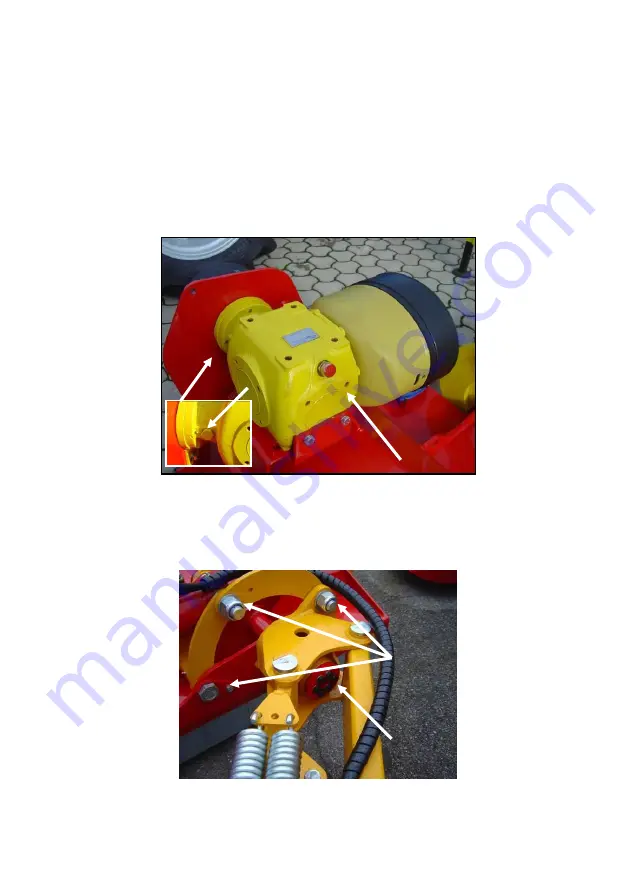
31
9.2. Oil level control
Use always the same type of oil, SAE 90. For gearbox we need cca 2 l of
oil.Use the hole on the top of gearbox for filling in
(Fig. 31/1)
. For
pouring in use a funnel.
Pour in the oil till the level of the control plug on
the gearbox
(Fig.31/1).
A plug for oil control is placed on the rear side of
the gearbox (Fig.31/2).
Slika št. 31
9.3. Control of bolts
Fig. 32
Take special care that the bolts (Fig.32/1) are tightened well!
1
2
1
Summary of Contents for MKM
Page 33: ...33 Fig 33 Fig 34 Fig 37 Fig 38 1 Fig 34 6 Fig 35 Fig 36 Fig 38 2 5 9 4 10 7 8 3 1 2 ...
Page 38: ...38 A ...
Page 39: ...39 B ...