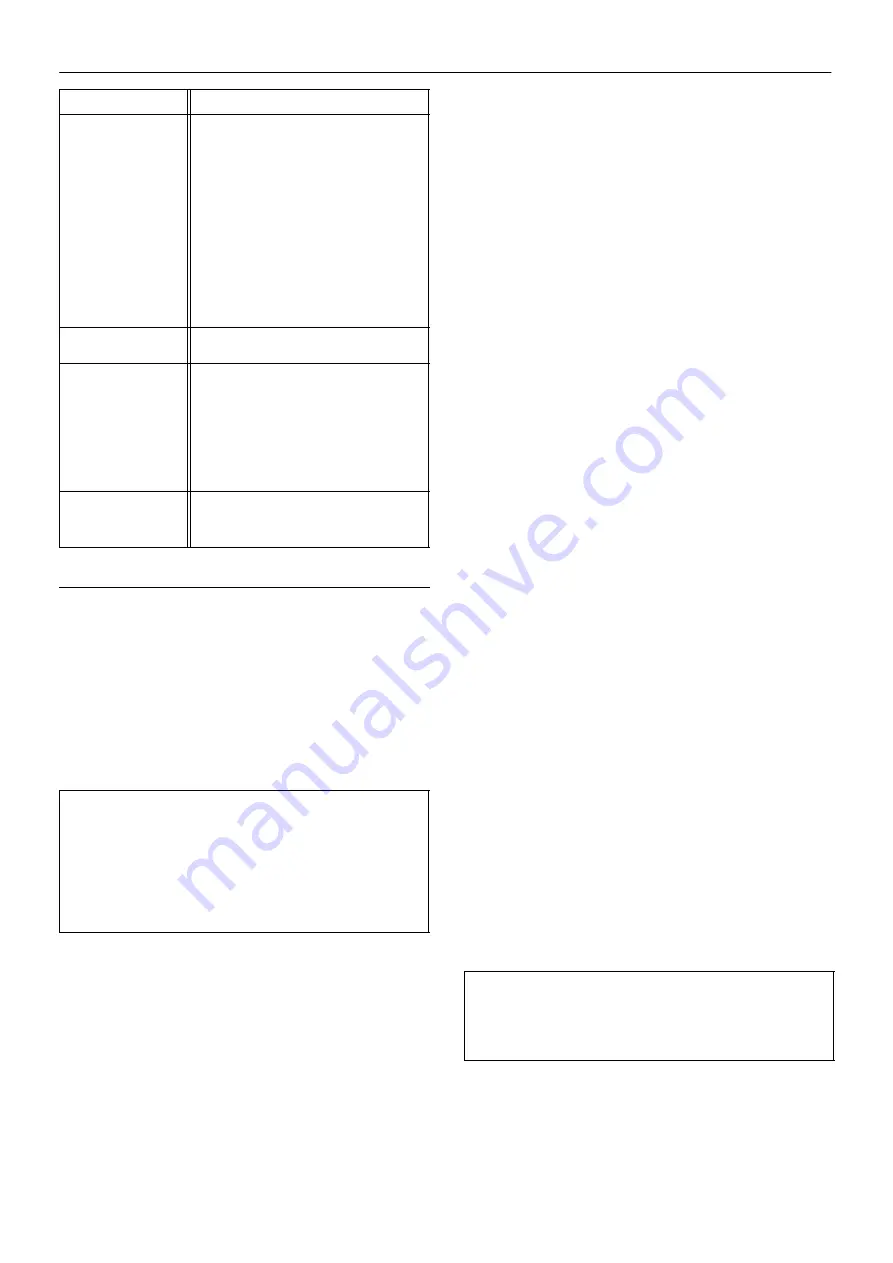
MAINTENANCE
19
UP6RD–5–175, UP6RM–5–175, UP6RD–5–175
PERIOD
MAINTENANCE
Daily or Before Each
Operation
S
Check oil level. Fill as needed.
Operation
S
Drain receiver tank condensate. Open
the manual drain valve and collect and
dispose of condensate accordingly.
S
Test drain valve for proper operation.
Clean if needed
S
Check for unusual noise and vibration.
S
Ensure beltguards and covers are
securely in place.
S
Ensure area around compressor is free
from rags, tools, debris, and flammable or
explosive materials.
Weekly
S
Inspect air filter element(s). Clean or
replace if necessary.
Monthly
S
Inspect for air leaks. Squirt soapy water
around joints during compressor operation
and watch for bubbles.
S
Check tightness of screws and bolts.
Tighten as needed.
S
Clean drain valve
S
Clean exterior.
Each 2000 Hours /
1 year
S
Change synthetic oil while crankcase is
warm.
S
Replace filter element(s).
ROUTINE MAINTENANCE
This section refers to the various components which require
periodic maintenance and replacement.
The SERVICE/MAINTENANCE CHART indicates the various
components’ descriptions and the intervals when maintenance has to
take place. Oil capacities, etc., can be found in the GENERAL
INFORMATION section of this manual.
Compressed air can be dangerous if incorrectly handled. Before
doing any work on the unit, ensure that all pressure is vented from the
system and that the machine cannot be started accidentally.
CAUTION
Before beginning any work on the compressor, open, lock and tag
the main electrical disconnect and close the isolation valve on the
compressor discharge. Vent pressure from the unit by slowly
unscrewing the coolant fill cap one turn. Unscrewing the fill cap opens
a vent hole, drilled in the cap, allowing pressure to release to
atmosphere. Do not remove the fill cap until all pressure has vented
from the unit. Also vent piping by slightly opening the drain valve. When
opening the drain valve or the coolant fill cap, stand clear of the valve
discharge and wear appropriate eye protection.
Compressed air can be dangerous if incorrectly handled. Before
doing any work on the unit, ensure that all pressure is vented from the
system and that the machine cannot be started accidentally.
Ensure that maintenance personnel are adequately trained,
competent and have read the Maintenance Manuals.
Prior to attempting any maintenance work, ensure that:–
.
all air pressure is fully discharged and isolated from the system. If
the automatic blowdown valve is used for this purpose, then allow
enough time for it to complete the operation.
.
the machine cannot be started accidentally or otherwise, by posting
warning signs and/or fitting appropriate anti–start devices.
.
all residual electrical power sources (mains and battery) are
isolated.
Prior to opening or removing panels or covers to work inside
a machine, ensure that:–
.
anyone entering the machine is aware of the reduced level of
protection and the additional hazards, including hot surfaces and
intermittently moving parts.
.
the machine cannot be started accidentally or otherwise, by posting
warning signs and/or fitting appropriate anti–start devices.
Prior to attempting any maintenance work on a running
machine, ensure that:–
.
the work carried out is limited to only those tasks which require the
machine to run.
.
the work carried out with safety protection devices disabled or
removed is limited to only those tasks which require the machine to be
running with safety protection devices disabled or removed.
.
all hazards present are known (e.g. pressurized components,
electrically live components, removed panels, covers and guards,
extreme temperatures, inflow and outflow of air, intermittently moving
parts, safety valve discharge etc.).
.
appropriate personal protective equipment is worn.
.
loose clothing, jewelry, long hair etc. is made safe.
.
warning signs indicating that Maintenance Work is in Progress are
posted in a position that can be clearly seen.
Upon completion of maintenance tasks and prior to returning
the machine into service, ensure that:–
.
the machine is suitably tested.
.
all guards and safety protection devices are refitted.
.
all panels are replaced, canopy and doors closed.
.
hazardous materials are effectively contained and disposed of.
WARNING
Do not under any circumstances open any drain valve or remove
components from the compressor without first ensuring that the
compressor is FULLY SHUT– DOWN, power isolated and all air
pressure relieved from the system.
Summary of Contents for UP6RD-5-175
Page 2: ......