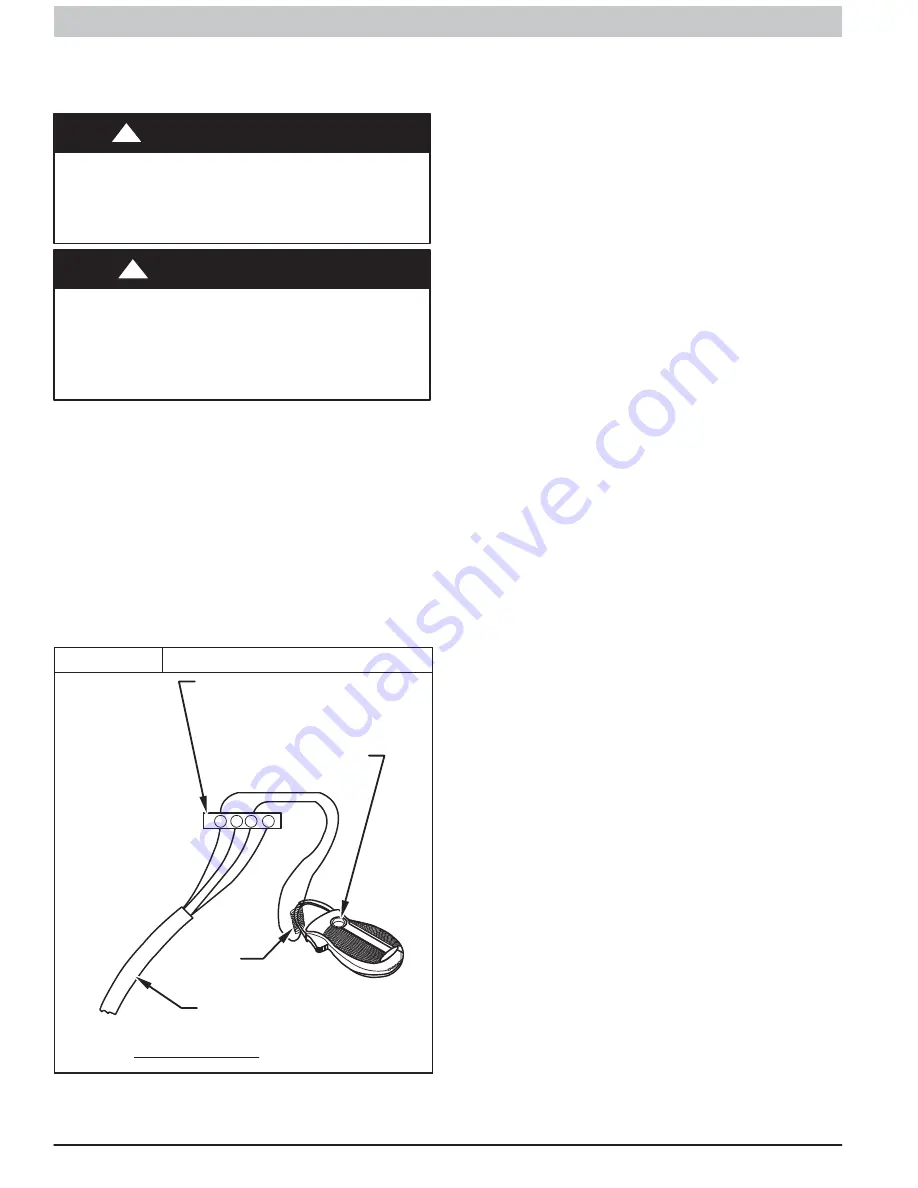
SERVICE AND TECHNICAL SUPPORT MANUAL
Gas Furnace: (F/G)9MXT
Specifications subject to change without notice.
10
440 04 4321 02
Adjust Continuous Fan Airflow
The Continuous Fan airflow can be set from the remaining
blower speed taps. Refer to the Air Delivery Tables in these
instructions.
FIRE HAZARD
Failure to follow this warning could result in personal injury,
death, and/or property damage.
Reinstall manifold pressure tap plug in gas valve to
prevent gas leak.
!
WARNING
FURNACE OVERHEATING HAZARD
Failure to follow this caution may result in reduced furnace
life.
Recheck temperature rise. It must be within limits specified
on the rating plate. Recommended operation is at the
midpoint of rise range or slightly above.
CAUTION
!
Adjust Thermostat Heat Anticipator
When using a nonelectronic thermostat, the thermostat heat
anticipator must be set to match the amp draw of the electrical
components in RW circuit. Accurate amp draw readings can
be obtained at the thermostat subbase terminals R and W.
Figure 5
illustrates the easy method of obtaining actual amp
draw. The amp reading should be taken after blower motor has
started and furnace is heating. Connect ammeter wires as
shown in
Figure 5
. The thermostat anticipator should not be in
the circuit while measuring current. If thermostat has no
subbase, the thermostat must be disconnected from R and W
wires during current measurement. See thermostat
manufacturer’s instructions for adjusting heat anticipator and for
varying heating cycle length. For an electronic thermostat, set
cycle rate for 3 cycles per hour.
Figure 5
Amp. Draw Check with Ammeter
A96316
R Y W G
10 TURNS
THERMOSTAT SUBBASE
TERMINALS WITH
THERMOSTAT REMOVED
(ANITICIPATOR, CLOCK, ETC.,
MUST BE OUT OF CIRCUIT.)
HOOKAROUND
AMMETER
EXAMPLE:
5.0 AMPS ON AMMETER
10 TURNS AROUND JAWS
=
FROM UNIT 24V
CONTROL TERMINALS
Check Safety Controls
The flame sensor, gas valve, and pressure switch were all
checked in the Startup procedure section as part of normal
operation.
1. Check Main Limit Switch
This control shuts off combustion system and energizes
aircirculating blower motor, if furnace overheats. By
using this method to check limit control, it can be
established that limit is functioning properly and will
operate if there is a restricted returnair supply or motor
failure. If limit control does not function during this test,
cause must be determined and corrected.
a. Run furnace for at least 5 minutes.
b. Gradually block off return air with a piece of
cardboard or sheet metal until the limit trips.
c. Unblock return air to permit normal circulation.
d. Burners will relight when furnace cools down.
2. Check Pressure Switch(es)
This control proves operation of the draft inducer blower.
a. Turn off 115V power to furnace.
b. Disconnect inducer motor lead wires from wire
harness.
c. Turn on 115V power to furnace.
d. Set thermostat to “call for heat” and wait 1 minute.
When pressure switch is functioning properly, hot
surface igniter should
NOT
glow and control
diagnostic light flashes a status code 3. If hot surface
igniter glows when inducer motor is disconnected,
shut down furnace immediately.
e. Determine reason pressure switch did not function
properly and correct condition.
f. Turn off 115V power to furnace.
g. Reconnect inducer motor wires, replace outer door,
and turn on 115V power.
h. Blower will run for 90 seconds before beginning the
call for heat again.
i. Furnace should ignite normally.
Checklist
1. Put away tools and instruments. Clean up debris.
2. Verify that the jumper is removed from the TEST/TWIN
terminal. Verify that there is nothing plugged into the PLT
connector.
NOTE
: Note: If there is a jumper connector plugged into PLT,
remove it and discard. (See
Figure 4
)
3. Verify that (TT) switch SW-1 is set properly. (See
Figure 4)
4. Verify that the Heat OffDelay SW2 and SW3 switches
are set as desired. (See
Figure 4)
5. Verify that the blower and control (“Main”) doors are
properly installed.
6. Verify that the Status LED glows. If not, check that the
power supply is energized and that the blower door is
secure. (See
Figure 14
) to interpret diagnostic codes.
7. Cycle test furnace with room thermostat to be sure that it
operates properly with the room thermostat. Check all
modes including Heat, Cool and Fan.
8. Check operation of accessories per manufacturer’s
instructions.
9. Review Home Owner’s Information with owner.
10. Attach entire literature packet to furnace.