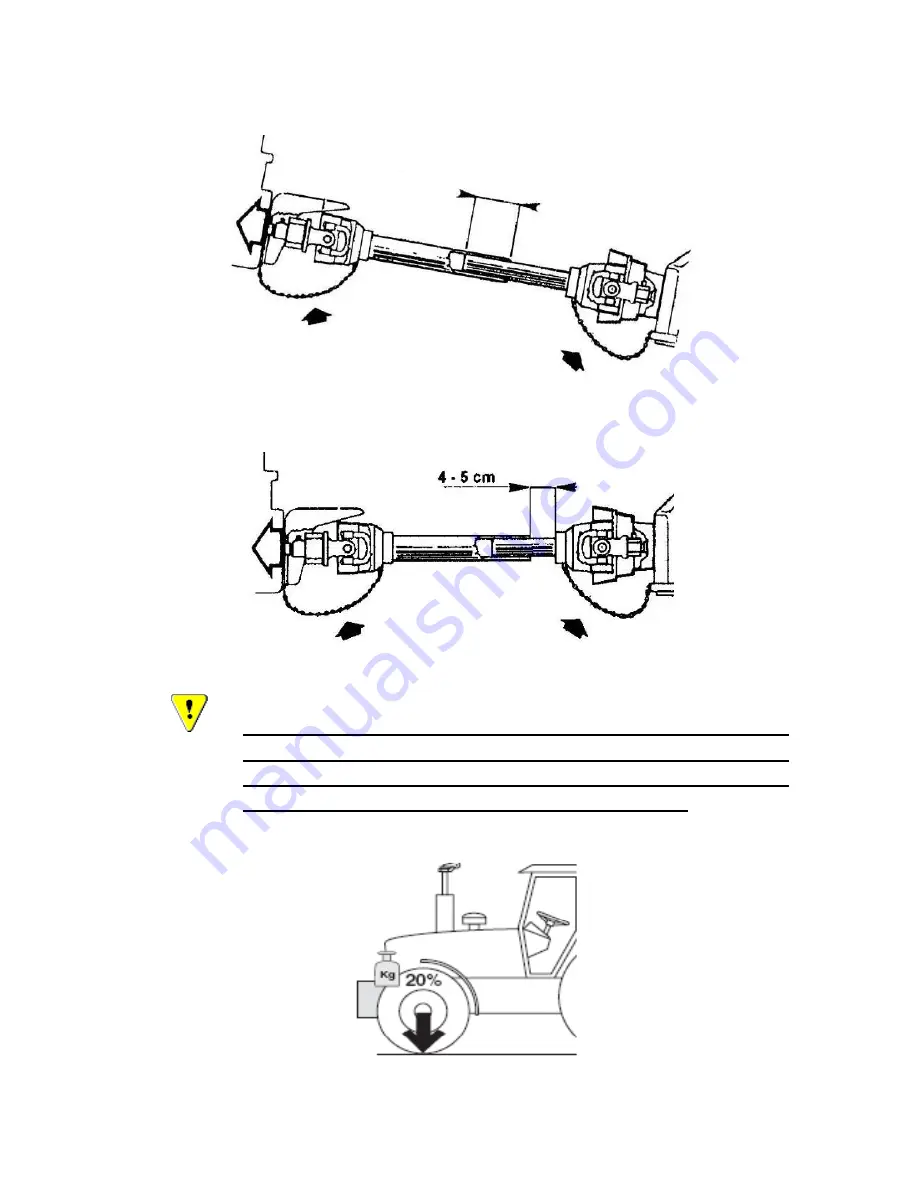
19
Fig. 8: Appropriate length of PTO shaft at the machine on the ground
Fig.9: Appropriate length of the guard at machine lifted.
5.4 Tractor stability
At attachment of the machine on the tractor always take
care about allowed weight of the attachment and axle
load. First axle of the tractor should always be loaded
with min.20% of the weight of the tractor itself.
Fig. 10
1/3 cevi
Summary of Contents for EURO MINI
Page 32: ...32 ...