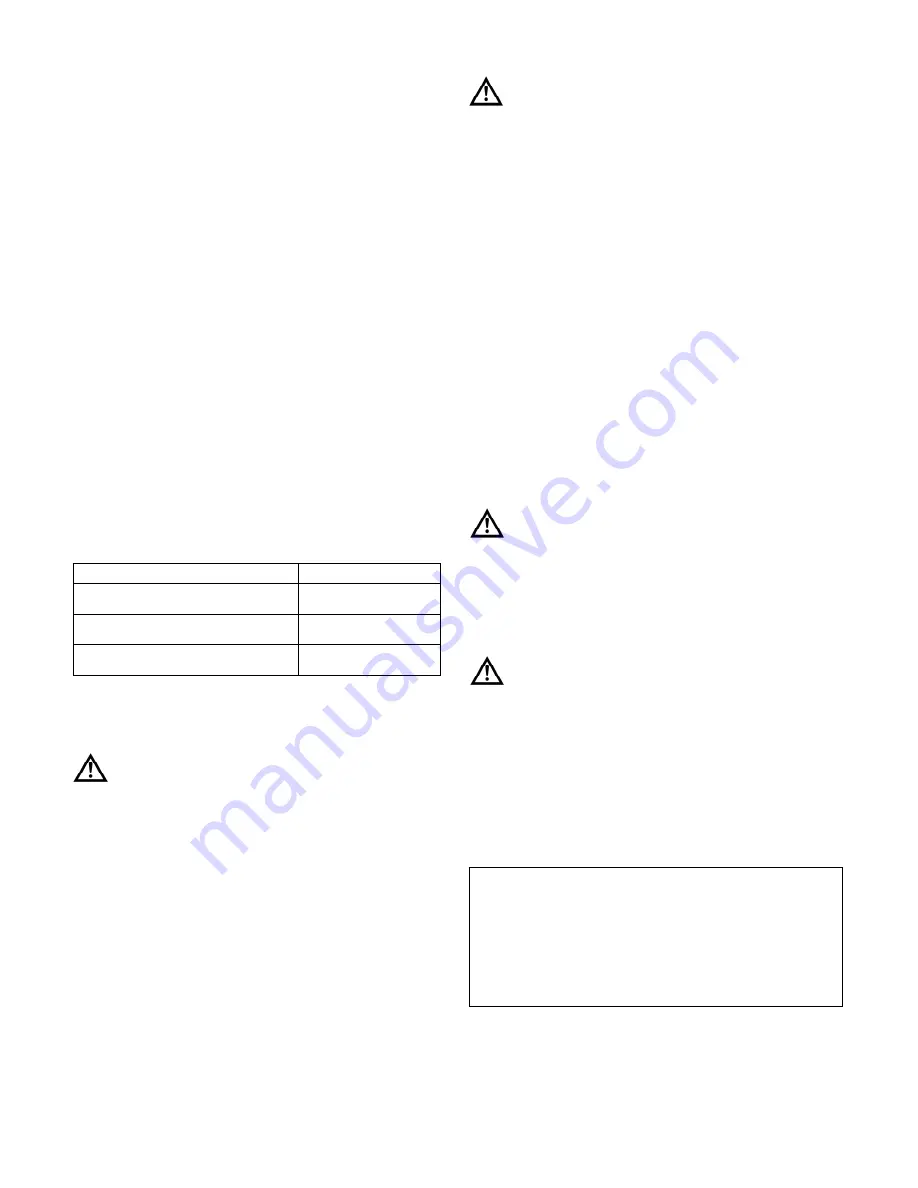
- 8 -
3.1.9- Lubricate the O-ring pos. 13 and place it into the seat of
the reduction gear casing pos. 2.
3.1.10- Join the two parts of the reduction gear matching the
reduction gear casing pos. 2 with the reduction gear cover pos.
14. Take care that the O-ring pos. 13 stays in place correctly.
Position the toothing of the crown gear and of the pinion gear so
as to make the mesh and the coupling easier.
3.1.11- Fix the reduction gear casing pos. 2 to the reduction gear
cover pos. 14 by means of the nine screws pos. 21 and tighten
(torque wrench setting 20 Nm).
3.1.12- Screw down the oil drain cap pos. 20 (torque wrench
setting 40 Nm) into the lower port of the reduction gear casing
pos. 2.
3.1.13- Make the first oil filling by the oil dipstick cap hole pos. 8
up to the middle of the oil window cap pos. 1. Approximately
0.28 litres are needed. (See paragraph “LUBRICATING OIL”).
3.1.14- Screw down the oil dipstick cap pos. 8.
3.2- Coupling to the engine:
3.2.1- Lubricate the engine shaft with grease in order to make
the assembly easier and prevent contact oxidation.
3.2.2- Center and couple the reduction gear/pump assembly to
the engine by means of the flange taking care that the shaft and
the hole are correctly aligned. See table of “TECHNICAL
FEATURES” in order to choose the flange to be used with the
engine. Make sure that the feather key is present on the engine
shaft.
3.2.3- Do not force and/or damage the coupling of the engine
shaft to the reduction gear pinion hole due to incorrect actions.
3.2.4- In order to obtain a good centering and a correct
functioning we suggest you use engine shafts with the following
machining tolerances for the shaft end:
Pinion
Engine shaft
Cod. 10023355 - Ø25.4 G7
(+0.007/+0.028)
Ø25.4 f7 (-0.02/-
0.041)
Cod.10031255 - Ø25 H7
(0/+0.021)
Ø25 f7 (-0.02/-
0.041)
Cod.10027155 - Ø28.6 H7
(0/+0.021)
Ø28.6 f7 (-0.02/-
0.041)
3.2.5- Fix the reduction gear/pump assembly to the engine by
means of the four screws pos. 6 or 7 (see engine flange), of the
washer pos. 3 and the washer pos. 4 or 5 and tighten (torque
wrench setting as stated in the exploded view).
IMPORTANT: The pump must be fixed to the reduction
gear only, therefore it must be suspended during
working.
4- LUBRICATING OIL
4.1- For the inside lubrication use gear drive oils with cSt
40°C
≥
180 viscosity, better if containing addition agents in order
to grant an excellent level of protection against wear, against
foaming and to provide high oxidation and corrosion strength.
We suggest you use ISO VG 220 DIN 51519 quality oils (or with
80W-90 SAE degree).
4.2- These oil types are valid for room temperatures between
0°C and 30°C. In case of different temperatures, please contact
the after-sales service of Interpump Group.
4.3- Oil change
4.3.1- The oil change must be carried out when the reduction
gear is at a working temperature.
4.3.2- Place a container under the drain plug pos. 20.
4.3.3- Remove the oil dipstick cap pos. 8 and then the drain plug
pos. 20.
4.3.4- Wait until all the oil has been drained, then screw back the
drain plug pos. 20 (torque wrench setting as stated in the
exploded view).
4.3.5- Fill with fresh oil up to the middle of the oil window cap
pos. 1 and screw back the oil dipstick cap pos. 8.
IMPORTANT: The exhausted oil must be gathered in
containers and disposed of contacting the authorized
centres as established by the laws in force. The oil must
not be dispersed in the environment for any reason.
5- MAINTENANCE
5.1- Maintenance and repair must be carried out by qualified and
authorized staff only. Before any operation, make sure that the
engine-reduction gear- pump assembly is shut down and made
unusable.
5.2- A correct maintenance helps extend the working life and
grants a better performance of the reduction gear.
5.3- Scheduled maintenance
5.3.1- After 50 working hours:
Change the oil after 50 working hours from the first use.
Afterwards, the oil must be changed every 1000 working hours
or once a year (See paragraph “Oil change”).
5.3.2- Every 500 hours
Check the oil window pos. 1 to verify the oil level. If necessary,
add the oil up to the middle of the oil window. In case of a
substantial decrease in the oil level, check that there are no
leakages or drippings caused by an excessive wear or by
breakings.
5.4- Replace the reduction gear parts with original spare
parts only. Use only oil types as stated in the above
paragraph.
IMPORTANT: After maintenance, we suggest you
change the lubricating oil. Moreover, make sure that the
reduction gear is re-assembled correctly and that the
initial conditions are restored. If necessary, comply with
the instructions contained in the above paragraph
“ASSEMBLY AND INSTALLATION”.
5.5- In case of disposal, we suggest you take the reduction gear
to an authorized disposal centre or contact the nearest
INTERPUMP GROUP Authorized Service Centre.
IMPORTANT: The reduction gear shall not be tampered
with for any reason and/or used for any purpose other
than the use it has been designed for. In case of
tampering, the manufacturer disclaims all responsibility
as to the reduction gear functioning and safety.
6- WARRANTY CONDITIONS
6.1- The period and conditions of warranty are specified in the
purchase contract.
6.2- Warranty is voided in case the reduction gear is used for
improper purposes, used at higher performances than the rated
ones, repaired with non-original spare parts or if it turns out to be
damaged due to the non-compliance with the operating
instructions or to unauthorized tampering.
Copyright - The content of these operating instructions is
property of Interpump Group.
The
instructions
contain
technical
descriptions
and
illustrations that cannot be copied and/or reproduced,
entirely or in part, nor distributed to third parties in any form
and without in any case authorized written consent of the
owner.
Offenders will be prosecuted according to the laws in force
and proper legal actions will be instituted against them.
The information contained in this document may be modified
without notice.