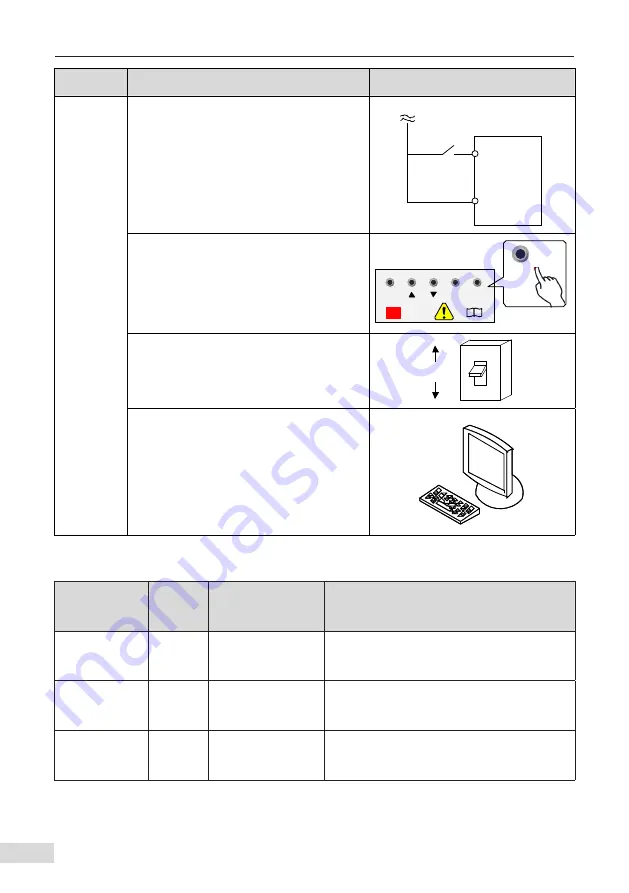
6 Troubleshooting
- 72 -
Stage
Solution
Remarks
Fault
resetting
method
1) Allocate a DI terminal with function 9
"Fault reset (RESET)" by setting any of F4-
00 (DI1 function selection) to F4-04 (DIO2
function selection) to 9 (Fault reset).
DI
COM
Fault
reset
Drive
2)
Press the ENTER key on the operating
panel.
SHIFT
MODE
ENTER
CHARGE
i
ENTER
3)
Automatic resetting
Disconnect the main circuit power supply.
Wait until the fault code disappears, and
connect the power supply again.
ON
OFF
4) Fault resetting using the host controller
Confirm that F0-02 (Command source
selection) is set to 2 (Communication control)
and write "7" (fault reset) to communication
address 2000H. [1]
Host
computer
6.2 Fault Codes and Solutions
Fault Name
Operating
Panel
Display
Cause
Possible Solution
Abnormal
current
sampling
E 01.01
The current
sampling circuit is
faulty.
Check whether mains power supply is on.
Contact the agent or Inovance.
Product model
setup error
E 01.05
Product model and
hardware do not
match.
Check whether the equipment model is wrong.
STO product
model setup
error
E 01.06
Product hardware
does not support
STO.
Check whether there is no STO product model,
and contact the manufacturer if so.