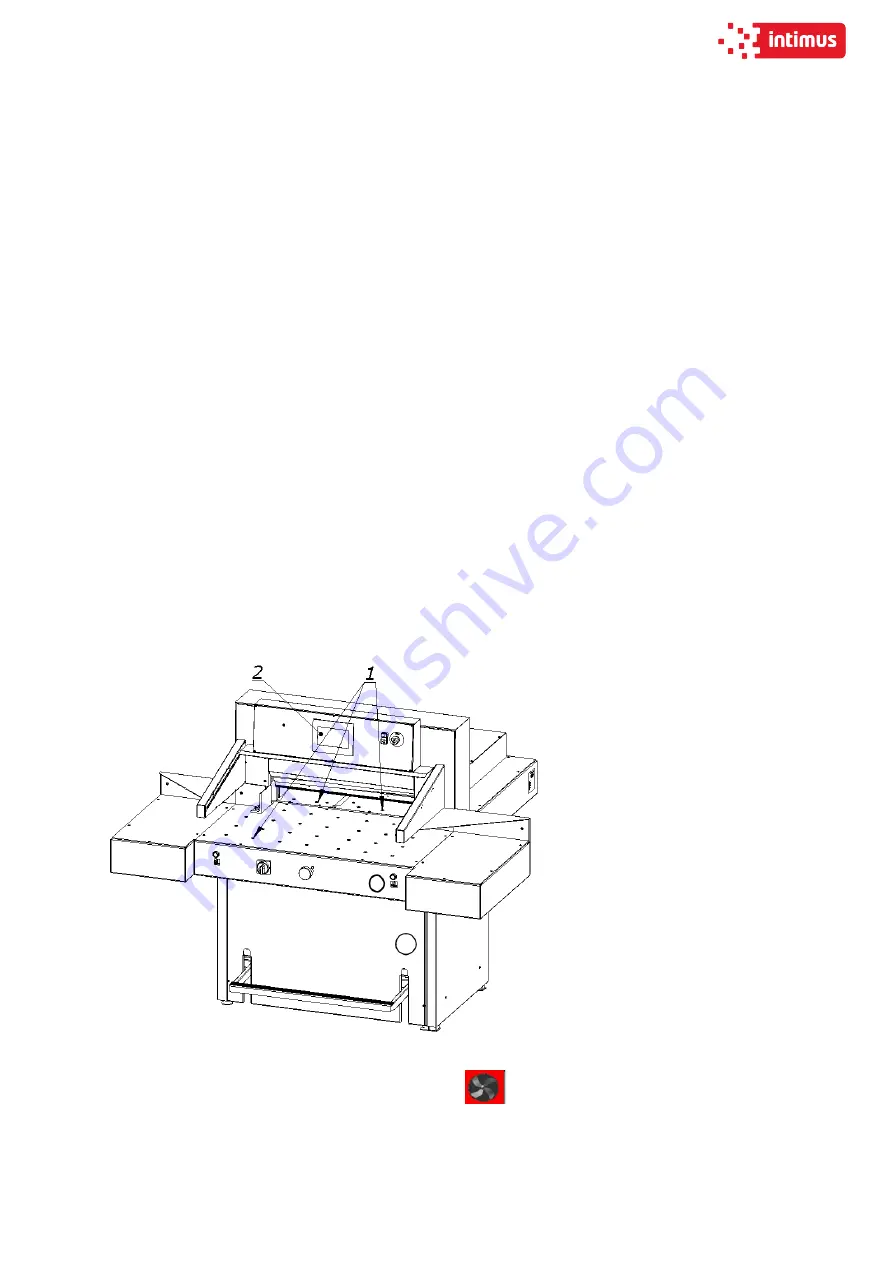
Operation Manual 7310 EPSHP
37
Cutting can be done if:
1. there is no object in the work area of the light barrier - the green OSSD 1 LED lights
up (Fig.11) on the receiver 1 (Fig.19).
2. the green push button switch 2 is pressed.
3. the two buttons 3 were pressed simultaneously.
Keep both buttons 3 until the material is cut.
The return of the knife and its stop in the upper return position and the movement of the
pressure beam upwards is automatic.
Releasing the buttons 3 during the movement of the pressure beam and the knife downwards
interrupts this movement. If an object gets caught in the light barrier working area, the
pressure beam and the knife will stop moving. To continue cutting, remove the unauthorized
item and simultaneously restart both buttons 3.
Paper clips or other hard objects can damage the blade!
7.8 Air Table
The surface of the cutter table is equipped with air nozzles 1 (fig.20.
Figure 20.
To turn on the air supply press the blower button
on the programmer 2 screen (Figure
20).
After switching on the air supply, moving the pile becomes easier. During the cutting,
pressing or manual pressing (testing), the air supply is switched off automatically
Summary of Contents for INT-GU-07310EPSHP
Page 5: ...Operation Manual 7310 EPSHP 5 EC Conformity Declaration...
Page 42: ...Operation Manual 7310 EPSHP 42 Figure 26 Figure 27...
Page 55: ...Operation Manual 7310 EPSHP 55 Figure 43 Adjusting elements of backguage...
Page 61: ...Operation Manual 7310 EPSHP 61 Figure 50 Lubrication point of the knife assembly lever...
Page 66: ...Operation Manual 7310 EPSHP 66 PROGRAM MODULE OPERATOR MANUAL DOP B07S410 7...