keep press
roller in tight contact with wire rope. Make sure of smooth and proper operation.
19.
Labels and Tags:
Check for presence and legibility. Replace if necessary.