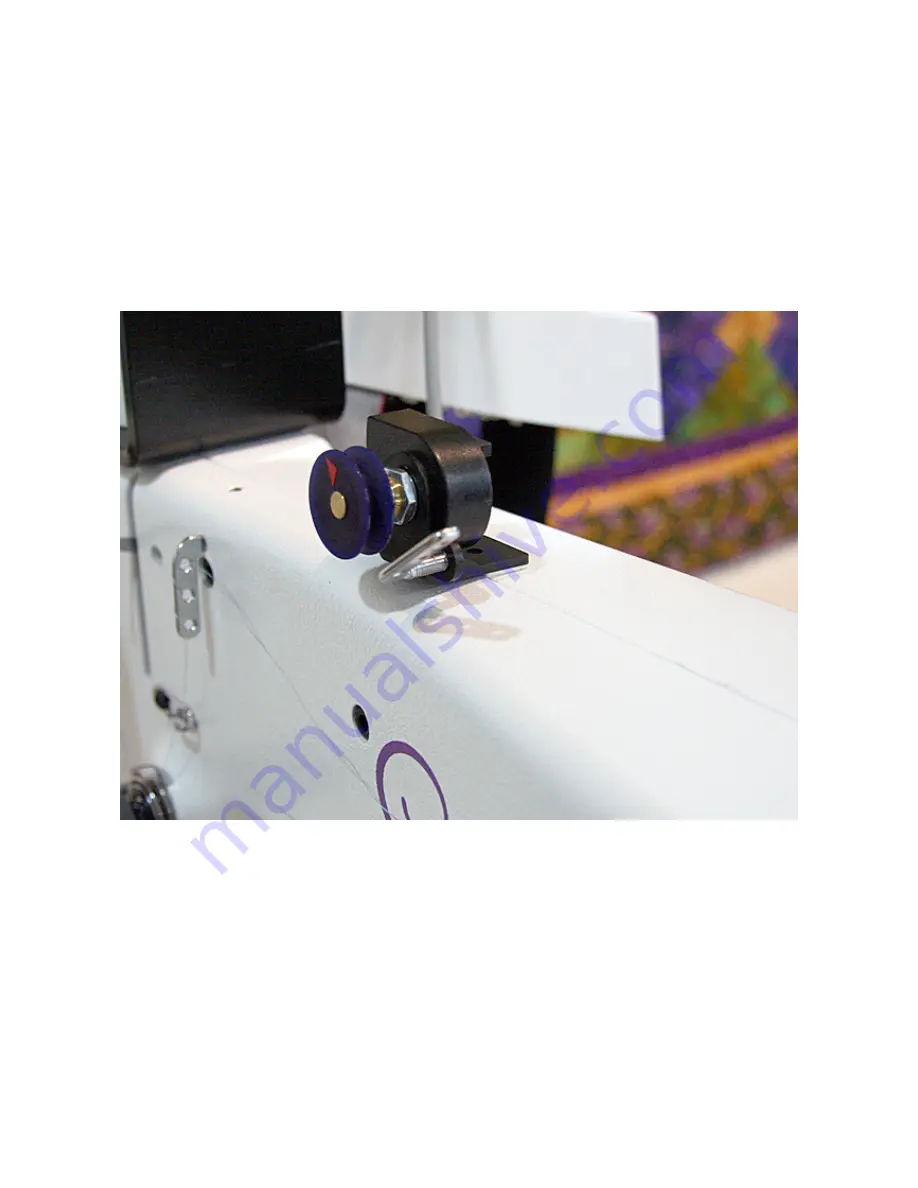
5
3. THREAD BREAK DETECTOR
Position the thread break detector on the top of the arm, so the hole in the bracket
is about 7" (178mm) from the rear edge of the head and the whole adhesive pad is
beyond the separation line (see Fig. 5). Mark the position of the edge of the bracket.
Fig. 5
Clean the surface where the bracket will be placed with alcohol.
Remove the clear protective foil from the double-sided tape on the bracket and push
it firmly to the surface, making sure that it sticks only to the left side of the body
(viewed from the front). Set the wheel position so it is aligned with the thread path.
Note the proper threading direction: it should be wrapped around the wheel
clockwise.