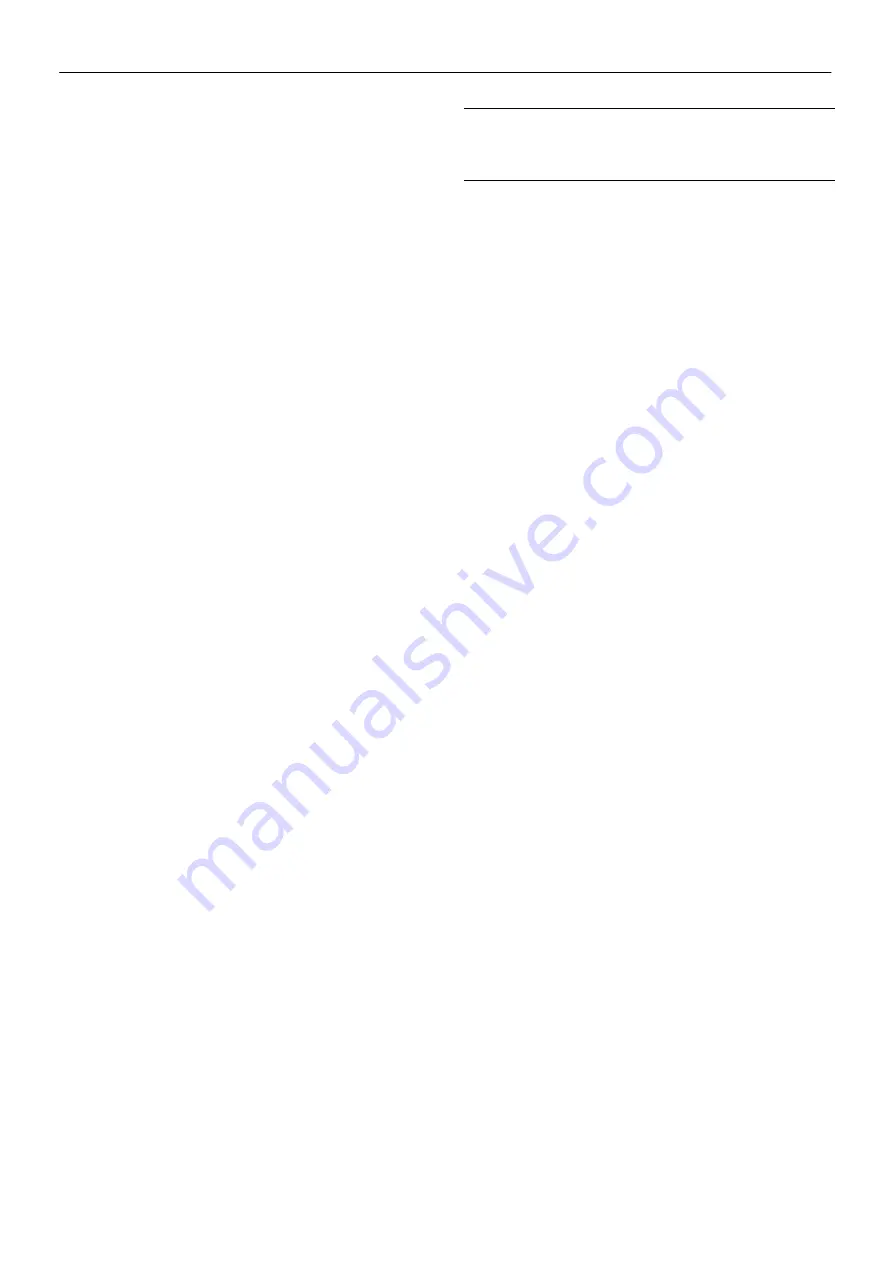
MAINTENANCE
24
M4 M5,5 M7,5 M11
BELT TENSION
This unit has been designed with a unique self tensioning system,
therefore, the drive belt requires no manual adjustment. Use only
genuine Ingersoll–Rand replacement parts to ensure the correct belt
tension.
AIREND BEARINGS
Airend bearings are lubricated by the compressor coolant and
require no maintenance.
MOTOR BEARINGS
Motor bearings are sealed for life and require no maintenance.
Summary of Contents for SSR M11
Page 15: ...GENERAL INFORMATION 13 M4 M5 5 M7 5 M11 ...
Page 34: ......
Page 35: ......
Page 36: ...Printed in the United Kingdom ...