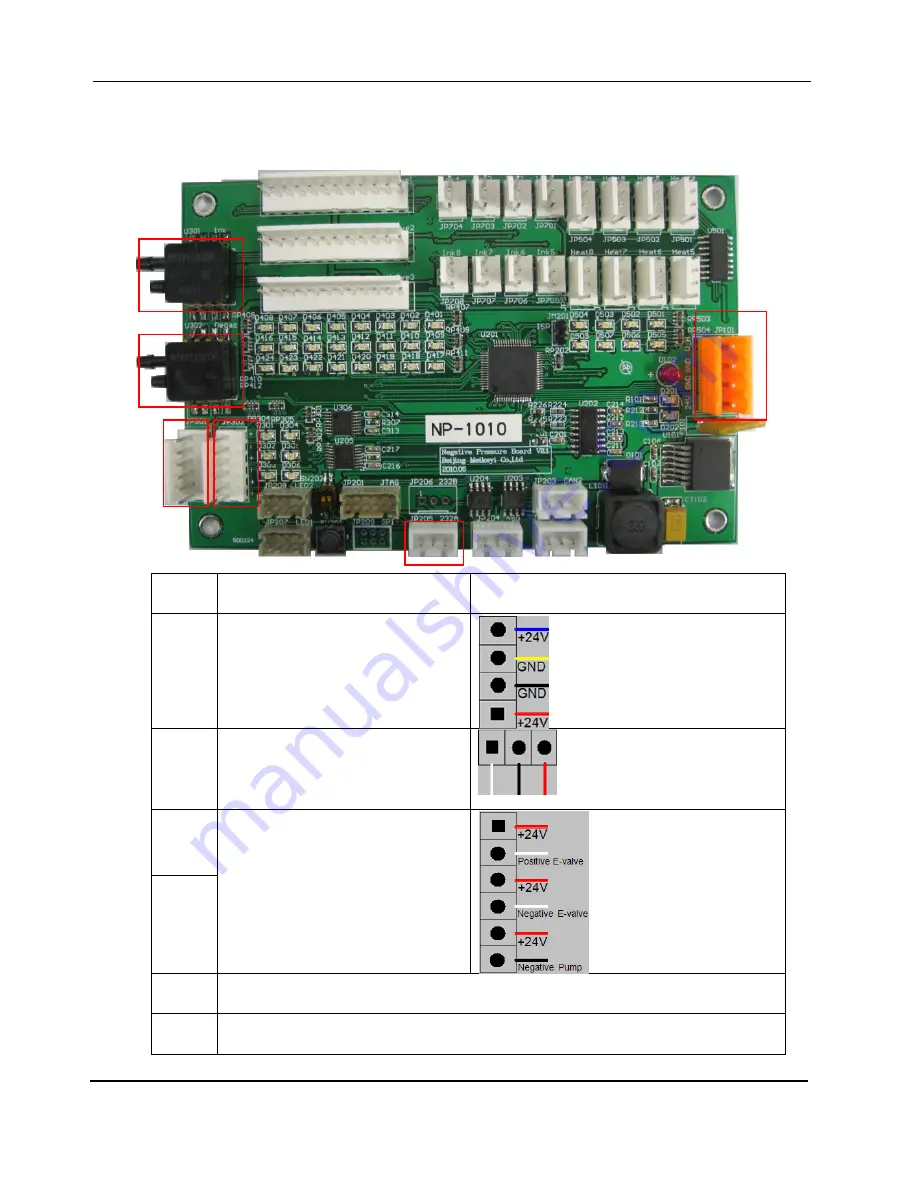
2
‐
3
‐
7
N
EGATIVE
P
RESSURE
C
ONTROL
B
OARD
Negative pressure board controls the negative pressure system, which is important for high-speed printing.
Slot Connection
Note
JP101 Power
supply
JP205
To socket Panel of IS Main Board
JP301
(KCMY)
Pin 1, 3, 5: +24V
Pin 2: to positive 3-way EM valve
Pin 4: to negative 3-way EM valve
Pin 6: to negative pump
JP302
(White)
U301
Negative pressure sensor of Meniscus system of KCMY
U302
Negative pressure sensor of Meniscus system of white ink
JP101
JP301
JP302
U301
U302
JP205
INKCUPS NOW SERIES INKJET PRINTERS
XJET
All rights reserved by Inkcups Now Corporation
Rev: SC71112
Page 27 of 100