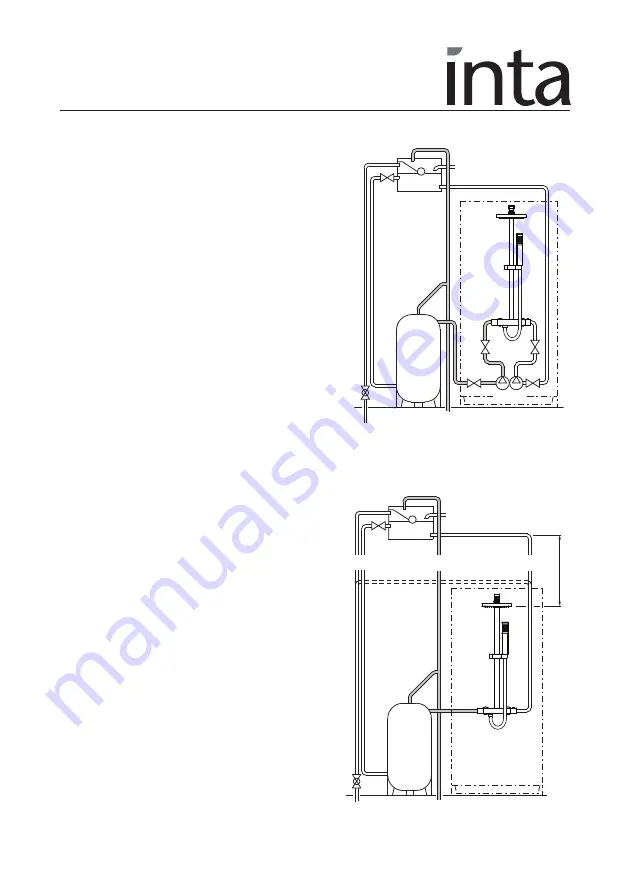
© Intatec Ltd 2017
4
Pumped Systems
Pumped systems use a booster pump to increase the
pressure of the gravity fed water supplies.
These booster pumps are used where the head of
water is insufficient to provide a satisfactory shower
or where a high performance shower is required.
Please ensure that the performance of the pump is
matched to suit the shower.
Follow the instructions for gravity fed installations
taking into account the installation requirements of
the pump.
Ensure that the hot and cold water storage capacity
is sufficient to supply the shower and any other
draw off points that may be used simultaneously.
Most pumps require a minimum head of water to
allow the flow switches to operate automatically.
Where this is not available a negative head kit
may be required to operate the pump.
Please consult the pump manufacturer’s installation requirements
Gravity System
The drawing shows a typical installation of a
shower valve on a gravity supplied system.
Please note the minimum head pressure required
to ensure correct operation of the valve. In
accordance with good plumbing practice, we
recommend that a totally independent hot and
cold water supply be taken to the valve.
The cold water supply must be connected directly
to the water cistern. The hot water supply should
be connected to the hot water cylinder via an
Essex flange or Sussex flange or to the vent or a
draw off pipe as close as possible to the top of
the cylinder.
For equal tank fed pressures there is no need to
fit the flow regulators. This installation is the
recommended minimum for gravity supplies. For
systems with less than 4 metre head pressure,
we recommend that a suitable booster pump is
fitted to increase the supply pressure.
Cold Supply direct
from mains
Pumps
Option shown
for mains
pressure cold
& low pressure
hot water
Min. 4m head
Summary of Contents for Nulo CB10032CP
Page 21: ...Intatec Ltd 2017 20 Notes...
Page 22: ...Intatec Ltd 2017 21 Notes...
Page 23: ...Intatec Ltd 2017 22 Notes...