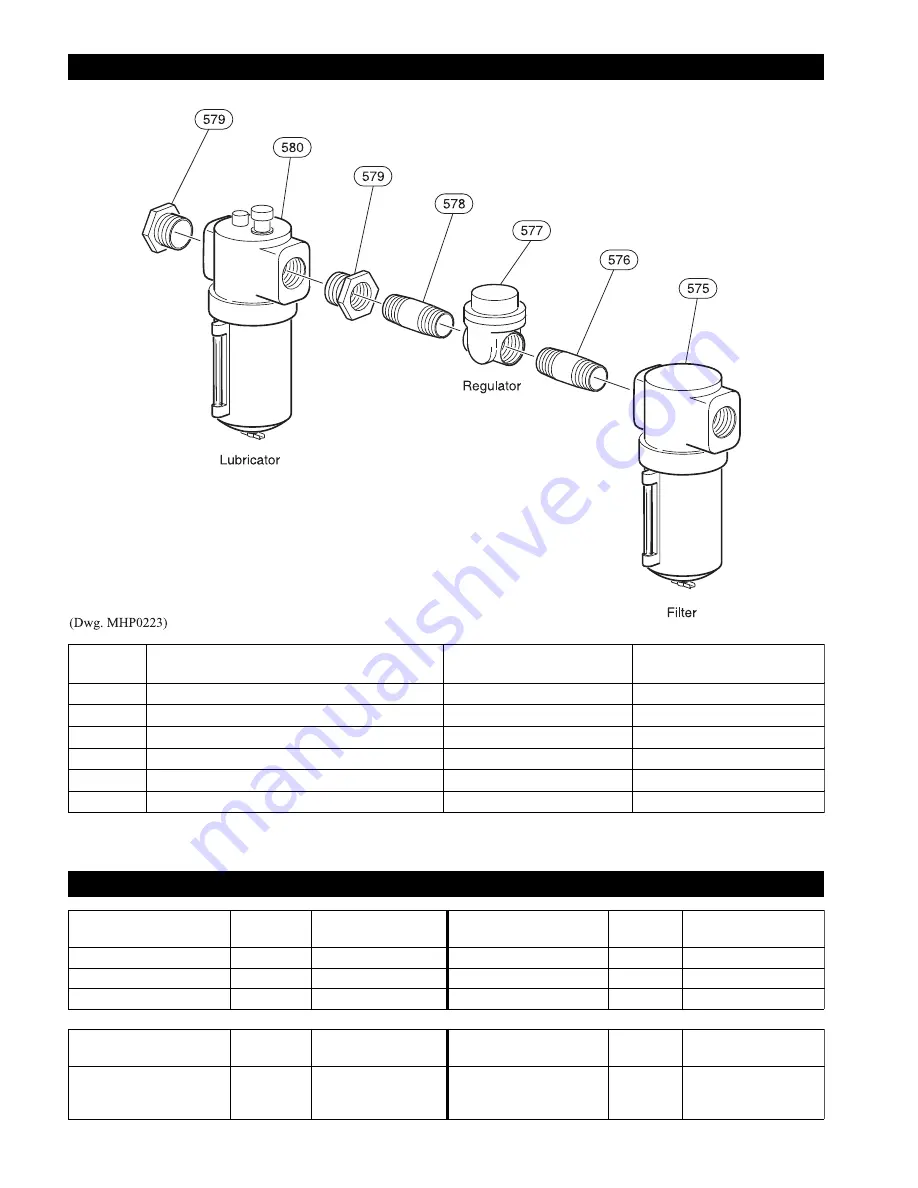
62
AIR PREPARATION ASSEMBLY PARTS DRAWING AND PARTS LIST
DESCRIPTION
OF ACCESSORY
QTY
TOTAL
PART
NUMBER
DESCRIPTION
OF ACCESSORY
QTY
TOTAL
PART
NUMBER
Thermoplastic Powder
2 ounce
71308902
Yellow Touch-Up Paint
1 can
FAP-237Y
Propane Torch
1 each
71308886
Lubricant
16 fl. oz.
LUBRI-LINK-GREEN
Heat Gun
1 each
71308894
Infra-red Thermometer
1
71308878
DESCRIPTION
OF KIT
QTY
TOTAL
PART
NUMBER
DESCRIPTION
OF KIT
QTY
TOTAL
PART
NUMBER
Adapter Rail Kit for FA5A
Short Drum to K6U Foot
Print
1
24333
Adapter Rail Kit for FA5A
Long Drum to K6U Foot
Print
1
24332
ITEM
NUMBER
DESCRIPTION
OF PART
QUANTITY
TOTAL
PART
NUMBER
575
Filter
1
F42-0B-000
576
Pipe Nipple
1
51670
577
Regulator
1
R30-0B-G00
578
Pipe Nipple
3
51704
579
Pipe Bushing
2
Contact factory
580
Lubricator
1
L40-0B-G00
*
Air preparation components for 1-1/2 inch NPT system. Items 578 and 579 depend on required size for customer application.
ACCESSORIES AND KITS
Summary of Contents for ManRider force5 FA5AMR-LAK1
Page 39: ...39 WINCH CROSS SECTION DRAWING ...
Page 40: ...40 WINCH ASSEMBLY PARTS DRAWING ...
Page 42: ...42 MOTOR ASSEMBLY PARTS DRAWING ...
Page 44: ...44 DISC BRAKE ASSEMBLY PARTS DRAWING ...
Page 48: ...48 LEVER OPERATED CONTROL VALVE ASSEMBLY PARTS DRAWING ...
Page 50: ...50 PENDANT OPERATED PILOT CONTROL VALVE ASSEMBLY PARTS DRAWING ...
Page 52: ...52 REMOTE PENDANT ASSEMBLY PARTS DRAWING ...
Page 54: ...54 SHUTTLE VALVE ASSEMBLY PARTS DRAWING ...
Page 56: ...56 EMERGENCY STOP AND OVERLOAD ASSEMBLY PARTS DRAWING ...
Page 64: ...64 SERVICE NOTES ...
Page 65: ...65 SERVICE NOTES ...