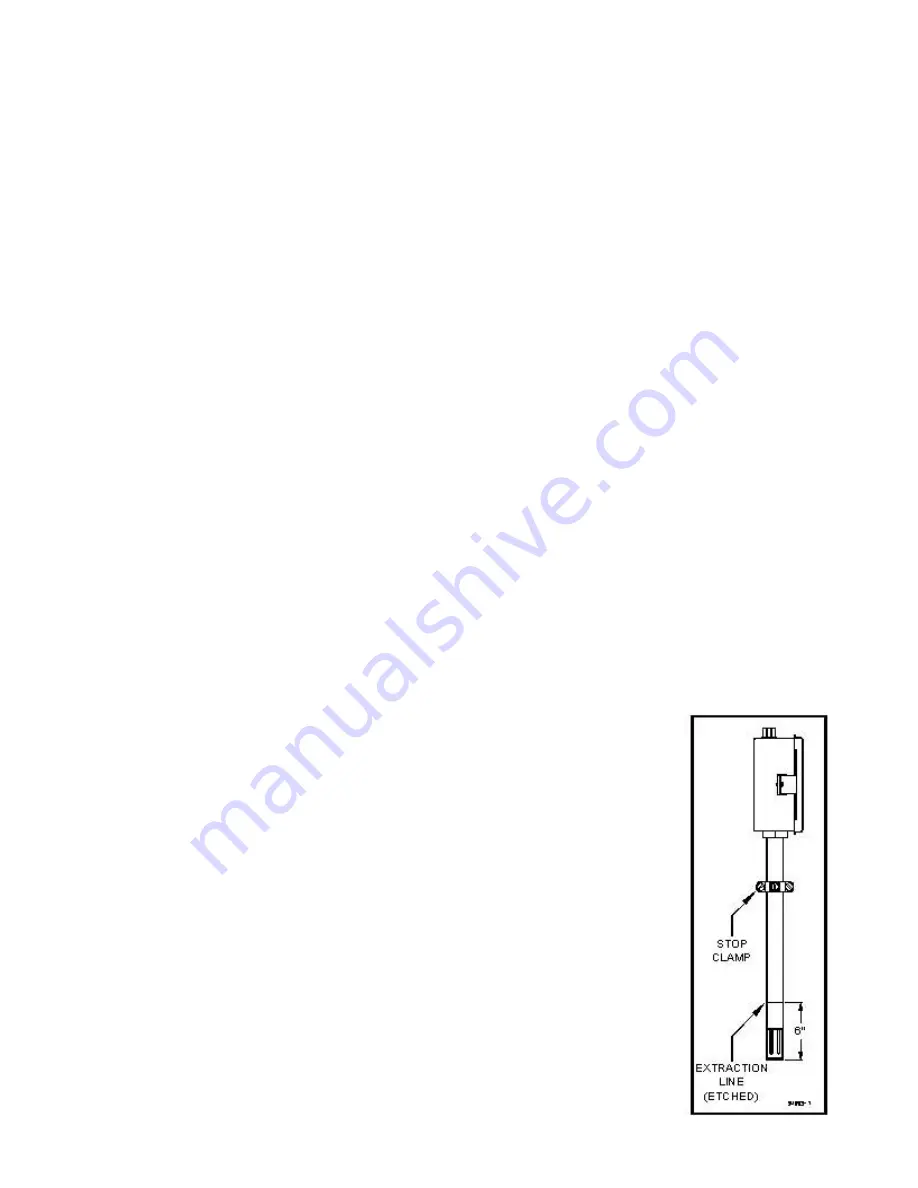
- 7 -
Figure 3
Transducer
Stop Clamp
These instructions cover installation of the
RheoVac
probes and
SENTRY
CPU in its standard
configuration. Additional information pertaining to your unit is covered in
SECTION 6 — CUSTOM
INFORMATION
. Carefully read these instructions prior to installing the equipment.
2.3 HOT TAP INSTALLATION
Î
Check installation configuration. Make sure the probe is parallel to the floor (see Figure 4).
Ï
Check installation clearance. Verify there is a minimum probe insertion clearance of 4 feet
from the pipe surface.
Ð
Install the mounting hardware. Drill a 1½” through hole and weld the thread-o-let onto the
condenser vacuum pipe (See Figure 4). Thread the hot-tap assembly into the thread-o-let. Use
thread tape or pipe dope to seal the connection.
Ñ
It should be convenient to apply a restrictive or pulling force of between 9 and 11 lbs to
remove or replace the probes under plant operating conditions.
2.4 PROBE INSTALLATION
Î
Check proper installation direction. The probe has a directional arrow on the tag and/or etched
into a metal part. Before installing the unit, note proper flow direction. This is important to
instrument operation.
Ï
Check serial number of the probe. Choose a location for each probe (always reinstall probe
to same location). Custom labeling of the
SENTRY
screen with probe serial numbers or other
I.D. is possible - see Section 3.3.
Ð
Verify stop clamp location (see Figure 3). A stop clamp is attached to each probe as an
indication of its insertion depth. It is important this stay in place in
order for the probe to be installed correctly and to ensure the end of
the probe does not contact the opposing pipe wall. The clamp’s
location is determined based on the diameter of each pipe, as shown
in
SECTION 6.2
, and is marked with a groove on the probe’s shaft.
Refer to this mark if the stop clamp is inadvertently moved.
Ñ
Inspect the probe tips. Be sure wetted surfaces are clean before
installing. If cleaning is needed, use a damp cloth wetted with alcohol
and wipe dry using a soft, lint-free cloth. Do not immerse probe in
liquid alcohol or any other liquids.
Ò
Install the probes. Each probe should be mounted through the pipe
wall using a hot-tap assembly. The probe installs so that the two probe
tips (visible in the probe head) are side-by-side across the gas stream.
The probe has a flow directional arrow on the tag. When installing
under vacuum, do not allow the clamp to "slam" against the seal nut
upon opening the valve. Grasp the probe shaft firmly before opening
the ball valve. Allow the probe to slide through the valve by
controlling the amount of grip on its shaft. Special installation
instructions, if any, will be noted in
SECTION 6
.
Summary of Contents for RheoVac
Page 10: ... 8 Probe Installation Detail ...
Page 13: ... 11 Figure 6 CPU Wiring Part 1 ...