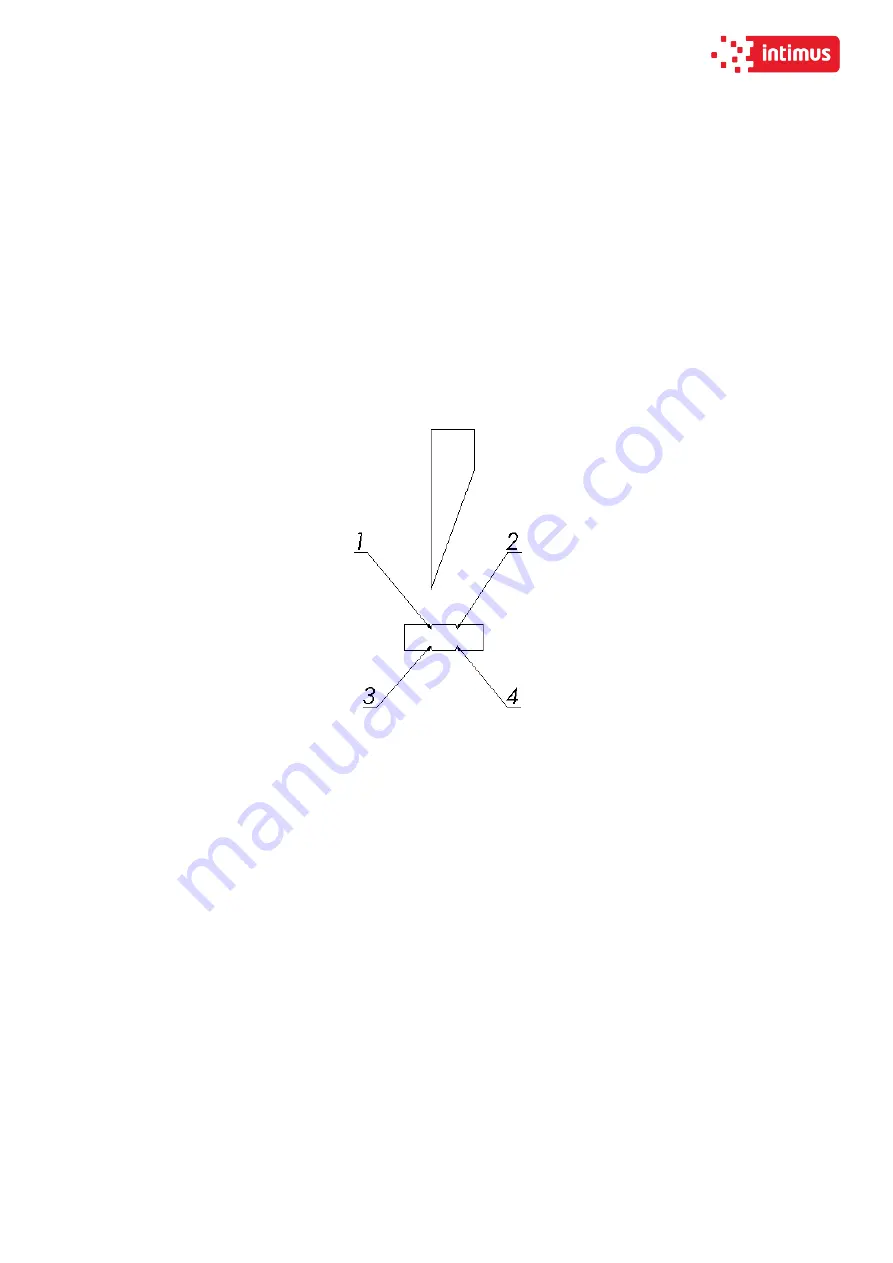
Operation Manual 5280 EPSP
54
2. Tables 2
3. Fixing pin
4. Screwdriver
8.2.1
Lift (lift) the cutting stick 1 with a screwdriver 4 (fig. 35)
8.2.2
Rotate or replace the cutting stick
8.2.3
. Insert the replaced stick into the channel between the tables 2 and place it on the
dowel 3 (Fig. 35)
Figure 36. Diagram of using the cutting stick
Rotation of the cutting stick in both planes gives the possibility of obtaining four lines
of contact with the knife, marked in Figure 36 as l, 2, 3, 4.