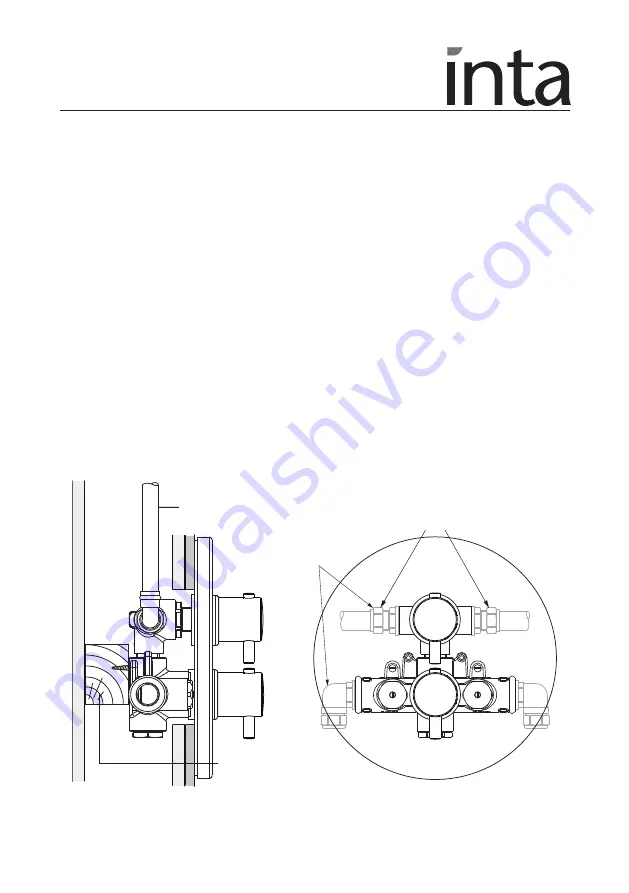
© Intatec Ltd 2017
12
Fitting the Concealing Plate
• If there is access from the adjacent room into the cavity, the surface of the shower room wall
can be finished with most of the tiling completed.
• Connect the copper supply pipework ensuring a water tight joint.
• Insert the assembly through the wall, secure the pipework and connect to the shower valve.
• Once the wall elbow and soaker have been connected turn on the water supplies and test all
joints for leakage before finishing the wall. Any leaking joints must be rectified before
proceeding further.
• Finish tiling the wall around the shower valve.
• Fit the gasket into the concealing plate with a bead of mastic.
• Place the concealing plate and gasket, with a bead of mastic on the back of both, over the
control valves and press firmly to the wall.
• Fit the temperature stop ring, the gear drive and push on the temperature control knobs.
• Finally finish the wall on the adjacent room side.
• See installation details for the various outlet and shower combinations.
Compression
Fittings
Connections to Overhead
Soaker and Wall Elbow
Valve fixed securely
using 2 screws to
structural member of stud wall
Outlet pipes to
wall elbow and
overhead soaker
Typical arrangement
for a studded wall
Summary of Contents for Kiko DELUXE KIKOD20
Page 27: ...Intatec Ltd 2017 26 Notes...
Page 28: ...Intatec Ltd 2017 27 Notes...
Page 29: ...Intatec Ltd 2017 28 Notes...