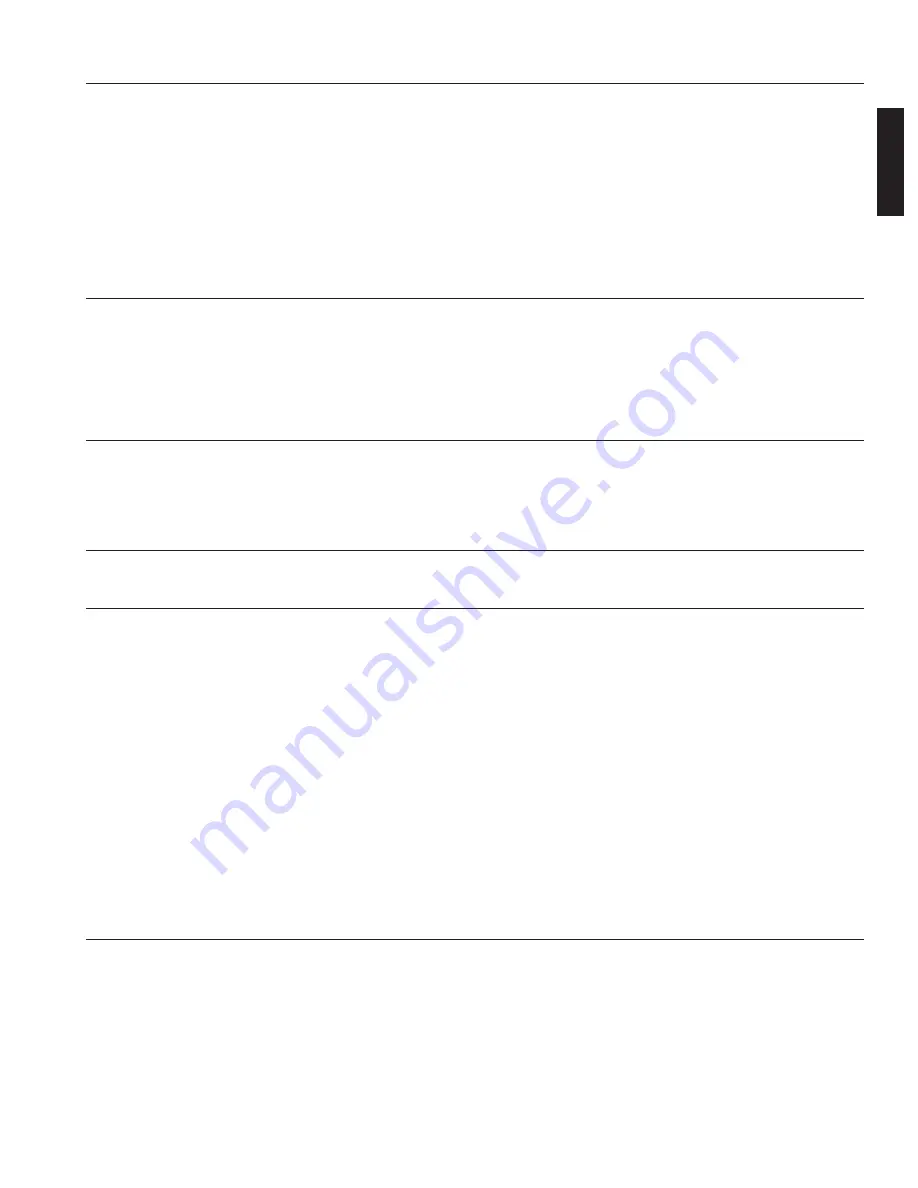
PROBLEM
POSSIBLE CAUSE
POSSIBLE SOLUTION
High oil consumption
1. Clogged or dirty inlet and/or discharge line filter.
2. Lubricant viscosity too low.
3. Detergent type lubricant being used.
4. Piston rings damaged or worn (broken, rough or scratched).
Excessive end gap or side clearance.
5. Piston rings not seated, are stuck in grooves or end gaps not
staggered.
6. Cylinder(s) or piston(s) scratched, worn or scored.
7. Connecting rod, piston pin or crankpin bearings worn or scored.
8. Crankshaft seal worn or crankshaft scored.
9. Worn cylinder finish.
1. Clean or replace.
2. Drain existing lubricant and refill with proper lubricant.
3. Drain existing lubricant and refill with proper lubricant.
4. Install ring kit.
5. Adjust piston rings.
6. Repair or replace as required.
7. Inspect all. Repair or replace as required.
8. Replace seal or crankshaft assembly.
9. Deglaze cylinder with 180 grit flex-hone.
Knocking or rattling
1. Loose beltwheel or motor pulley, excessive end play in motor
shaft or loose drive belts.
2. Compressor valves leaky, broken, carbonized or loose.
3. Carbon build-up on top of piston(s).
4. Cylinder(s) or piston(s) scratched, worn or scored.
5. Connecting rod, piston pin or crankpin bearings worn or scored.
6. Defective ball bearings on crankshaft or motor shaft.
1. Check beltwheel, motor pulley, crankshaft, drive belt tension
and alignment. Repair or replace as required.
2. Inspect valves. Clean or replace as required.
Install valve kit.
3. Clean piston(s). Repair or replace as required.
4. Repair or replace as required.
5. Inspect all. Repair or replace as required.
6. Inspect bearings and replace crankshaft assembly if required.
Lights flicker or dim when
running
1. Improper line voltage.
2. Wiring or electric service panel too small.
3. Poor contact on motor terminals or starter connections.
4. Improper starter overload heaters.
5. Poor power regulation (unbalanced line).
1. Check line voltage and upgrade lines as required. Contact
electrician.
2. Install properly sized wire or service box. Contact electrician.
3. Ensure good contact on motor terminals or starter connections.
4. Install proper starter overload heaters. Contact electrician.
5. Contact power company.
Moisture in crankcase or “milky”
appearance in petroleum
lubricant or rusting in cylinders
1. Detergent type lubricant being used.
2. Extremely light duty cycles.
3. Unit located in damp or humid location.
1. Drain existing lubricant and refill with proper lubricant.
2. Run unit for longer duty cycles.
3. Relocate unit.
Motor overload trips or draws
excessive current
1. Lubricant viscosity too high.
2. Improper line voltage.
3. Wiring or electric service panel too small.
4. Poor contact on motor terminals or starter connections.
5. Improper starter overload heaters.
6. Poor power regulation (unbalanced line).
7. Drive belts too tight or misaligned.
8. Compressor valves leaky, broken, carbonized or loose.
9. Cylinder(s) or piston(s) scratched, worn or scored.
10. Connecting rod, piston pin or crankpin bearings worn or scored.
11. Defective ball bearings on crankshaft or motor shaft.
12. Leaking check valve or check valve seat blown out.
13. Ambient temperature too low.
14. Bad motor.
1. Drain existing lubricant and refill with proper lubricant.
2. Check line voltage and upgrade lines as required. Contact
electrician.
3. Install properly sized wire or service box. Contact electrician.
4. Ensure good contact on motor terminals or starter connections.
5. Install proper starter overload heaters. Contact electrician.
6. Contact power company.
7. Adjust belts to proper tension and alignment.
8. Inspect valves. Clean or replace as required.
Install valve kit.
9. Repair or replace as required.
10. Inspect all. Repair or replace as required.
11. Inspect bearings and replace crankshaft assembly if required.
12. Replace check valve.
13. Relocate unit to warmer environment.
Install crankcase heater kit.
Convert to synthetic lubricant.
14. Replace
Motor will not start
1. Improper line voltage.
2. Wiring or electric service panel too small.
3. Poor contact on motor terminals or starter connections.
4. Improper starter overload heaters.
5. Bad motor.
1. Check line voltage and upgrade lines as required. Contact
electrician.
2. Install properly sized wire or service box. Contact electrician.
3. Ensure good contact on motor terminals or starter connections.
4. Install proper starter overload heaters. Contact electrician.
5. Replace
3FW&
11
EN
RELEASED 31/Jan/2020 19:25:50 GMT
Summary of Contents for SS4L5
Page 4: ...4 3FW EN General Arrangement INSTALLATION RELEASED 31 Jan 2020 19 25 50 GMT...
Page 14: ...3FW 41 NOTES RELEASED 31 Jan 2020 19 25 50 GMT...
Page 15: ...42 3FW NOTES RELEASED 31 Jan 2020 19 25 50 GMT...
Page 16: ...3FW 43 NOTES RELEASED 31 Jan 2020 19 25 50 GMT...
Page 17: ...ingersollrandproducts com 20 Ingersoll Rand RELEASED 31 Jan 2020 19 25 50 GMT...