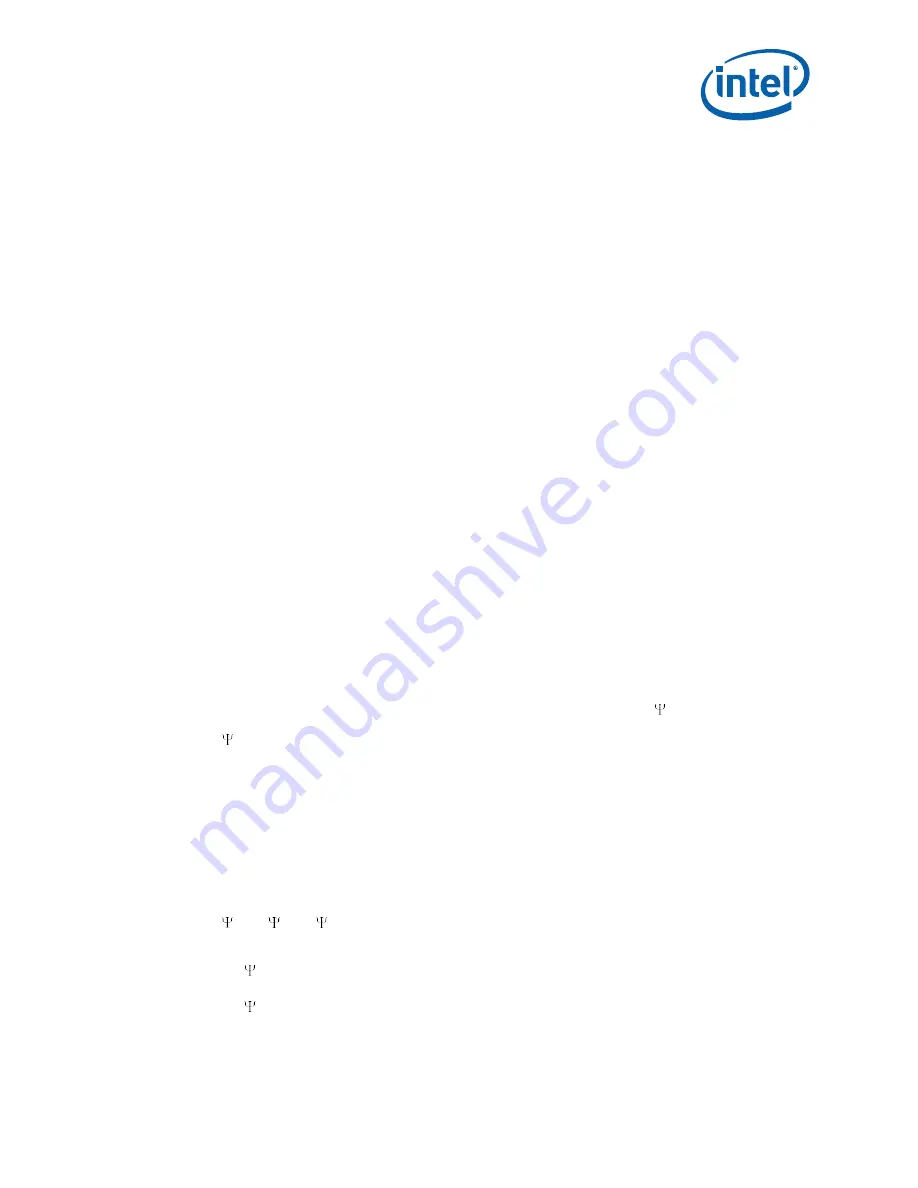
Thermal/Mechanical Design Guide
35
Thermal Solutions
5.3.1
Thermal Interface Material (TIM)
TIM should be verified to be within its recommended shelf life before use.
Surfaces should be free of foreign materials prior to application of TIM.
Use isopropyl alcohol and a lint free cloth to remove old TIM before applying new TIM.
5.4
Structural Considerations
Mass of the 1U reference heatsink and the target mass for 2U and Tower heatsinks
does not exceed 500 gm.
From
Table 4-3
, the Dynamic Compressive Load of 200 lbf max allows for designs that
exceed 500 gm as long as the mathematical product does not exceed 200 lbf. Example:
A heatsink of 2-lb mass (908 gm) x 50 g (acceleration) x 2.0 Dynamic Amplification
Factor = 200 lbf. The Total Static Compressive Load (
Table 4-3
) should also be
considered in dynamic assessments.
The heatsink limit of 500 gm and use of back plate have eliminated the need for Direct
Chassis Attach retention (as used previously with the Intel® Xeon® processor 5000
sequence). Direct contact between back plate and chassis pan will help minimize board
deflection during shock.
Placement of board-to-chassis mounting holes also impacts board deflection and
resultant socket solder ball stress. Customers need to assess shock for their designs as
their heatsink retention (back plate), heatsink mass and chassis mounting holes may
vary.
5.5
Thermal Design
5.5.1
Thermal Characterization Parameter
The case-to-local ambient Thermal Characterization Parameter (
CA
) is defined by:
Equation 5-1.
CA
= (T
CASE
- T
LA
) / TDP
Where:
T
CASE
=
Processor case temperature (°C). For T
CASE
specification see the
appropriate datasheet.
T
LA
=
Local ambient temperature in chassis at processor (°C).
TDP
=
TDP (W) assumes all power dissipates through the integrated heat
spreader. This inexact assumption is convenient for heatsink design.
TTVs are often used to dissipate TDP. Correction offsets account for
differences in temperature distribution between processor and TTV.
Equation 5-2.
CA
=
CS
+
SA
Where:
CS
=
Thermal characterization parameter of the TIM (°C/W) is dependent
on the thermal conductivity and thickness of the TIM.
SA
=
Thermal characterization parameter from heatsink-to-local ambient
(°C/W) is dependent on the thermal conductivity and geometry of the
heatsink and dependent on the air velocity through the heatsink fins.
Figure 5-4
illustrates the thermal characterization parameters.
Summary of Contents for X5550 - Quad Core Xeon
Page 8: ...8 Thermal Mechanical Design Guide ...
Page 12: ...Introduction 12 Thermal Mechanical Design Guide ...
Page 24: ...Independent Loading Mechanism ILM 24 Thermal Mechanical Design Guide Figure 3 3 ILM Assembly ...
Page 26: ...Independent Loading Mechanism ILM 26 Thermal Mechanical Design Guide ...
Page 48: ...Component Suppliers 48 Thermal Mechanical Design Guide ...
Page 82: ...Mechanical Drawings 82 Thermal Mechanical Design Guide ...
Page 88: ...Socket Mechanical Drawings 88 Thermal Mechanical Design Guide ...