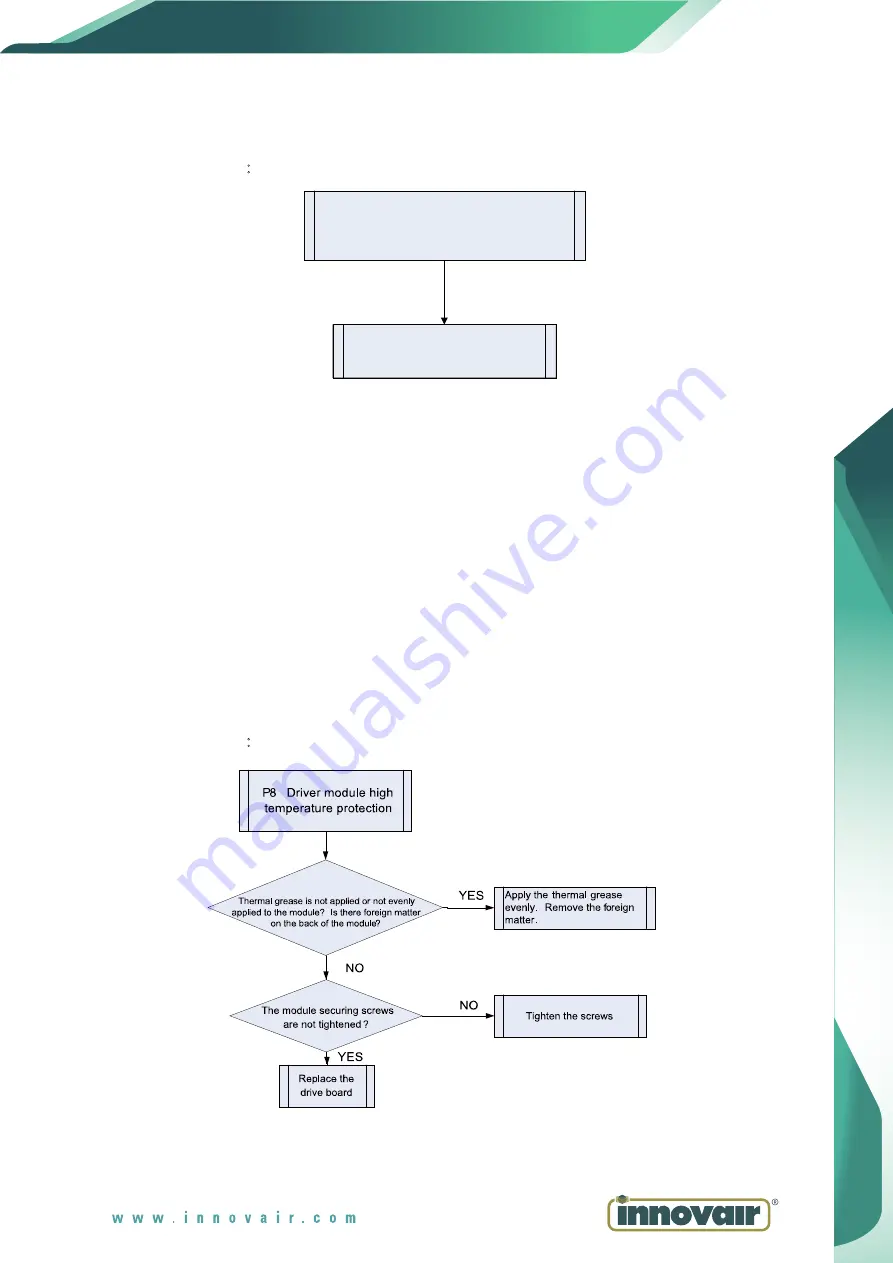
46
SERVICE MANUAL
Troubleshooting
:
P7
Driver module sensor error
Replace the drive board
3.4.19 “P8” Driver Module High Temperature Protection
Error display:
ODU mainboard LED displayer
Error judgment condition and method:
If IPM module temperature or PFC module temperature exceeds the set protection value, then it can be
judged that driver module temperature is too high and system will shut down for protection.
Possible reason:
Thermal grease is not applied or not evenly applied to the module, or there is other substance on the back of the
module.
The module securing screws are not tightened up.
Drive board temperature sampling circuit element is damaged or drive chip temperature sampling AD terminal is
abnormal.
Troubleshooting
:
Summary of Contents for Inverter FLEX24 DEV24H2R18
Page 9: ...6 SERVICE MANUAL 2 Control 2 1 Operation Mode 2 1 1 Cooling Mode ...
Page 10: ...2 1 2 Heating Mode SERVICE MANUAL 7 ...
Page 19: ...Model DEV48H2R18 DEV60H2R18 16 SERVICE MANUAL ...
Page 27: ...SEV2040H2R18 SEV4060H2R18 24 SERVICE MANUAL ...