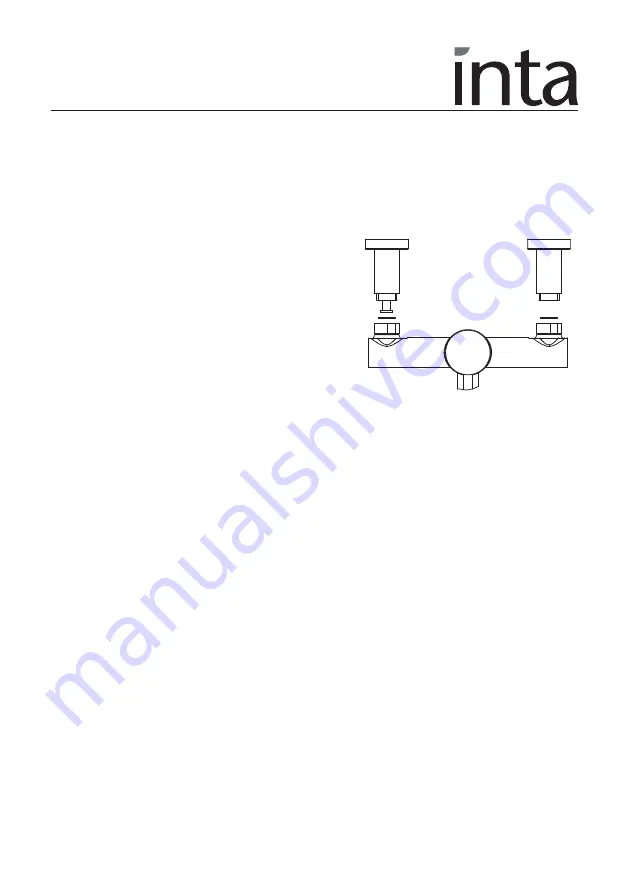
© Intatec Ltd 2016
8
Installation
Wall Mounting
• The tap is supplied as shown in the Components section except that the thermostatic cartridge
(2) and swivel nut connectors (9) are fitted into the body.
• Fit the concealing plates (5) onto the tailpieces (6) & (7).
• Screw the tailpiece (6) into the cold water inlet of
the tap, right hand side when facing the tap.
ATTENTION: The hot water inlet connection tail
can be identified by the brass insulator pipe that
protrudes past the connecting thread.
Care must be taken to ensure the Hot Water Inlet
Tail Assembly is connected securely into the hot
water inlet of the tap body.
• Screw the tailpiece (7) into the hot water inlet of
the tap, left hand side when facing the tap.
• For wall mounting fit the tap assembly to the
mounting panel, using the back nuts (15) and slide
the concealing plates to the panel.
• Care should be taken that the maximum panel thickness does not exceed 33mm..
• Connect the supply pipes to the tap, cold on the right, hot on the left.
• Fit the lever (3) to the tap using the grub screw (4) provided.
• Please ensure that the hydraulic installation is completed and that all check valves are open.
Deck Mounting
• Screw the tailpiece (6) into the cold water inlet of the tap, right hand side when facing the
tap.
ATTENTION: The hot water inlet connection tail can be identified by the brass
insulator pipe that protrudes past the connecting thread. Care must be taken to ensure the
Hot Water Inlet Tail Assembly is connected securely into the hot water inlet of the tap
body.
• Screw the tailpiece (7) into the hot water inlet of the tap, left hand side when facing the tap.
• For deck mounting fit the tap assembly to the basin, using the washers (16) and back nuts
(15) (supplied) and slide the concealing plates to the basin.
• Connect the supply pipes to the tap, cold on the right, hot on the left.
• Fit the lever (3) to the tap using the grub screw (4) provided.
• Please ensure that the hydraulic installation is completed and that all isolation valves are in
the open position.
Cold water
inlet tail
Sealing
washer
6
Hot water
inlet tail
7
Summary of Contents for HTMDMCP
Page 23: ...Intatec Ltd 2016 22 Notes...