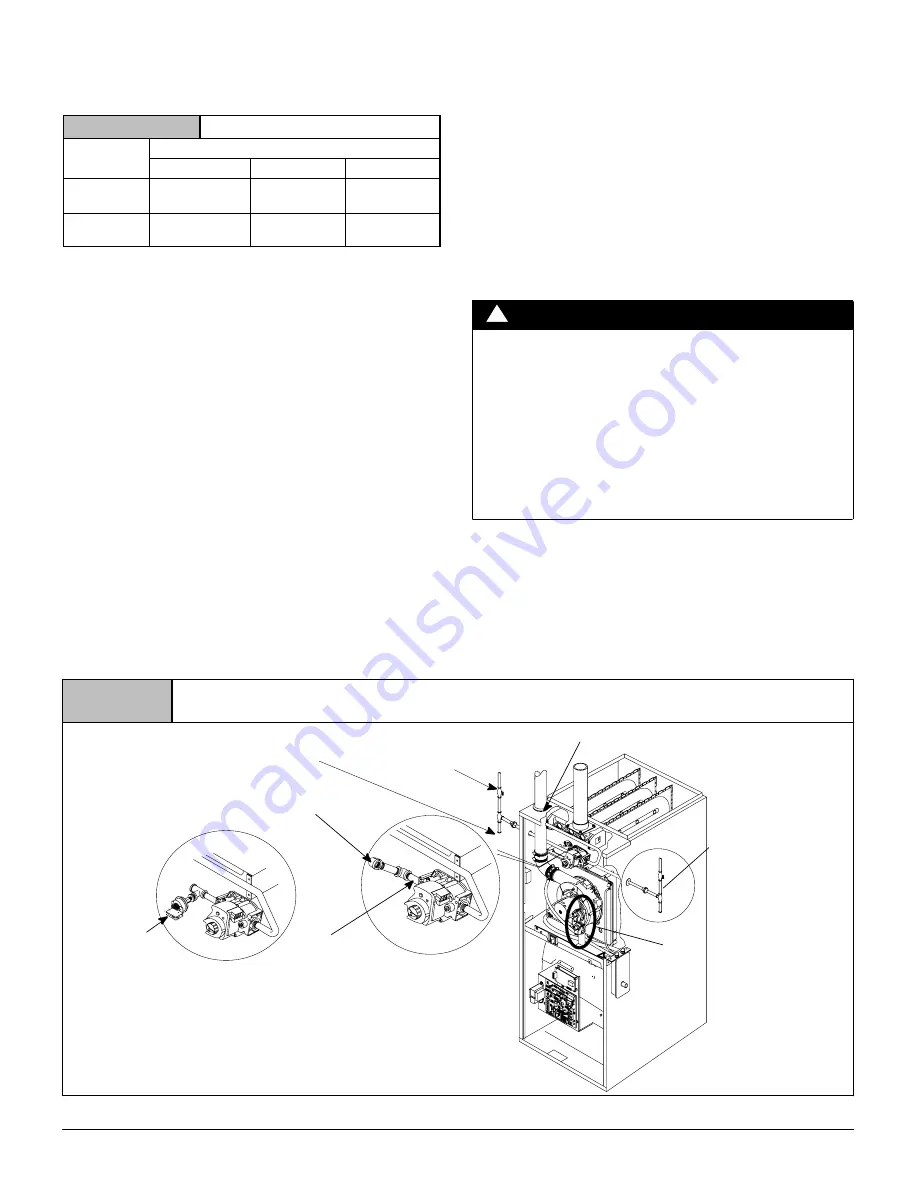
35
440 01 1051 02
Specifications are subject to change without notice.
•
Do not allow minimum supply pressure to vary downward.
Doing so will decrease input to furnace. Refer to
Table 5
for
Gas supply. Refer to
Table 6
or
Table 7
for manifold
pressures.
Table 5
Gas Pressures
Gas Type
Supply Pressure
Recommended
Max.
Min.
Natural
7 in wc
(1.8 kPa)
14 in wc
(3.5 kPa)
4.5 in wc
(1.1 kPa)
Propane
11 in wc
(2.8 kPa)
14 in wc
(3.5 kPa)
11 in wc
(2.8 kPa)
Gas Piping Requirements
NOTE:
The gas supply line must be installed by a qualified service
technician in accordance with all building codes.
NOTE:
In the state of Massachusetts.
a. Gas supply connections MUST be performed by a
licensed plumber or gas fitter.
b. When flexible connectors are used, the maximum length
shall not exceed 36
″
(915 mm).
c.
When lever handle type manual equipment shutoff
valves are used, they shall be T
−
handle valves.
d. The use of copper tubing for gas piping is NOT approved
by the state of Massachusetts.
1. Install gas piping in accordance with local codes, or in the
absence of local codes, the applicable national codes. Refer
to NFPA 54/ANSI Z223.1 for proper gas pipe size.
2. It is recommended that a manual equipment shutoff valve be
installed in the gas supply line outside the furnace. Locate
valve as close to the furnace as possible where it is readily
accessible. Refer to
Figure 37.
3. Use black iron or steel pipe and fittings or other pipe approved
by local code.
4. Use pipe thread compound which is resistant to natural and
Propane gases.
5. Use ground joint unions and install a drip leg no less than 3
″
(76.2mm) long to trap dirt and moisture before it can enter gas
control valve inside furnace.
NOTE:
Refer to
Figure 37
and
Figure 38
for the general layout at
the furnace. The rules listed apply to natural and Propane gas pipe
installations.
NOTE:
Install the gas pipe grommet to the furnace side panel with
the gas pipe entry. If needed, remove the 2” (50.8mm) hole plug
from the plastic accessory bag and relocate to the open hole in the
furnace side panel.
6. Use two pipe wrenches when making connections to
prevent gas valve from turning.
7. Install a manual shut
−
off valve external to furnace casing
and tighten all joints securely.
8. If local codes allow the use of flexible gas appliance
connectors, always use a new listed connector.
Do not use a connector which has previously serviced
another gas appliance.
FIRE OR EXPLOSION HAZARD
Failure to follow this warning could result in
personal injury, death, and/or property damage.
A flexible corrugated metal gas connector must be
properly installed, shall not extend through the side
of the furnace,and shall not be used inside the
furnace.
Black iron pipe shall be installed at the furnace gas
control valve and extend a minimum of 2
(50.8mm)
outside furnace casing.
!
WARNING
9. Flexible
corrugated metal gas connector may
NOT
be used
inside the furnace or be secured or supported by the furnace
or ductwork.
10. Properly size gas pipe to handle combined appliance load
or run gas pipe directly from gas meter or Propane gas
regulator.
11. Install correct pipe size for run length and furnace rating.
12. Measure pipe length from gas meter or Propane second
stage regulator to determine gas pipe size.
ON
OFF
ON
OFF
ON
O
FF
* Union may be installed inside the cabinet when necessary
because of clearances.
Figure 37
Typical Gas Piping for Upflow
Drip Leg and Union, Union* should be outside the
cabinet. Manual shut-off valve MUST be upstream of
dripleg, union, and furnace.
Propane Low pres
sure switch
REQUIRED.
25
−
24
−
86
Vent Pipe Grommet (Single Pipe)
3
(76.2mm)
pipe
nipple
Models may
have 1 or 2
pressure
switches
Manual shut-off
valve
Alternative
installation
Representative drawing only, some models may vary in appearance.
Use elbows and 3
″
(76.2mm) pipe nipple to connect valve to
piping when using right side gas pipe entry.