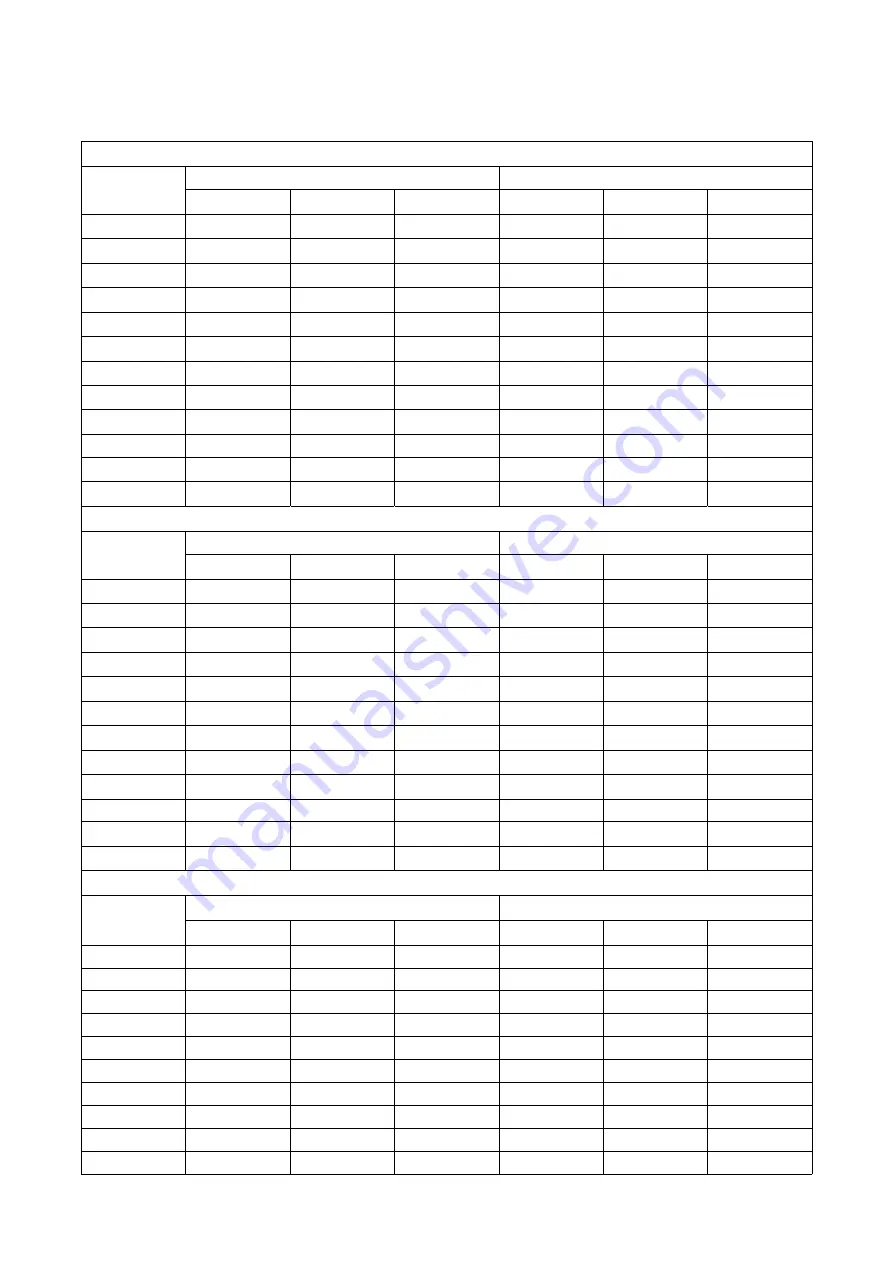
32
MHD56490
Torque Chart
Standard Coarse Thread Torque
Size
SAE Grade 5
SAE Grade 8
Dry
Lubricated
PTFE
Dry
Lubricated
PTFE
1/4-20
8-10
6-7
4
12-14
9-10
5-6
5/16-18
17-20
13-15
8-9
25-28
18-21
11-13
3/8-16
31-35
23-26
14-16
44-49
33-37
20-22
7/16-14
49-56
37-42
22-25
70-79
52-59
31-36
1/2-13
75-85
57-64
34-38
106-121
80-90
48-54
9/16-12
109-123
82-92
49-55
154-174
115-130
69-78
5/8-11
150-170
113-128
68-77
212-240
159-180
95-108
3/4-10
267-302
200-227
120-136
376-426
282-320
169-192
7/8-9
429-487
322-365
193-219
606-687
455-515
273-309
1-8
644-729
483-547
290-328
909-1030
681-772
409-463
1 1/8-7
794-900
596-675
357-405
1288-1460
966-1095
580-657
1 1/4-7
1121-1270
840-952
504-571
1817-2059
1363-1545
818-927
Standard Fine Thread Torque
Size
SAE Grade 5
SAE Grade 8
Dry
Lubricated
PTFE
Dry
Lubricated
PTFE
1/4-20
10-11
7-8
4-5
14-15
10-12
6-7
5/16-24
19-22
14-16
9-10
27-31
20-23
12-14
3/8-24
35-40
26-30
16-18
49-56
37-42
22-25
7/16-20
55-63
41-47
25-28
78-88
58-66
35-40
1/2-20
85-96
64-72
38-43
120-136
90-102
54-61
9/16-18
121-137
91-103
55-62
171-194
128-146
77-87
5/8-18
170-193
127-144
76-87
240-272
180-204
108-122
3/4-16
297-337
223-253
134-152
420-476
315-357
189-214
7/8-14
474-537
355-403
213-242
669-758
502-568
301-341
1-12
704-798
528-599
317-359
995-1127
746-845
448-507
1 1/8-12
1023-1159
767-869
460-572
1444-1637
1083-1227
650-736
1 1/4-12
1425-1615
1069-1211
641-727
2012-2280
1509-1710
905-1026
Metric Coarse Thread Torque
Size
Class 8.8 / 9.8
Class 10.9
Dry
Lubricated
PTFE
Dry
Lubricated
PTFE
M6x1
9-10
6-7
4
11-12
8-9
5-6
M8x1.25
21-23
16-18
9-11
26-30
20-22
12-13
M10x1.5
41-47
31-35
19-21
53-60
39-45
24-27
M12x1.75
71-81
54-61
32-36
91-103
68-77
41-46
M14x2
115-130
86-98
52-59
147-166
110-125
66-75
M16x2
165-187
124-140
74-84
227-257
170-193
102-116
M20x2.5
321-364
241-273
144-164
443-502
332-376
199-226
M22x2.5
439-497
329-373
197-224
605-686
454-514
272-309
M24x3
556-630
417-473
250-284
767-869
575-652
345-391
M30x3.5
1103-1250
827-938
496-563
1521-1724
1141-1293
685-776